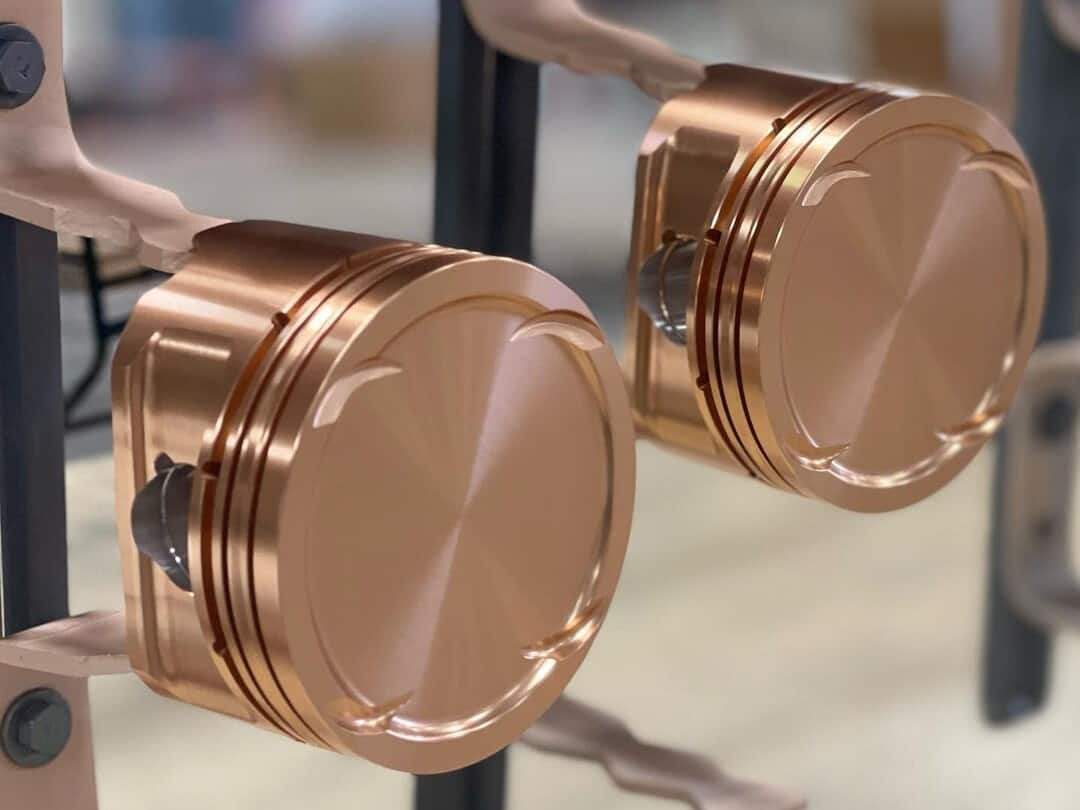
Rapid Prototyping & Rapid Manufacturing Expert
Specialize in CNC machining, 3D printing, urethane casting, rapid tooling, injection molding, metal casting, sheet metal and extrusion
Factors affecting the cost of anodizing aluminum parts
Aluminum alloy has become the second largest type of metal material next to steel due to its excellent physical and chemical properties such as low density, high strength excellent ductility, good electrical conductivity, strong corrosion resistance and easy forming. Especially, the use of CNC machining technology to manufacture aluminum prototype has received widespread attentions. There are many surface treatment for custom aluminum parts, such as anodizing, micro-arc oxidation, electroplating, painting (Powder coating or painting) etc., and the most widely used process is anodizing. Today let we discuss the knowledge of anodizing and the factors affecting the cost of anodizing aluminum parts.
What is anodizing and its effects
The anodizing process is to use metal or alloy parts as an anode, and use the method of electrolysis to form an oxide film on the surface. Metal oxide films change the surface state and properties, such as surface coloration, improve corrosion resistance, enhance wear resistance and hardness, and protect metal surfaces. The anodizing of aluminum and aluminum alloys, placed the aluminum and aluminum alloys as anode in the corresponding electrolyte (such as sulfuric acid, chromic acid, oxalic acid, etc.), and electrolysis is carried out under specific conditions and the action of an applied current. A thin layer of aluminum oxide is formed on the oxidized surface of the aluminum or aluminum alloys of the anode, and its thickness is 50-30 microns, and the hard anodized film can reach around 25-150 microns. The aluminum and aluminum alloys after anodizing process, the hardness and wear resistance improved, and there are a large number of micropores in the thin oxide film, which can absorb various lubricants and are suitable for the manufacturing of engine cylinders or other wear-resistant parts; Micropores in the thin oxide film with strong adsorption capacity can be colored into a variety of beautiful and gorgeous colors. Non-ferrous metals or its alloys (such as aluminum, magnesium and its alloys, etc.) can be anodized. This method is widely used in mechanical parts, aircraft and auto parts, precision instruments and radio equipment, daily necessities and architectural decoration.
Corrosion resistance. Since the film layer obtained by anodization has sufficient stability in the atmosphere, then the oxide film can be used as protective layer for aluminum parts to prevent corrosion. The oxide film of aluminum obtained by anodizing in chromic acid solution has good corrosion resistance and the micropores of the oxide film is fine; the oxide film obtained from sulfuric acid solution has larger micropores than the former, but its film layer is thicker and has strong adsorption capacity, after appropriate filling and sealing treatment, its corrosion resistance is also very good. It should be mentioned that the chromic acid anodizing method is especially suitable for the anodizing treatment of riveted parts and welded parts.

Decoration. Anodizing can absorb various organic dyes and inorganic dyes, thus giving aluminum parts a variety of bright colors. Under some special process conditions, a protective and decorative oxide film can be obtained and similar with porcelain appearance.
Wear resistance. Through the hard anodizing aluminum and aluminum alloys, a thick and hard oxide layer can be obtained on the surface. A hard and thick oxide film can be obtained on aluminum parts by anodizing in sulfuric or oxalic acid solutions also. For example, the engine cylinders and pistons of automobiles and tractors after anodizing, its wear resistance can be improved greatly.
Insulation. The oxide film of aluminum and aluminum alloys obtained by anodizing has large resistance, so it has certain effect on improving the electrical insulation of aluminum parts. Anodizing can be used to prepare the dielectric layer of capacitors, or oxidation Aluminum prepares an insulating layer for its surface.
As a primer for painting and electroplating. Due to the porosity and good adsorption capacity of the anodized film, it can be used as the bottom layer of spray paint and other organic films, so that the paint film and organic film can be firmly combined with the parts, thereby increasing its corrosion resistance. Before the aluminum and aluminum alloy parts are electroplated, a primer layer must be applied to them before electroplating. There are many methods for applying the bottom layer on the surface of the substrate. In addition to electrogalvanizing, zinc dipping, and electroless nickel plating, anodizing treatment is also one of the important methods.



Preparation process of anodized film
Common processes for aluminum alloys anodizing included: chromic acid anodizing process, sulfuric acid anodizing process, oxalic acid anodizing process and phosphoric acid anodizing process. When using different electrolytes, the obtained oxide films have great differences in appearance and properties. In actual manufacturing, it is necessary to select a suitable anodizing process according to the purpose of use.
Sulfuric acid anodizing process. At present, the most widely used anodizing process in the world is sulfuric acid anodizing. The sulfuric acid anodizing process is simple, short operation time, the production operation is easy to master, the film transparency is high, and the corrosion resistance and wear resistance are good. Compared with other acid anodizing, it has obvious advantages in various aspects. The process flow of sulfuric acid anodizing is: polishing → degreasing → two cleanings → chemical polishing or electrolytic polishing → two cleanings → anodizing → two cleanings → dyeing. If the aluminum parts use higher voltages and strong sulfuric acid for anodizing, which be called “hard” anodizing, and also be an ideal option for making heavily worn parts.

Chromic acid anodizing. The chromic acid anodizing process was first developed by Bengough and Staurt in 1923 (B-S method for short). The oxide film obtained by chromic acid anodizing is relatively thin, generally only 2-5μm thick, which can maintain the original precision and surface roughness of the parts, and is called “light” type anodizing. The oxide film is soft, and its wear resistance is not as good as sulfuric acid oxide film, but it has good elasticity. In addition, the film layer is opaque and has a low porosity, which is difficult to dye, and can be used directly without sealing. The low solubility of chromic acid solution on aluminum alloys makes the solution remaining in pinholes and crevices have little effect on the corrosion of components. It is used for surface treatment of castings, riveted parts and machining.

Oxalic acid anodizing. Oxalic acid anodizing process was widely used in Japan and Germany as early as 1938. Because the solubility of oxalic acid for aluminum and aluminum alloys is small, and the porosity of the oxide film is low, so the corrosion resistance, wear resistance and electrical insulation of the film are better than sulfuric acid film. However, the cost of oxalic acid anodic oxidation is high, generally 3-5 times of sulfuric acid anodic oxidation; and the color of oxalic acid oxide film is easy to change with the change of process conditions, resulting in color discrepancy of the product, so this process is limited in application, generally only It is used under special requirements, such as making electrical insulating layers.
Phosphoric acid anodizing. Phosphoric acid anodizing was first used as a pretreatment process for aluminum plating. Since the oxide film dissolves more in the phosphoric acid electrolyte than sulfuric acid, the phosphoric acid film is thin (about 3 μm in thickness) and has a large pore size. Because the phosphoric acid film has strong water resistance, it is mainly used for the surface treatment of printed metal plates and the pretreatment of aluminum workpiece bonding.
Anodizing gives aluminum and aluminum alloys better corrosion resistance, wear resistance, decorative properties and electrical insulation, and is the most widely used surface treatment technology for aluminum and aluminum alloys currently. With the development of science and technology, in order to follow the concept of environmental protection or to improve the performance of one aspect of the anodized film, or to reduce the production cost, the anodized film has gradually developed from a traditional acid anodized film to a mixed acid anodized film.
Factors affecting the cost of anodizing aluminum
The thickness of oxide film. The thickness of the oxide layer is a major factor the cost of anodizing aluminum parts. Standard thickness oxide films are the cheapest. Most people think that the thicker the oxide film, the higher the cost of anodizing. In fact, the thinner the oxide film, the higher its price. For example, +/- .001” is cheaper than +/- .0001”. This is because thicker oxide films are easier to control than thinner oxide films.
Type of anodizing process. Above we introduced 4 types of anodizing process, each type have a significant impact on the cost of anodized aluminum. Of the four types, the chromic acid anodizing process is the cheapest. This is because the materials to be used, such as chromic acid, are inexpensive and consume less energy. Anodizing with sulfuric acid, the price of producing hard anodizing aluminum will be higher.
Size of the part. Size of the part is an important factor in the cost of anodized aluminum parts. The larger the size and the larger the surface area of the part, which means the required materials and facilities need to increse. In addition, an increase in the size of parts means an increase in labor and time, as well as an increase in cost.



Anodizing is an electrolytic process and an ideal option for improving the performance of aluminum parts. In fact, anodizing aluminum parts is a simple process, and you can anodize aluminum at home if you have the necessary equipment, such as storage tanks, chemicals, and stable high-voltage electricity. However, in pursuit of higher quality and aesthetic appearance, it is best to consider a professional anodized aluminum supplier.