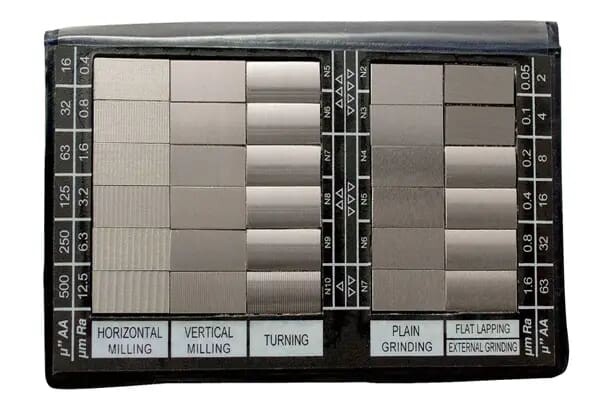
Rapid Prototyping & Rapid Manufacturing Expert
Specialize in CNC machining, 3D printing, urethane casting, rapid tooling, injection molding, metal casting, sheet metal and extrusion
The surface roughness of CNC machined parts
CNC machining can manufacture the part with tight tolerance requirements and fine parts of various metals or plastics, and is one of the best machining methods for custom parts and prototype production. During CNC machining, raw material is selectively and precisely removed to produce the part that approximate the final shape. This machining process is also commonly referred to as subtractive manufacturing. As the CNC cutting tool continuously removes raw material during machining, visible cutting tool marks will be created on the surface of the part. For the definition of finish of these cutting tool marks, we call it the surface roughness of CNC machined parts and divide it into various roughness grades.
What is surface roughness and what caused it
The surface of the parts after CNC machined, it looks very smooth but it feels uneven when touched by hand. In daily life, people are often used to calling it “surface finish”. In fact, the international unified standard calls it “surface roughness”. Surface roughness refers to the small spacing and the unevenness of small peaks and valleys that the machined surface has. The distance (wave distance) between the two wave crests or two wave troughs is very small (below 1mm), which belongs to the microscopic geometric shape recognition error. And the value of surface roughness is smaller, the smoother of the surface.

Surface roughness is generally formed by the processing method used and other factors, such as the friction between the tool and the surface of the part during machining, the plastic deformation of the surface metal when the chips are separated, and the high-frequency vibration in machining process. Due to different processing methods and workpiece materials, the depth, density, shape and texture of the cutting tool marks left on the machined surface are different.
The effects of surface roughness on parts
Surface roughness is closely related to the matching properties, wears resistance, fatigue strength, contact stiffness, vibration and noise of mechanical parts, and has an important impact on the service life and reliability of mechanical products. The part after CNC machining, and the surface of the part will leave fine machining marks, and the smaller the surface roughness, the smoother the surface. The specific influence of surface roughness on parts can be referred to the following points.

1、Surface roughness affects the wear resistance of the parts. The rougher the surface, the smaller the effective contact area between the mating surfaces, the greater the pressure, and the faster the wear.
2、Surface roughness affects the stability of the fit properties. For clearance fit, the rougher the surface is, the easier it is to wear, so that the clearance gradually increases during the working process; for interference fit, due to the flattening of microscopic peaks during assembly, the actual effective interference is reduced, the connection strength is reduced.
3、Surface roughness affects the fatigue strength of the part. There are large wave valleys on the surface of rough parts, which are sensitive to stress concentration like sharp corner notches and cracks, thus affecting the fatigue strength of the parts.
4、Surface roughness affects the corrosion resistance of the part. The rough surface is easy for corrosive gas or liquid to penetrate into the inner metal layer through the tiny valleys on the surface, causing surface corrosion.
5、Surface roughness affects the sealing performance of the part. Rough surfaces cannot be tightly fitted, and gas or liquid leaks through the gaps between the contact surfaces.
6、Surface roughness affects the contact stiffness of a part. Contact stiffness is the ability of the joint surface of a part to resist contact deformation under the action of external force. The stiffness of the machine is largely determined by the contact stiffness between the various parts.
7、Surface roughness affects the measurement accuracy of the parts. The surface roughness of the measured surface of the part and the measuring surface of the measuring tool will directly affect the accuracy of the measurement, especially during precise measurement.
In addition, the surface roughness will have varying degrees of influence on the coating, thermal conductivity and contact resistance of parts, reflectivity and radiation performance, resistance to liquid and gas flow, and current flow on the conductor surface.

Grade standard and selection of surface roughness
The surface roughness of CNC machined parts is not an accidental value, because the surface roughness is controllable and only needs to be preset before machining. But usually, many parts do not have specified surface roughness requirements, unless they are in some specific industries, such as some rotating parts, vibration scenes, medical implants and so on.
Different application fields require different surface roughness. How to choose a surface roughness value for your part, the first thing we need to consider is that the surface of the part must not only meet the functional requirements, but also consider the economic rationality. The specific selection can be determined by analogy with reference to the existing similar parts drawings. On the premise of meeting the functional requirements of the part, a larger surface roughness parameter value should be selected as much as possible to reduce the CNC machining cost. Generally speaking, the working surface, mating surface, sealing surface, friction surface with high movement speed and high unit pressure of the parts have high requirements on the smoothness and smoothness of the surface, and the parameter value should be smaller. For non-working surfaces, non-matching surfaces, and surfaces with low dimensional accuracy, the parameter values can be larger to reduce machining costs.

According to the ISO2632/1-1975 machining roughness standard, at DDPROTOTYPE CNC machining shop, we manufacture high-quality parts for customers according to the following four surface roughness parameter values.
Ra=3.2 um. this is the default surface finish for CNC machined parts and is suitable for most parts. The surface of the part with Ra3.2um is very smooth, but the cutting marks can still be seen, which is suitable for the scene under vibration, load and high stress.
Ra=1.6 um. this grade is a relatively good surface roughness, machined under the set conditions, but slight cutting marks can still be seen. Parts in this grade can mate closely with other components and are suitable for slow-moving and light-loaded scenarios, not for rapid rotation or severe vibration. Taking aluminum 6061 as an example, the cost of manufacturing Ra1.6um is about 5% higher than that of Ra3.2, and it increases with the complexity of the parts.
Ra=0.8 um. this is a high level of surface roughness that needs to be manufactured under tightly controlled conditions and is easier to produce with cylindrical, centerless or surface grinders. Parts in this class are typically used in scenarios with light loads or infrequent motion. Taking aluminum 6061 as an example, the cost of manufacturing Ra0.8um is about 10% higher than that of Ra3.2, and it increases with the complexity of the parts.
Ra=0.4 um. this grade is the highest quality surface finish. Parts of this grade usually require diamond polishing or grinding. For very smooth scenes, it is necessary to choose Ra0.4um, such as the inner wall of bearings or medical implants. Taking aluminum 6061 as an example, the cost of manufacturing Ra0.4um is about 15% higher than that of Ra3.2, and it increases with the complexity of the parts.

Common issues for surface roughness
Evaluation and measurement of surface roughness. The evaluation of roughness is mainly divided into qualitative and quantitative evaluation methods. The qualitative evaluation is to compare the surface to be measured with the known surface roughness comparison samples, and to judge its grade by visual inspection or by means of a microscope; Quantitative evaluation is to measure the main parameters of the roughness of the measured surface through some measurement methods and corresponding instruments. These parameters are Ra, Rq, Rz, Ry. At present, the commonly used surface roughness measurement methods mainly include sample comparison method, light section method, interference method, stylus method and so on.
The meaning of surface roughness parameters Ra, Rq, Rz, Ry. Ra is the arithmetic mean deviation of the contour: the arithmetic mean of the sum of the absolute values of the measured contour deviation within the sampling length. Rq is the root mean square deviation of the contour: the root mean square value of the contour offset within the sampling length. Rz is the 10-point height of micro-roughness: the sum of the average of the 5 largest profile peak heights and the 5 largest profile valley depths within the sampling length. Ry is the maximum height of the profile: the maximum distance between the peak line of the profile and the midline of the profile valley within the sampling length.
Factors affecting surface roughness. There are many factors that affect the surface roughness of the parts, among which the biggest factors are cutting speed, cutting depth, cutting amount, tool geometry angle, cutting tool vibration, hardness of processed material, workpiece rigidity, fixture and rigidity of machine tool during CNC machining, and use of cutting fluid, etc.