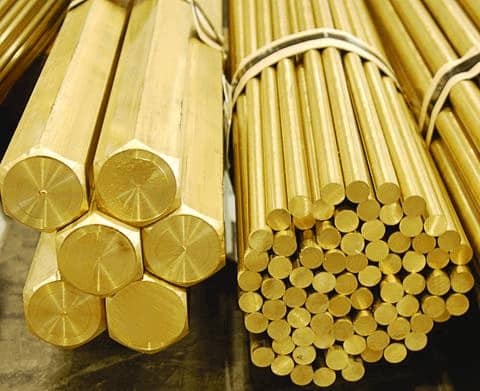
Rapid Prototyping & Rapid Manufacturing Expert
Specialize in CNC machining, 3D printing, urethane casting, rapid tooling, injection molding, metal casting, sheet metal and extrusion
Bronze vs Brass, Which is Better for Your CNC Machining Project
CNC milling and turning are compatible with hundreds of metal alloys. Which material is best for your CNC machining project? It depends on many factors, including price, machinability, corrosion resistance, strength, weight, and appearance. Material selection is a very important part of any manufacturing process, especially materials with similar alloying elements, such as bronze and brass, which are both copper alloys. Next, we’ll introduce the difference between bronze vs brass and explain which is better for your CNC machining projects.
Bronze Vs Brass:History
Bronze. About 3,500 years ago, the ancient Sumerians ushered in the Bronze Age. Bronze is mainly composed of copper and tin, sometimes with small additions of other elements such as phosphorus, manganese, aluminum or silicon, and has a melting point of 315 – 1080 °C. Due to the high copper content of bronze, it has a distinctive reddish appearance. Bronze has good hardness, electrical conductivity, thermal conductivity, low friction coefficient, and it can be used to manufacture weapons, armor, tools, bearing springs, and even ship parts, etc., because of its certain corrosion resistance in seawater. Although brass is considered to make musical instruments.

Brass. Brass was discovered in 500 BC, mainly composed of copper and zinc, sometimes with other small additions, such as tin, iron, aluminum, lead, silicon and manganese, etc., and its melting point is 809 – 1030 °C. Other trace elements can improve the properties of brass, such as manganese, which can improve the corrosion resistance of brass, and the higher the zinc content, the easier it is to stretch and bend. The color of brass is closer to gold, and it is widely used in decorations in the field of construction. Its excellent corrosion resistance is also commonly used in the manufacture of pipes and so on.

17 Differences Between Bronze vs Brass
Elemental composition of bronze | |||||
copper | tin | aluminum | lead | antimony | chromium |
Nickel | Phosphorus | silicon | sulfur | Cobalt | zinc |
Elemental composition of brass | |||||
copper | zinc | tin | sulfur | silicon | Phosphorus |
Nickel | lead | iron | antimony | aluminum |
Bronze Vs Brass:Corrosion resistance. Due to the presence of copper, bronze will oxidize in air, producing a mottled patina, which helps prevent further corrosion. Bronze has excellent corrosion resistance in salt water and is commonly used in marine applications such as marine propellers, rudders, underwater bearings, portholes, center plates and engine parts. On the other hand, brass also has excellent corrosion resistance and is better than bronze.

Bronze Vs Brass:Electrical Conductivity. Copper has excellent electrical conductivity andit is often used as a standard for conducting electricity. However, there are many other small amounts of elements in bronze and brass, such as aluminum, tin, zinc, nickel, cobalt, which can greatly reduce the electrical conductivity. After testing, compared with copper, the conductivity of bronze is only about 15% of copper, while the conductivity of brass is about 30% of copper.

Bronze Vs Brass:Thermal conductivity. The higher the thermal conductivity of the material, the better for thermal applications. It has been proved by practice that the thermal conductivity of brass is much greater than brass’s. Although bronze can be used for thermal applications, brass is more suitable for making heatsink

Bronze Vs Brass:Melting point. Bronze has a melting point (315 – 1080 °C), and brass is (809 – 1030 °C), both are easy to cast. Melting point is very important and critical for CNC machining projects. Because the temperature reaches near the melting point, the state of the CNC part is possibly to change from solid to liquid, which will affect the function of the part and even malfunction.

Bronze Vs Brass:Hardness. Hardness is a measure of how it behaves under stress and responds to dents and scratches. According to the value of Brinell hardness, the Brinell hardness of brass is around 55-73, while bronze is around 40-420.Therefore, bronze is harder than brass, but also more fragile and more prone to breakage.

Bronze Vs Brass:Durability. Bronze is a hard metal that does not bend easily and can withstand water erosion. Brass is also a strong and durable metal, but not as durable as bronze.

Bronze Vs Brass:Machinability. Machinability refers to the reaction of a metal to machining stresses such as stamping, CNC milling, CNC turning, etc. Most copper alloys are highly ductile, which presents processing challenges. But there is the brass material C360 specially developed for CNC machining.

Bronze Vs Brass:Yield strength. The highest stress to which a metal is permanently deformed. Brass has a yield strength of 34.5 to 683 MPa (5000 – 99100 psi), while bronze is 0 – 800 MPa (10000 – 116000 psi). Therefore, bronze has a higher yield strength than brass and is less prone to permanent deformation.

Bronze Vs Brass:Tensile strength. Brass and bronze have excellent tensile strength.And after tested. The brass has a tensile strength of 53 Ksi when annealed, and 88 Ksi (607 MPa) when cold-rolled and tempered. The bronze has a tensile strength of 50 Ksi (350 MPa) when annealed, and 92 Ksi (635 MPa) when cold rolled and tempered. The difference between the two is very

Bronze Vs Brass:Price. The copper content is the biggest factor in the price difference between the twomaterial, because bronze has more copper than brass, so it is more expensive. There is also a more complex process for making bronze, which is also one of the factors that affect the price.

Bronze Vs Brass:Alloy Comparison Table
Alloy Types | Min. Yield Strength, psi | Hardness (Rockwell) | Machinability | Formability | Electrical Conductivity | Weldability |
Copper | ||||||
Multipurpose 110 | 33,000 | F40 |
| Excellent | Excellent |
|
Super-Conductive 101 and 102 | 10,000 | F60 |
| Excellent | Excellent | Good |
Easy-to-Machine 145 | 18,000 | ___ | Excellent | Good | Excellent |
|
High Strength 182 | 40,000 | B60 |
| Excellent | Good |
|
Weldable 122 | ___ | ___ |
| Excellent | Good | Good |
Brass | ||||||
Ultra-Machinable 360 | 15,000 | B35 | Excellent |
|
|
|
Formable Easy-to-Machine 353 | 25,000 | B60 | Excellent | Good |
|
|
Easy-to-Machine Architectural 385 | 16,000 | B42 | Excellent |
|
|
|
Ultra-Formable 260 |
|
|
| Excellent |
| Good |
High-Strength 330 | 60,000 |
| B73 | Good | Excellent |
|
Weldable Marine-Grade 464 | 20,000 | B55 |
| Good |
| Good |
Marine-Grade 485 | 25,000 | B60 | Good |
|
|
|
Bearing Bronze | ||||||
932 Bearing Bronze | 18,000 | B34 | Good |
|
|
|
Easy-to-Machine 936 | 21,000 | B26 | Good |
|
|
|
Weldable 954 | 28,800 | B80 | Good |
|
| Good |
Ultra-Wear-Resistant AMPCO 18 | 37,000 | B88 | Good |
|
| Good |
High-Strength 863 | 62,000 | B97 |
|
|
|
|
High-Strength Formable 544 | 50,000 | ___ | Good | Good |
|
|
Self-Lubricating Oil-Filled 840 and 841 | 11,000 | ___ | Good |
|
|
|
High-Temperature Graphite-Filled 841 | 8,500 | ___ | Good |
|
|
|
Bronze | ||||||
High-Strength 630 | 50,000 | B90 |
|
|
| Good |
Easy-to-Machine High-Strength 642 | 42,000 | B65 | Good |
|
|
|
Easy-to-Weld 655 | 43,000 | B75 |
| Excellent |
| Excellent |
Easy-to-Machine 316 | 28,000 | B70 | Good | Good |
|
|
Easy-to-Form 220 | 33,000 | B55 |
| Excellent |
| Good |
Ultra-Strength Easy-to-Form 510 | 80,000 | ___ |
| Excellent |
| Good |
Common Brass Grades
There are many grades of brass, each with exact alloy composition and properties. Here,DDPROTOTYPE lists 7 common grades for your reference.



Brass 260. Brass 260 has good cold working properties. Suitable for guns, cars, fasteners, etc.
Brass 272.Brass 272 contains 33% zinc and is commonly used in industry and construction.
Brass 330. Brass 330 has excellent machinability and is often used to make pipes due to its cold workability and low lead content.
Brass 353. Brass 353 has excellent machinability and is often used to manufacture precision parts, such as watch parts.
Brass 360. Brass 360 is the most popular type of brass, offering excellent machinability and formability, as well as being suitable for welding and brazing, it is ideal for making hardware components, fittings, valves and fasteners, and more.
Brass 385. Brass 385 is available in a variety of extruded and extruded shapes and is often used in construction such as angles, channels, square tubes, handrail forming, and more.
Brass 464. Brass 464 has excellent resistance to seawater erosion, and also has good thermoformability, bending, brazing, welding, etc., and is often used in marine applications.
Common Bronze Grades
Tin bronze. The tin content of this alloy is usually between 0.5% ~0%, and the phosphorus content is between 0.01% ~0.35%. Tin bronze is known for its toughness, strength, low coefficient of friction, high fatigue resistance and fine grain. 907 tin bronze has excellent corrosion resistance in seawater, and is resistant to wear and fatigue. Manufactured parts are: bearings, bushings, marine accessories, piston rings, pump components, etc. 917 tin bronze is famous for its bearing capacity, strong corrosion resistance and lubricity, and is often used in the manufacture of low-speed and high-load bearings, gears, and worm gear components.

Aluminium bronze. Aluminium Bronze contain 6% ~12% aluminium, 6% iron maximum, and 6% nickel maximum. These alloying elements increase the strength of aluminum bronze and provide excellent corrosion and wear resistance. 954 Aluminium Bronze is the most popular aluminium bronze alloy, and it is a very strong metal with excellent corrosion resistance, strength, high ductility, high yield and tensile strength, can be weld Commonly used in the manufacture of worms and worm gears , gears, bushings, bearings, valve components, etc. 955 Aluminum Bronze is one of the toughest metals, with excellent heat resistance, tensile strength, yield strength, high hardness and machinability , especially in seawater, it has excellent corrosion resistance, can be welded, commonly used in manufacture of agitators, aircraft engines (seats, valve guides), gears, bushings, landing gear components, etc.

Silicon bronze. Silicon bronze has high strength and corrosion resistance and it is often used in valve stems. Very similar to red bronze, but with a lower zinc content, it is often used to make pump and valve parts, etc.

Copper nickel. Copper nickel contains 2% ~30% nickel , and it has very high corrosion resistance and thermal stability. This material is also very resistant to corrosion cracking under stress and oxidation in steam or humid air environments. Higher nickel content will improve corrosion resistance in seawater and resistance to marine biofouling. It is often used to manufacture electronics, marine equipment, valves, pumps and boat hulls, among others.

Manganese bronze. Manganese bronze has excellent corrosion resistance and high strength, and the manufactured parts are very durable.And it is ideal for the manufacture of load-bearing parts, such as gears, cams, hydraulic cylinder assemblies, load-bearing bearings, nuts, etc.
Bronze Vs Brass, Which is Better for Your CNC Machining Project?
Bronze and brass retain many copper’s qualities, but they also have unique differences. Bronze is often confused with brass when selecting materials for CNC machining projects. After we compare the two types thoroughly, you should have the answer. If you still can’t make the final decision, please contact DDPROTOTYPE, we will fully evaluate your CNC machining project and help you make the right choice.