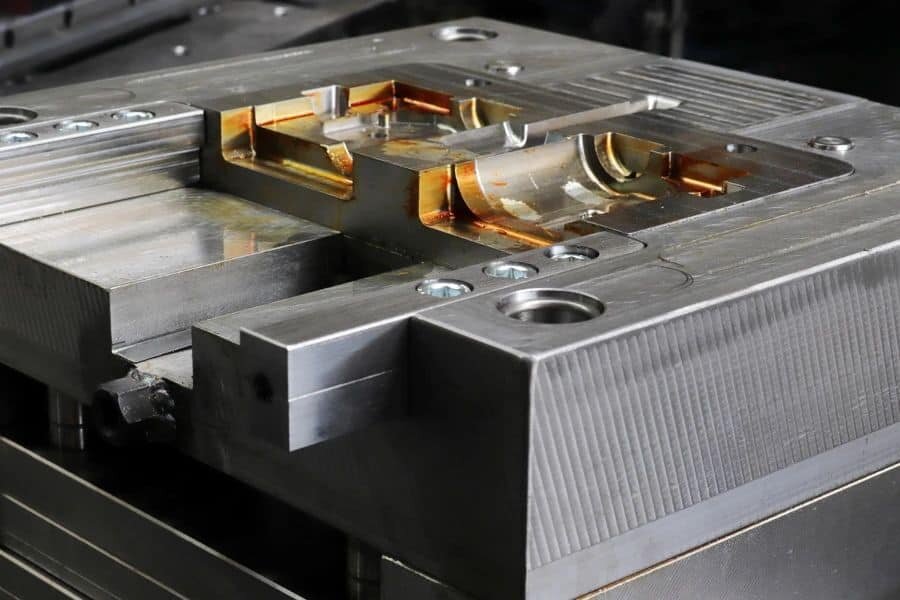
Rapid Prototyping & Rapid Manufacturing Expert
Specialize in CNC machining, 3D printing, urethane casting, rapid tooling, injection molding, metal casting, sheet metal and extrusion
The Difference Between Injection Molding vs Die Casting
Both injection molding VS die casting are ways of mass production/manufacturing. The two manufacturing techniques are similar in that molten material is injected into the mold by using extreme pressure, and then parts are demoulded after cooling. Many people have difficulty to distinguish the difference between the two methods. Now we discuss in detail the difference between injection molding and die casting, the advantages, disadvantages and how to choose the best manufacturing techniques.
Injection molding
Injection molding is a very popular manufacturing process. Main reason is compatible with a wide variety of materials, including metals, glass, but most commonly is plastics, especially thermoplastics, therefore, a wide variety of products can be produced. Injection molding can be divided into plastic injection molding and Metal Injection Molding.

Plastic Injection Molding (PIM)
Install the tooling on an injection molding machine, and the liquefied molten plastic is injected into the mold using high pressure until all the cavities are filled. After it is cooled, the part can be removed from the machine. The process is plastic injection molding.
Advantages of injection molding
Ability to manufacture parts with complex geometric features
Rapid manufacturing
Can be used repeatedly
Very little material waste
Low cost per part
Achieve tight tolerances
Compatible with a variety of plastic materials, custom selection of soft, tough or high-strength parts
Excellent surface finish
Disadvantages of injection molding
The cost of molds is high.
The cost of raw materials mightbe expensive
Due to the size limitation of injection molding machines and molds, it is especially suitable for making small parts. For large parts, several parts may be required and then assembled, which takes time and more cost
For complex parts, longer lead times may be required
It is very difficult to modify the finished mold, especially the steel mold.Several adjustments and tests are required before a part manufactured.
Common plastic injection molding materials
Plastic injection molding can be compatible with thermosetting plastics and thermoplastics. The more common materials are:
Nylon
Polycarbonate
Acrylic fiber
Polystyrene
Polyoxymethylene (POM)
Polypropylene (PP)
Acrylonitrile Butadiene Styrene (ABS)
Thermoplastic Polyurethane (TPU)
Polyethylene (PE)
Thermoplastic Rubber (TPR)
Celcon® (Acetal)
High impact polystyrene (HIPS)
Low Density Polyethylene (LDPE)
Metal Injection Molding (MIM)
Powder metal and binder (wax, thermoplastic polymer or other binder) are mixed together, and the resulting mixture is used as the “raw material” for metal injection molding. The mixture is injected into the mold by using high pressure, and after cooling and solidification, it forms metal parts. In addition, additional cleaning and degreasing are required, after heat treatment, and completely removed the binder, the final metal part is obtained.

Advantages of Metal Injection Molding
Metal injection molding can produce parts with high strength and wear resistance
Manufacture of complex and thin-walled (eg 0.1mm) metal parts
Used repeatedly
The final product does not require additional finishing
Minimal waste of materials
Disadvantages of Metal Injection Molding
Higher cost to manufacture large size parts (eg over 100 grams)
Mechanical operation that requires professional skills
During the degreasing or sintering stage, the part has a certain shrinkage rate
The mold life is relatively small (150K-300K times)
Common materials for metal injection molding are: stainless steel, titanium, nickel, tungsten, copper and various other combinations, etc.
Die casting
The manufacturing process of die casting is similar to injection molding, the material of choice is a molten metal, not a plastic, nor a mixture of powdered metals.
Advantages of die casting
Full automationline
Low cost
Better mechanical propertiesof parts
Disadvantages
Finished products usually have porosity
The quality of the parts is relatively poor
High cost of mold
Common materials for die casting: aluminum, zinc, copper, magnesium, lead, other metals and other alloys.
Here, we can see that plastic injection molding is a way of making plastic parts. Metal injection molding and die casting are techniques for making metal parts. If you plan to manufacture plastic parts, then go with plastic injection molding. If you plan to manufacture metal parts, it is more informative to compare metal injection molding with die casting.

Metal Injection Molding VS Die casting
Although both processes can produce high-quality parts, there is a big difference between the two, let’s compare them one by one.
Thin-walled parts
Metal injection molding can manufacture thin-walled parts according to strict parameters, while die casting cannot control the wall thickness and porosity of the part. Therefore, die casting is not ideal for making thin-walled parts.
Porosity
After heat treatment, the parts manufactured by metal injection molding have higher row tensile strength and have a uniform and dense structure. The internal structure of parts made by die casting will have certain air cavities, which are usually referred to as porosity.
Mold life
Despite it need to withstand high pressure and molten high temperature metal, die casting molds have one million shots, while metal injection molding molds can be reused around 150k-300k.
Product shrinkage
Typically, metal injection molded parts will shrink by as much as 30% after heat treatment, so shrinkage must be accurately calculated. Die casting parts do not have the problem of product shrinkage.
Cost
Although metal injection molding can produce higher strength parts than die casting and can avoid wasting material, while the metal injection molding is 20%-30% more expensive than die casting. This cost difference mainly depends on the type of material chosen. In addition, die casting can be achieved automatic line to reduce labor costs.
Automation and Product Design
Metal injection molding can manufacture parts with complex structures. This is more difficult for die casting.
Material waste
Metal injection molding with little or no material waste, and the material injects into the mold according to the established parameters. The parts made by die-casting need to remove the excess parts, and there is a certain amount of waste.
Which process to choose to manufacture metal parts
It seems like metal injection molding looks more advantageous than die casting, but it can’t be judged that way. It should come up with the reality. Which process to choose to manufacture metal parts depends on your industry goals. If you want to manufacture large parts, such as engine casings, large containers, etc., die casting may be the ideal choice. Because the process is not too complicated and the cost of raw materials is relatively low.
If you plan to manufacture complex and small metal parts, metal injection molding is an ideal manufacturing process that saves time and resources. Die casting cannot make highly complex metal parts.
Conclusion
Metal injection molding is a new technology. It is more cost-effective for mass production of parts with small, complex features is required.
Die casting is more profitable when manufacturing a large number of larger, simple-structured parts.
If you still can’t judge to choose the most suitable manufacturing process, please feel free to contact DDPROTOTYPE immediately, which is a top manufacturer in China, they will strictly review and optimize your design drawings and propose the most feasible solution.