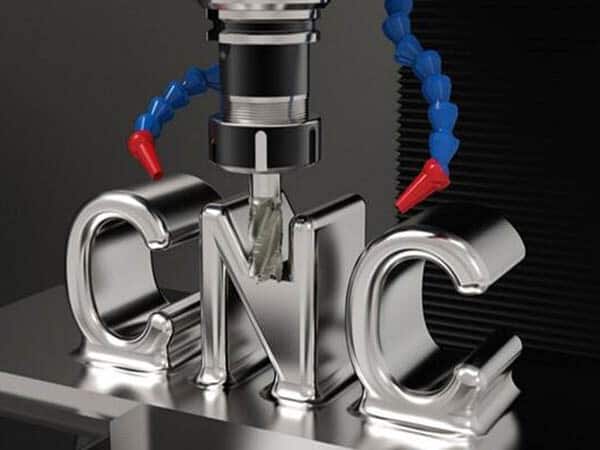
Rapid Prototyping & Rapid Manufacturing Expert
Specialize in CNC machining, 3D printing, urethane casting, rapid tooling, injection molding, metal casting, sheet metal and extrusion
How to reduce the cost of CNC machining
CNC machining is still one of the most popular ways to create rapid prototyping and low-volume manufacturing, with high precision and repeatability, it can process almost any type of materials, and is widely trusted by designers. In the short term, it is difficult to have better technology to surpass CNC machining. Before developing new products, enterprises usually consider how to reduce the budget. So it is very important to reduce the cost of CNC machining in the early stage of prototype creation. The secret to reduce the cost of CNC machining is to reduce the machining time as much as possible. In the process of following the designer’s 3D drawings, the less the machining time, the lower the cost of parts.
Planning is very important for CNC machining. People who don’t know about it may think that it’s a simple and cheap thing to create a prototype with a highly automated, fast and repeatable process. This is not the case. If there is no early scientific planning in terms of materials, machining difficulty, precision, quantity, etc., the price of a prototype may reach hundreds of dollars, or even more. DDPROTOTYPE has 15 years of CNC machining experience, providing rapid prototyping and low-volume manufacturing services to more than 270 customers in more than 30 countries around the world, summarizing various factors to reduce CNC machining costs.

1. Material factor
In CNC machining a prototype, of course, we need to consider what materials to use, each material has its unique performance, cost, machining difficulty. Some of our common materials, such as aluminum, ABS and so on, are popular because they are easy to process and cheap. For example, the price of a 6061 aluminum plate is about $25, the price of 304 stainless steel is $150, and the price of precision grinding 316 stainless steel is as high as $320. In general, you should choose the cheapest material to meet the functional requirements of your design. For some functional prototypes, first consider aluminum or ABS, which can greatly reduce the cost. If it’s a medical prototype that needs to be implanted in the human body, then it has to be made of stainless steel or titanium. Of course, the difficulty of machining, each material is different, easy to process materials, will greatly shorten the processing time. To produce a stainless steel prototype, we need more advanced CNC machines, harder cutting tools, etc. Therefore, when machining the same functional prototype and selecting different materials, the final price varies greatly.


2. Reduce setup time
Before the machining is decided, the machinist needs to set up a program to command the cutter to walk according to the planned route. In ddprototype, CNC milling parts generally adopt 3-axis and 5-axis CNC machining. In order to reduce the cost, the 3-axis is usually preferred, so that the part can only be machined on one side at a time, except for the machining profile. For the next side, CNC machines needs to be shut down and manually turned to the other side, which increases the processing risk and additional processing time. In this process, more standard or non-standard clamps may be needed, which increases the processing cost. Therefore, in the design stage of prototype drawings, try to simplify the prototype design.
3. Order Larger Quantities
For the same prototype, the cost of one machining quantity is usually the cost of 10 or 100 machining quantity is much higher. In the process of machining, the same CAM programming and fixture are used, which is repeatable. Therefore, DDPROTOTYPE recommends using low volume production parts to reduce the cost per unit part.
4. Design skills
You can make changes in each of these areas, including material selection, programming, increased quantity or other manufacturing costs, to reduce CNC machining cost. When the above areas cannot be modified during prototyping, you can also take the following steps to ensure that the design is optimized to minimize the budget.
The inner angle of a circle
In the process of CNC machining, the rotating tool will automatically leave a circular internal angle at the internal angle. The larger the diameter is, the less material removal steps are required, and the shorter the machining time is. If there is a sharp, 90 degree internal angle in the design, it is necessary to stop the machine, rotate the parts, set the fixture, and use a special tool to continue machining. This process will greatly process the time and risk, increasing the additional cost. If you adjust the design to fillet without affecting the function of the prototype, the machine can run continuously to make parts, and further ensure that the radius of the inner corner is at least 1 / 3 of the cavity depth, which helps to eliminate the change of the tool and greatly shorten the processing time.

Avoid deep pits
For deep pit machining, it usually requires the use of fragile tools to increase the risk, and it takes a lot of time to remove more materials, and even requires the use of special tools to achieve the depth required by the design. In order to avoid risks, the rotation speed of the tool can only be reduced as much as possible when setting the tool path, and milling can be carried out in small increments. Or use other technology, such as WEDM, the cost is also relatively high. Try to limit the pit depth in the design to 2-3 times of CNC tool diameter. If it exceeds 4 times, the cost will increase exponentially.

Limited precision tolerance
In general, the function of a part requires only a few surfaces or surface supports. If there are more dimensions in the design (such as radius, angle, depth, etc.), the cost of the part will be higher.In the prototype design, we try to eliminate some non key annotations and assign key numbers to the features and surfaces that undertake the task. Smaller tolerance = higher cost. Ddprototype follows ISO 2768 medium standard, which is a reasonable standard for prototype design in DDPROTOTYPE. Our typical tolerance accuracy unit is 0.005 “– 0.001”, depending on the specifications required by customers.
Restricted parenchyma
Because the vibration of the tool is very easy to deform and the tolerance is difficult to maintain, the machining speed needs to be greatly reduced and the cost of CNC production increased. Ddprototype recommends a minimum wall thickness of 1.0mm for plastics and 0.5mm for metals. If very thin walls are required, sheet metal manufacturing is usually more economical.


Limit thread length
The length of the thread is about 1.5 times the diameter of the hole and the connection will not be stronger. Increasing the length of the threads may require special tools to make them. In the design of parts, the length of thread should be limited to three times of the hole diameter as far as possible, and the use of standard tap can greatly reduce the cost. Note that the thread in the blind hole should have an additional unthreaded half diameter at the end of the hole.
avoid multiple finishing
The surface treatment of parts will usually have a smoother surface, more pleasant and beautiful appearance, better corrosion resistance, and can maintain function in harsh environment. This requires a higher cost.If only when necessary, it can reduce the cost. DDPROTOTYPE has rich experience in anodizing aluminum and has unique views on cost reduction. Please contact us for details.


Decompose complex parts.
For parts with complex geometry, many coding settings may be required in the process of machining. Special clamps also need to be rotated and repositioned manually, which will also greatly increase the cost. If a large and complex part is decomposed into two or more parts in the design of the part, and then assembled together, the function of the part will not be affected.
About DDPROTOTYPE
DDPROTOTYPE is a one-stop solution supplier for your on-demand manufacturing. After applying every skill to reduce CNC machining cost to your design.DDPROTOTYPE is a reliable CNC machining partner. Attention to details, such as optimizing design, identifying materials, precise tolerance, timely delivery and so on, are trusted by customers, and we are willing to do our best to ensure that you are satisfied with CNC machining parts.
When you are ready to get the quotation, please submit 3D drawings to info@ddprototype.com.