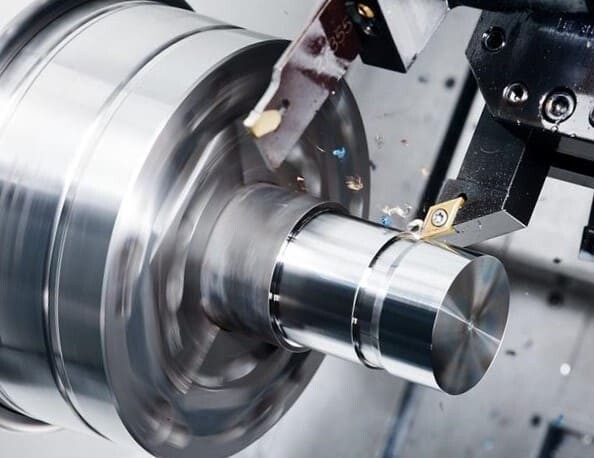
Rapid Prototyping & Rapid Manufacturing Expert
Specialize in CNC machining, 3D printing, urethane casting, rapid tooling, injection molding, metal casting, sheet metal and extrusion
Summing up everything about CNC turning
Today, research and development operations in many industries rely on CNC machining of parts or assemblies. CNC turning is a form of CNC machining used to create circular, cylindrical, tapered or other shaped parts or prototypes. Although its range of applications is not as popular as CNC turning, it is still a versatile and cost-effective manufacturing process that can produce a large number of parts in a variety of materials. In this article, we’ll take an in-depth look at what CNC turning is for, how it works, its advantages and disadvantages, and how it differs from other manufacturing processes such as milling or grinding.
1. What is CNC turning?
CNC turning is a manufacturing process in which a bar is held in a chuck and rotated while a tool is brought into contact with the workpiece at a set speed to remove material to create an axisymmetric part or prototype. The axis of rotation of CNC turning machines is divided into horizontal or vertical directions, and the latter is mainly used to manufacture relatively long parts with large radii. If the CNC lathe also has a milling function, it can allow other shapes of parts or components to be milled.
The selected material is usually a round bar, or other regular squares or hexagons.
Depending on the CNC lathe, the allowable bar length may be different.
The tools of the CNC lathe are installed in the rotatable drilling tower and controlled by the computer. The more tools in the turret, the more options there are for making complex parts.
CNC lathes can both cut the outside of the workpiece and drill holes from the inside to make tubular parts.

2. What is the function of CNC turning?
CNC turning is mainly used to manufacture axisymmetric parts, such as round shafts, hollow tubes, tapers, threaded rods or bushings, etc., while for CNC milling, it is relatively difficult to manufacture parts with circular contours. Parts manufactured by CNC turning have a very smooth surface finish and tight tolerances, even to within ± 0.0002 inches. Sometimes, the cooperation of CNC milling and CNC turning can greatly improve the efficiency. For example, CNC milling is performed on the parts after CNC turning. Machinists can further manufacture asymmetrical features on the parts to make full use of the advantages of the two manufacturing processes.

3. Key factors to be considered in CNC turning parts
The outer diameter of the part. CNC turning is often well suited for prototyping and low-volume production. A key factor to consider in determining whether CNC turning a part is the most cost-effective manufacturing method is the outside diameter (OD) of the part. The CNC lathe has a maximum limit on the outer diameter of the bar. When the outer diameter exceeds the maximum size allowed by the CNC lathe (such as 2.5 inches), it needs to be clamped separately, which may affect the delivery time and cost.
CNC tool. Another factor to focus on is CNC tools. No matter how thin or small the tool is, the cutting edge has a cylindrical character that leaves a radius when machining inside corners. For some parts with special characteristics, it is necessary to choose the most suitable CNC tool.
Part characteristics. For parts designed with undercuts, CNC turning is an effective solution. This can present some challenges for CNC milling, which requires longer special tools with the risk of chatter, loss of precision, poor surface finish, etc.
Asymmetric parts. For asymmetrical parts, CNC turning is not ideal.



4. Advantages of CNC turning
Reduce human error. Choosing a CNC turning service can greatly reduce human error. Once programmed and set up, the CNC lathe works automatically and can manufacture parts with the expected results.
Improve production efficiency.Most CNC lathes work at a relatively fast speed and can work for a long time without interruption. One operator can supervise the operation of multiple machines, which can help improve production efficiency without the need to hire additional labor.
Reduce the waste rate of materials. CNC lathes rarely waste materials or available resources, especially for precious metals, such as titanium, aluminum 7075, etc., effectively saving the total cost.
High precision.CNC turning has high machining accuracy and surface finish, and the manufactured parts are always of consistent quality.
5. Disadvantages of CNC turning
In addition to the advantages of CNC turning, we also need to consider some of its disadvantages. Of course, CNC turning requires more initial investment than manually operated turning.
Requires high setup cost
Higher technical requirements for mechanics and programming ability
Only cost-effective for axisymmetric parts
CNC lathes need maintenance and may not be able to fix the fault immediately
Weighing the features of CNC turning, the advantages far outweigh the disadvantages.
6. How CNC Turning Works
CAD/CAM design.The CNC turning process is all automated, but it is preceded by a digital representation of the part required for CAD/CAM design, which is then converted into G-code, the language of the CNC lathe. G-code guides the feed rate, rotation speed, tool change, etc. of the CNC machine tool. This can often be simulated on software such as AutoCAD Fusion’s MasterCAM that allows visualization of the manufacturing process from material to final product.


Turning process.Once the G-code is set up, the operator sets up and loads the turret. The turret can hold many tools at once. With the rods secured in place, the automated cutting of excess material begins until the desired part or prototype is manufact
7. CNC turning type
There are many different types of CNC turning such as turning, undercutting, knurling, drilling, facing, boring, etc. and different operations can be performed to obtain the desired shape. The following are common operations you use on your CNC turning projects.
During facing, a single-point tool moves radially or axially from the edge of the workpiece to evenly cut through thin layers of material, leaving a smooth surface. The cutting depth of the surface is generally relatively small, and it can be processed radially or axially at a single point.
Taper turning.Knife cutting cuts the material into a cone shape, where the diameter of the workpiece decreases or increases from one end to the other (think, for example, the shape of an hourglass).
Form turning.Cut material and create contoured parts with round, curved or smooth shaped knives.
Contour turning.Single-point cutters can machine round, curved, or smooth parts with continuous curves.
Chamfering.The chamfer is generally set to 45 degrees, in order to prevent damage to the sharp edge of the part or for safety. Chamfered edges are more resistant to damage than square or other sharp edges.
Partition.Use a special cutting tool to cut a groove straight until it is cut off.
Threading. Helical flutes are cut to match bolts of uniform thread specification.
Boring. Enlarge the existing aperture.
Drilling. The process of removing material from inside a workpiece to create a hole using a special auger drill.
Knurling. This is to cut straight lines, inclined lines, or cross zigzag patterns on the surface of the part, which can not only increase the friction of the part, but also improve the visual effect.
Grooving.The process of machining a narrow cavity in a part.



8. CNC turning compatible materials
CNC turning can be compatible with hundreds of materials, including various metals or plastics for you to choose. Choosing the right material is critical to making a custom part or prototype. We introduce several of the most widely used materials and note the common applicability of each material.
Aluminum. Aluminum is one of the most widely used materials for CNC turning, has an excellent strength-to-weight ratio, and is extremely resistant to corrosion. Aluminum parts can be anodized to further improve strength and corrosion resistance, and are available in a variety of colors to enhance visual aesthetics. CNC turning aluminum is widely used in aerospace, medical equipment, automotive parts or housings. Common aluminum alloy models include aluminum 5052, aluminum 7075, aluminum 7075-T6, aluminum 6063-T5, aluminum 7050-T7451, aluminum MIC-6, aluminum 6061-T6, aluminum 2024-T3, etc.

Steel.Because steel has excellent strength and hardness, it is often used in high-stress, friction-resistant parts, such as gears and shafts. Common steel types are alloy steel 4130, alloy steel 4140, ASTM A36, steel 1018, steel A36, etc.

Stainless steel. After heat treatment, stainless steel has excellent strength and corrosion resistance, and is widely used in aerospace, medical equipment, food and other fields. Common stainless steel models are, stainless steel 15-5, stainless steel 17-4, stainless steel 18-8, stainless steel 303, stainless steel 304, stainless steel 316/316L, stainless steel 416, stainless steel 420.

Titanium.Titanium has excellent strength, corrosion resistance, biocompatibility, and is very suitable for the manufacture of medical implants, aircraft and other fields. The most commonly used titanium alloy is titanium 6Al-4V.

Summary of common metal materials for CNC turning
Aluminum | Stainless steel | Mild, Alloy & Tool steel | Other metal |
6061-T6 | 303 | Mild steel 1018 | Brass C360 |
6082 | 304L | Mild steel 1045 | Copper C101 |
7075-T6 | 316L | Alloy steel 1215 | Copper C110 |
5083 | 2205 Duplex | Mild steel A36 | Titanium Grade 1 |
5052 | 17-4 | Alloy steel 4130 | Titanium Grade 2 |
2014 | 15-5 | Alloy steel 4140 | Invar |
2017 | 416 | Alloy steel 4340 | Inconel 718 |
2024 | 420 | Tool Steel A2 | Magnesium AZ31B |
6063 | 430 | Tool Steel A3 |
|
7050 | 440C | Tool Steel D2 |
|
A380 | 301 | Tool Steel S7 |
|
MIC 6 |
| Tool Steel H13 |
|
|
| Tool Steel O1 |
There are also many options for CNC turning common plastic materials.
PVC.PVC is a low-cost material with good corrosion resistance and chemical resistance. It can be used in a wide range of applications, from children’s toys to gas pipelines.
Nylon.Nylon is a versatile, low-cost plastic that is heat, chemical and abrasion resistant, can replace metal in some cases, and can be used to create high-strength and close-tolerance parts.
Plastics | Reinforced Plastic |
ABS | Garolite G-10 |
Polypropylene | Polypropylene (PP) 30%GF |
Nylon 6 | Nylon 30%GF |
Delrin (POM-H) | FR-4 |
Acetal (POM-C) | PMMA (Acrylic) |
PVC | PEEK |
HDPE |
|
UHMWPE |
|
Polycarbonate |
|
PET |
|
PTFE (Teflon) |
9、CNC turning design guidelines
Summarizes recommended and technically feasible values for common features of CNC turned parts.
Feature | Recommended size | Feasible size |
Min. feature size | Ø 2.5 mm | Ø 0.5 mm |
Internal edges | R 8 mm | R 0.25 mm |
Minimum wall thickness | 0.8 mm (for metals) | 0.5 mm (for metals) |
Holes | Diameter:standard drill bit sizes | Diameter: Ø 0.5 mm |
Threads | Size: M6 or larger | Size: M2 |
10. Surface treatment process of CNC turning parts
CNC turning parts have a variety of surface treatment processes to choose from. According to the summary of DDPROTOTYPE, a top prototype manufacturer in China, the more common post-treatments are as follows.
As-Machined (Ra 3.2μm / Ra 126μin).This is the standard most cost-effective surface preparation process with the tightest tolerances, deburring and chamfering if necessary.

Finishing (Ra 1.6μm /0.8μm).Usually the finished parts have a smooth surface finish, the traces are not obvious, and there is no need for manual polishing.

Sandblasting.Glass beads are sprayed onto the surface of the part using high pressure to create a grainy texture.

Brushed + Anodized Type II (glossy finish). A brushed finish prior to Type II anodizing gives the part a glossy color, increased hardness, and corrosion resistance.

Sandblasted + Anodized Type II (Matte). Grit blasted and Type II anodized parts have good corrosion resistance.

Anodizing type III (hard anodizing). Parts anodized Type III have better corrosion and wear resistance.

Powder coating. Powder coating works on all metals to form a strong, wear-resistant layer on the surface of the part.

Wire drawing + electropolishing (Ra 0.8μm / Ra 32μin). Brushed and electropolished parts have a smooth and well-groomed finish.
Black oxide.A surface treatment process suitable for steel, which is used to improve the corrosion resistance of steel parts and can effectively reduce reflection.
Chromate conversion coating.Applying a chromate conversion coating to a part increases corrosion resistance while maintaining its electrical conductivity. RoHS compliant.
Wire drawing (Ra 1.2μm / Ra 47μin). Reducing the surface roughness of the part with #400 – 600 sandpaper improves the visual quality.
Polished (Ra 0.8μm / Ra 32μin). The surface of the part is manually polished in multiple directions to further improve the surface finish and slightly reflective.
11. Tolerance of CNC turning
If there is no special specification, CNC turning generally follows the ISO2768 standard. It is worth noting that the tolerance of the nominal size below 0.5 mm needs to be clearly indicated on the drawing.
Limits for nominal size | Plastics (ISO 2768- m) | Metals (ISO 2768- f) |
0.5mm* to 3mm | ±0.1mm | ±0.05mm |
Over 3mm to 6mm | ±0.1mm | ±0.05mm |
Over 6mm to 30mm | ±0.2mm | ±0.1mm |
Over 30mm to 120mm | ±0.3mm | ±0.15mm |
Over 120mm to 400mm | ±0.5mm | ±0.2mm |
Over 400mm to 1000mm | ±0.8mm | ±0.3mm |
Over 1000mm to 2000mm | ±1.2mm | ±0.5mm |
Over 2000mm to 4000mm | ±2mm |