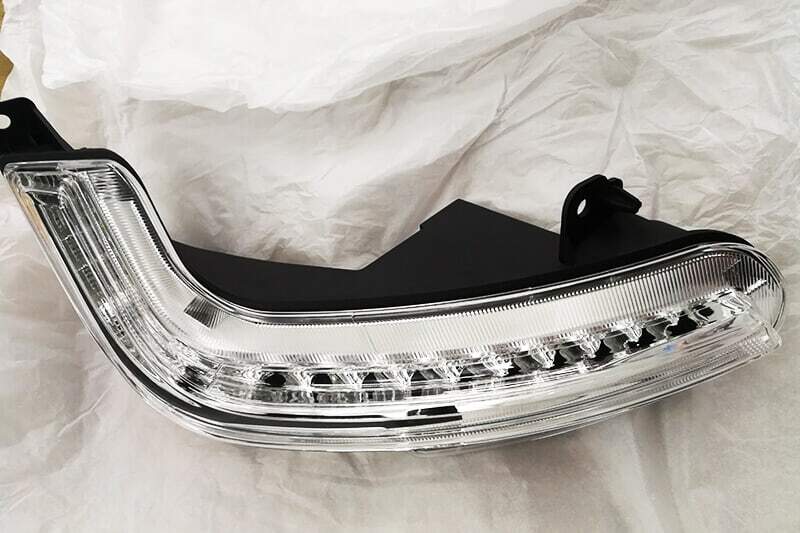
Rapid Prototyping & Rapid Manufacturing Expert
Specialize in CNC machining, 3D printing, urethane casting, rapid tooling, injection molding, metal casting, sheet metal and extrusion
Solution to Realize The Manufacturing of Prototyping-of-Optical-Parts-For-Cars
It is a challenging work to manufacture the prototyping-of-optical-parts-for-cars for the most Rapid prototyping company, The hardest part is how to make the optical parts clear. Cars bring great convenience to people and iterated out many brands and models every years. Especially the popular electric vehicles, such as Tesla, has become well-known automobile brand in recent years. In order to enhance competitiveness, the time for vehicle prototype development is getting shorter, but time should still be reserved to evaluate the performance and interaction between each part, it involves life. For example the Automobile lighting includes headlights, tail lights, fog lights, turn signals, interior lights, reflectors, optical guides, baffles and lenses. The solution for manufacturing the prototyping-of-optical-parts-for-cars includes a series of processes from concept design review to optical system manufacturing and testing, from shell prototype to optical component assembly.
1.Development stage of prototyping-of-optical-parts-for-cars.
engineering prototype.During the design and pre-production process, many prototypes must be made to verify the function or appearance of the final product. After that, the brightness, function, and other basic function parameters of the tail lamp will be tested. It usually takes 1-2 prototypes.

Design verification prototype.The design verification begins once the initial function of the vehicle lighting prototype is approved. This stage aims to optimize the geometric shape of the car lighting and check the assembly for the first time. Generally, the first assembly will encounter many problems that need to be corrected in the design, and the new prototype must be remanufactured to recheck its design because the correction may lead to other problems. This is an iterative process. Generally, no more than 20 prototypes are produced at this stage. The design verification test also includes the strength test. For vehicle lighting and other prototypes, it mainly includes an impact test, throwing some hard objects onto the lens to see if it can withstand a large impact. According to the test results, some materials can be changed to better adapt to the harsh environment and the needs of manufacturers.

Manufacture verification prototype.After the completion of various factors testing, the first attempt will be made to mass-manufacture the prototype of automobile lighting lamps, usually up to 1000 products. This stage is the process of optimizing production.

2.Solutions of manufacturing.
Different methods are usually used to manufacture prototypes at different stages of the development of automotive lighting.
In the first stage, there may be the most iterations because the final design scheme has not yet been determined. Therefore, prototypes should be remanufactured as soon as possible, and they are likely to be completely different from each other. The ideal process at this stage is additive manufacturing, which is 3D printing. This is a method of manufacturing complex free-form parts without mass production preparation. This process includes sintering plastic layer by layer according to the CAD model of the part.
The second stage requires dozens of parts, so 3D printing may no longer be feasible. Automobile lighting lamps are usually made of transparent plastic (polycarbonate or PMMA), so they can be poured into polyurethane molds. Compared with injection molds, the manufacturing speed of polyurethane molds is faster, and the cost is lower. Of course, the mainstream manufacturing method is CNC machining. Purchasing 3-axis, 4-axis, and 5-axis CNC machining services can achieve a higher mirror transparency effect.

The third stage is basically mass-production testing. Therefore, injection molding is the main manufacturing process for manufacturing expensive steel or aluminum injection molds. In order to obtain good lamp transparency and surface finish, grinding machines and polishing methods can be used.
3.Difficulties in manufacturing prototyping-of-optical-parts-for-cars
Manufacturing light guide.Manufacturing light guide is the most difficult part of prototype processing. Light guide is a unique transparent tube, which plays a key role in lighting. When you place a light source at one end of the light guide, the light reflects onto the surface of the guide rail and bounces in the direction of its axis, resulting in a brighter axis with a larger entrance angle. This means that complex light display can be realized and the light looks brighter. Transparent prototype and optical prototype processing materials mainly refer to transparent acrylic (PMMA) and polycarbonate (PC) to achieve clear and transparent mirror surface.
Manufacturing light guides requires precise plastic processing technology. CNC processing technology provides excellent surface quality. The processing radius of optical details will not exceed R0.005 “(R0.125mm), and the processing optical surface tolerance will reach+/-0.001” (+/-0.025mm). Combining the processing capability of the best combination of 3-axis, 4-axis and even 5-axis CNC milling machines, adopt the latest diamond processing technology (SPDM or SPDT), it can match the capability of 5-axis micro-milling, and produce a series of lenses and light guide types with excellent optical quality.

Manufacturing reflector.Use the precision 5-axis CNC machining equipment and high-speed cutting technology to process aluminum reflectors with complex geometry, improved reflectivity, enhanced illumination intensity and light range. Generally, aluminum 7075 or 7022 is used for milling radius of R0.1 or R0.15 mm optical surface, the exposed sharp edges can be rounded to R0.1 mm at most. Perform two 3D scans and roughness measurements, and the final roughness of polishing is Ra(μm) 0.05。 The surface accuracy tolerance of all process scans is within ± 0.05mm.

Solutions of sectioned and glued.For some very complex prototypes, it needs to be sectioned and glued for processing when the 5-axis milling machine cannot be processed. Sectioned and gluing solutions can save processing cost and solve processing constraints. Through proper splitting treatment and excellent finish, obvious adhesive lines on the surface can be cleverly hidden. The lines left by the optical components after bonding can only be covered up by decomposition solution and continuous fine processing.
Polish.Acrylic polishing helps to present the best transparency and transmittance of all transparent plastics. Although PMMA processed by CNC has good surface finish, it is difficult to achieve high definition, which requires polishing with special skills. Because acrylic is a stress-sensitive material and quite brittle. Manual polishing of acrylic requires different levels of polishing process. High-polishing needs to start from 400 # or 600 # abrasive paper, first remove the tool marks on the surface, then gradually lift to 800 # – 1000 # – 1500 #, and finally use 2000 # abrasive paper. The polishing surface will be highly smooth without any machine lines and marks. Finally, we need to use polishing paste to refine the process, and the final surface is super clear and transparent, without any grinding marks and scratches.

Polycarbonate (PC for short) is much stronger than acrylic and has better mechanical properties. Its transparency is only inferior to acrylic acid. We usually use polishing and steam polishing to obtain optical properties similar to acrylic. The polycarbonate polishing process is the same as the manual polishing of acrylic. The surface is polished with abrasive paper from 400 # to 2000 # to remove the processing marks. The steam is boiled in dichloromethane in a closed container, then the steam flows through the polycarbonate surface, and the surface becomes clear and transparent. It is worth noting that after the polishing process, the parts must be sent to a dry environment to evaporate dichloromethane (toxic).
DDPROTOTYPE focuses on providing complete vehicle lighting prototypes, providing professional prototype services for many well-known automobile manufacturers and suppliers around the world. We focus on various automobile prototype development and rapid manufacturing technologies, providing CNC processing, 3D printing, vacuum casting, rapid aluminum mold, small batch injection molding and sheet metal processing. The best combination of 3-axis, 4-axis and 5-axis CNC milling machines, equipped with a machine tool with a stroke of more than 1 meter, has the knowledge to process transparent plastic parts without defects. With effective splitting and binding solutions, highly skilled manual polishing technology, the use of diamond tools can achieve top surface quality, and the smallest tool can be processed to R0.1mm, perfectly presenting the designer’s optical details.