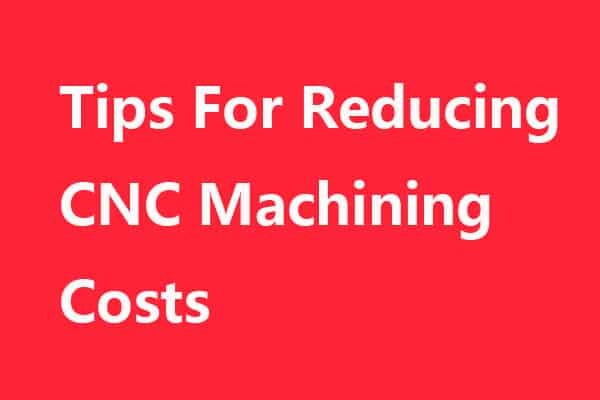
Rapid Prototyping & Rapid Manufacturing Expert
Specialize in CNC machining, 3D printing, urethane casting, rapid tooling, injection molding, metal casting, sheet metal and extrusion
Tips for reducing CNC machining costs
Making unique and innovative prototypes that look great and function well is what we strive for. When designing or machining, we pay a lot of attention to the end use of the part, such as “aerospace parts require lightweight parts, automotive tail lights require high surface finish, etc.”. But the desire to reduce costs runs through the entire design and manufacturing process.
Before understanding the techniques for reducing CNC machining costs, we must understand the price factors of CNC custom parts firstly. The most important factor is the processing time, which even exceeds the depreciation cost of the machine and the programming cost. The trick to reducing CNC machining costs is to follow certain rules to optimize the design, thereby reducing machining time without compromising the mechanical functionality of the part. DDPROTOTYPE has rounded up over ten tips to hopefully cut costs for your next CNC project.

1.Explore cheap materials-Reducing CNC Machining Costs
Both the price of raw materials and the ease of processing have a significant impact on costs. The price of raw materials is determined by their rarity and their own value. DDPROTOTYPE made a price comparison of different materials but with same size which are commonly used, and found the price difference is quite large. The ease of processing of a material has a greater impact on processing costs than the price of raw materials. In general, cutting softer materials requires less machining time and does not require special knives or additional auxiliary tools. For example, for the parts of the same drawing, the processing price of aluminum 6061 is much lower than that of stainless steel.
Take the 6” x 6” X 1” size as an example, the cost of different materials varies
Metal | |
Aluminum 6061 | $25 |
Aluminum 7075 | $80 |
Stainless Steel 304 | $90 |
Brass C360 | $148 |
Plastic | |
ABS (Acrylonitrile Butadiene Styrene) | $17 |
POM (Polyoxymethylene) | $27 |
Nylon 6 | $30 |
PEEK | $300 |
In general, just as a functional prototype, choosing a relatively cheap soft material that meets the design requirements would be more cost effective . Aluminum 6061 is clearly the most cost-effective material for making metal prototypes because of its low cost and very good machinability. Stainless steel and titanium are very expensive options, and it can save money unless certain specified material properties are required. If you are designing a medical device and it needs to be implanted inside the human body, then biocompatibility must be the first priority, and you have to choose titanium alloys, or stainless steels and so on based on actual requirements. When it comes to plastics, ABS and POM are the more popular inexpensive materials and are relatively easy to process,PEEK is a very expensive material.

2.Balance quantity and turnaround time - -Reducing CNC Machining Costs
Larger quantity is another important factor in reducing CNC machining costs.With quantity increasing, the unit price decreases. In the image below, the cost to machine just one piece is $41.89, and if 10 pieces are produced, the unit cost drops to $11.26. Increasing the quantity to 100pieces brings the unit price down to $5.72. The reason that the price has dropped so much is because only one piece is processed, which also requires programming, machine adjustment, material ordering, etc., while processing larger quantities, these tasks only need to be done once; more importantly, when the quantity increases, we will increase some Auxiliary jig to improve production efficiency, thereby greatly reducing the unit price of the product.

3. Evaluate the need for surface treatment - -Reducing CNC Machining Costs
Another factor that seriously affects the cost is the finish. When different surface treatments are required on the surface of a part, for example, a super high polish finish is required on one side and a special coating is required on the other side, or the surface finish effect of the entire part should be kept as consistent as possible, then additional costs will be incurred at this time. It is necessary to carefully evaluate the necessity of the surface treatment of the part, such as anodizing, heat treatment, special coatings, etc.

4. Set tight tolerances when necessary--Reducing CNC Machining Costs
Usually, not all features of a part are critical to its function. In the design, The more dimensions with tolerance requirements, the higher the precision requirements, (for example, marking the radius, hole diameter and position, fillet), etc., will increase the cost of machining. To avoid adding unnecessary costs, only a few critical surfaces need to be toleranced, such as holes, shafts, snaps, etc., and tight tolerances are controlled (standard tolerance is +/- 0.005 inches). At DDPROTOTYPE, our typical tolerance accuracy range is 0.005″ – 0.001″, depending on structure, material, etc.

5. Try to avoid text or icons.
If not necessary, try to avoid building text or icons on the part during CNC machining, which will increase the cost. If text and icons are necessary, consider changing it to a surface treatment process such as painting or printing, as this can reduce CNC machining time..

6. Use as many standard-sized tool as possible
When designing parts, try to design the dimensions that match standard CNC tools, which can greatly save machining time. For example, hole, thread and pocket diameters should be machined directly with common CNC tools. Non-standard size holes require end mills or reamers for precision machining, and even some structures require custom tools. If you are unfamiliar with tool dimensions, a general practice is to set the hole to a “standard” inch, such as 1/8″, 1/4″, or a integer of millimeters. Avoid sizes like 0.3871″ or 3.956mm. In addition, maintaining consistent hole and cavity dimensions of the whole part can reduce tool changes frequency and thus speed up the CNC machining process.

7. Use standard tapping size
The design of standard tapped holes can reduce the cost of CNC machining. Tap size and thread depth affect the processing time. For example, if you design a 2-56 inch threaded hole, if the thread is too deep while the tap is relatively thin, it will be more troublesome to operate. It is a common practice to always design the maximum depth of the thread to be less than three times the diameter of the bore. Longer threads may require special tools, also greatly increase the tapping time, and there is a risk of tap breakage. If the tap broken,then we need to deal with it with EDM or remake the parts.

8. avoid large and complex geometry parts - -Reducing CNC Machining Costs
The characteristics of a part, including size and complexity, have a large impact on CNC machining costs. It goes without saying that larger parts will consume more material and machining time. For highly complex parts, multiple processes may be required during the machining process, perhaps proceeding on multiple machines, which requires more programming, fixtures and set-up costs. For example, a part in the figure below needs to be processed on multiple surfaces during the manufacturing process. In 2019 DDPROTOTYPE quoted $159 for this part.

9. Avoid designing thin walls
Although CNC machining can machining parts with tight tolerances and thin walls even less than 1mm, if you are on a tight budget, it is recommended to increase the wall thickness. Parts with too thin walls (usually defined as less than 0.794 mm (1/32 inch)) are easy to deform during CNC machining and can also cause tool vibration, making it difficult to maintain tolerances. The correct way to machine thin walls is to reduce the amount of feed, which takes long machining time. Therefore, designing thicker walls can help speed up processing times and reduce costs. DDPROTOTYPE recommends a minimum wall thickness of 0.8 mm for metal parts and 1.5 mm for plastic parts. If you are making parts with smaller wall thicknesses, you can try sheet metal fabrication.

10. Avoid sharp interior edges
Machining a perfect 90° interior angle is difficult because CNC-machined tools such as end mills or milling cutters are cylindrical and may automatically leave rounded interior corners during machining. If you stick to this design, the best way to achieve it is to use EDM machining, which is a more expensive machining process and will take longer to machine. If sharp interior corners are not necessary, a conventional design is that the radius of the interior corner is at least 1/3 the depth of the cavity. Smaller inside corner radii require smaller tools, but small tools cannot remove large amounts of material at one time, and feeds are extremely small to prevent tool breakage, increasing machining time. Also, if possible, try to keep interior corners of the same radius. This helps reduce tool changes frequency.

11. Avoid deep cavities
CNC machining parts with deep cavities is time-consuming and expensive because the tool is prone to breakage during the process of making deep cavities. The cutting length of CNC tools is limited and works smoothly when cutting cavities two to three times as deep as their diameter. For example, a cutter with a diameter of 15 mm can easily cut a cavity up to a depth of 30 mm. DDPROTOTYPE recommends that the length of the cavity should not exceed 4 times the diameter of its tool based on practice. Otherwise, special tools or 5-axis CNC machines are required. For deeper cavities, additional machining equipment such as EDM, broaching, etc. may be required to assist in processing , which increases the machining cost.

12.Avoid designing features with high aspect ratios
When CNC machining high aspect ratio parts, tool vibration is prone to occur and it is difficult to maintain tight tolerances. According to the experiences of DDPROTOTYPE, the aspect ratio should be less than 4, which can effectively reduce the cost of CNC machining.

13. Split the complex parts
In certain cases, if a complex part is splitted into several parts and then bolted or welded together, the mechanical function of the assembly can also be fulfilled,we will recommand. This will reduce costs compared to machining a large, super-complex part individually.
Especially for parts with deep cavities or parts that need to be machined on multiple sides, machining them can be time-consuming and may require custom fixtures or 5-axis CNC machines.

14. Make sure the design is accurate
Unfinished or inaccurate CAD drawings will lead to secondary processing of parts, or even scrapping, and need to remake. This adds extra processing time, which is very frustrating. Consulting an experienced machinist or manufacturer during the design phase can save you a lot of time and money in the long run.

Summarize. Best Practices for Reducing CNC Costs
All in all, keep your parts simple and avoid complexity.
Otherwise, special tools or fixtures, multiple machine set-ups are required, especially for parts with highly complex geometries in special materials, meaning longer machining times.
So, in order to reduce the cost of CNC machining, after the design is complete, ask yourself the following questions:
Has the design been optimized with process feasibility guidelines?
Are all features of the design absolutely necessary?
Can the design function be simplified?
Can it be split into multiple parts that are easier to machining and then assembled?
Is the design re-optimized to eliminate the need for multiple machines to assist machining or special tooling to meet requirements?
Are there cheaper or easier-to-process materials that can meet my requirements?



In this article, we highlight design techniques with universal application to reduce the cost of CNC machining. Of course, for different projects and different solutions, you can send your 3D files to DDPROTOTYPE, optimize your designs for free, and provide constructive suggestions.