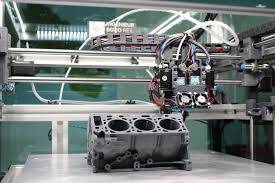
Rapid Prototyping & Rapid Manufacturing Expert
Specialize in CNC machining, 3D printing, urethane casting, rapid tooling, injection molding, metal casting, sheet metal and extrusion
Learning all about rapid prototyping
Rapid Prototyping (RP) is a relatively new term that simply explains the process of rapidly creating prototypes using advanced manufacturing processes, attempting to visually and functionally evaluate the design of new products and continuously optimize the design. Engineers or designers transform great ideas into realistic conceptual models that simulate the appearance and working style of the final product, and undergo a series of validations before moving towards to mass production. A prototype is the original version of the final product, used to evaluate the design, testing techniques, analyze the working principles of the product, adjust the design, materials, dimensions, shape, assembly, color, manufacturability, and strength, timely avoid potential pitfalls, and improve the quality of the final product. This article explores seven currently popular prototyping methods, and compares the material characteristics of parts manufactured by various processes. In addition, the key factors that must be considered in various manufacturing processes are summarized. The purpose is to help designers choose the best prototype manufacturing process.
Definition of rapid prototyping
Rapid prototyping is the process of producing models as quickly as possible to simulate the final product. There are dozens of manufacturing methods that can make prototypes, the most impressive of which is additive manufacturing, namely 3D printing. However, traditional subtractive manufacturing CNC machining can also produce high-quality prototypes. 3D printing and rapid prototyping fit perfectly, enabling the manufacture of parts with almost unlimited geometric shapes, requiring only one printer and no other tools. 3D printing can produce parts with mechanical properties that are very similar to various materials manufactured using traditional manufacturing methods.

7 types of prototype manufacturing processes
Process | Named | DESCRIPTION | FINISH | EXAMPLE MATERIALS |
Stereolithography | SLA | Laser cured photosensitive polymers | Typical additive layers range is 0.002-0.006 inches(0.051-0.152 mm) | Like thermoplastic |
Selective Laser Sintering | SLS | Laser sintered powder | Typical additive layers are around 0.004 inches (0.102 mm) | Like nylon and TPU |
Direct Metal Laser Sintering | DMLS | Laser Sintered Metal Powders | Typical additive layers range is 0.0008-0.0012 inches (0.020-0.030 mm) | Like stainless steel, titanium, chromium, aluminum, and chromium nickel iron alloy metal materials |
Fused Deposition Modeling | FDM | Fused extrusions | Typical additive layers range is 0.005-0.013 inches (0.127-0.330 mm) | Like ABS、PC、PC/ABS、PPSU and other plastic |
PolyJet | PJET | UV Cured Jet Photosensitive Polymers | Typical additive layers range is 0.0006-0.0012 inch (0.015-0.030 mm) | Like PMMA, elastic photosensitive polymer |
CNC Machining | CNC | Use CNC milling machines and lathes to remove excess material | Remove excess material (smooth) | Most of engineering-grade plastics and metals, have hundreds of materials |
Vacuum Casting | VC | Use silicone molds to make replica plastic parts | Smooth or with selected texture | Engineering-grade thermoplastic |
Advantages and disadvantages of different manufacturing methods
SLA
SLA: SLA is the oldest, most popular, and most cost-effective additive manufacturing method, and it is the first 3D printing method applied to commerce. It is a process of using a computer-controlled ultraviolet laser to cure liquid photosensitive polymer resin layer by layer, and repeating the process to manufacture parts. The layer by layer cross sections are derived from CAD design files (. stl format). It is worth noting that CAD files in. stl format have become the default computer language for most 3D printers.

Advantages: Compared to other additive processes, SLA can produce high-quality prototypes and parts with complex geometric shapes. SLA is fast, low cost, and manufactured parts have excellent surface finish and optimal detail, maintaining strict tolerances. There are multiple selectable material libraries, such as optical, mechanical, and thermal properties, to match standard, engineering, and industrial thermoplastics. SLA prototypes are typically used for manufacturing medical prototypes, also for vacuum casting master models.
Disadvantages: SLA manufacturing prototypes often have insufficient strength and are not suitable for testing in extreme situations. In addition, ultraviolet rays weaken over time in humid environments.
SLS
SLS: SLS is a 3D printing technology for manufacturing metal and plastic prototypes. It is a process of creating prototypes layer by layer using computer-controlled high-power laser heating and sintering powder materials, such as nylon or elastic TPU powders similar to engineering grade plastics. SLS technology can be traced back to the 1980s, and was patented by Carl Deckard. Similar to many other 3D printing processes, it can manufacture parts with complex geometric shapes, including internal features, undercuts, thin walls, etc., such as parts with internal lattice structures that are difficult to achieve by CNC machining.

Advantages: Compared to SLA, SLS parts are more accurate and durable, and are suitable for some functional tests.
Disadvantages: The surface of SLS parts has a granular or sandy texture, lacks fine details, and is very rough. Secondary processing is required to achieve aesthetic results, and the materials available are limited.
DMLS
DMLS: DMLS is a 3D printing technology for manufacturing metal prototypes and end use parts, welding powder layer by layer until the part is completed. DMLS parts can be made from most alloy materials, and of course, the same materials as the final parts can be selected to produce full strength and functional prototypes.

Advantages: DMLS can manufacture metal prototypes (typically 97% density) for functional testing, and can manufacture internal features or channels that cannot be accomplished by traditional processes. The mechanical properties of DMLS parts are basically consistent with those of traditional manufacturing parts.
Disadvantages: The surface of DMLS parts is rough and requires expensive post treatment. If DMLS is used to manufacture multiple metal parts, the cost can be high.
FDM
FDM: In the process of melt deposition molding (FDM), thermoplastic materials (such as ABS, polycarbonate, or ABS/polycarbonate blend) are melted in a nozzle heated by the printer, and then the nozzle moves along a set path, laying liquefied resin material layer by layer, creating a prototype from bottom to top.

Advantages: FDM can choose from genuine thermoplastic materials, producing components that are low cost and robust, and capable of performing some functional testing. Of course, this process can also produce parts with complex structures. FDM technology is easy to use, accommodates different types and colors of plastic in the manufacture of a single part, and is safe, clean, and pollution-free enough.
Disadvantages: FDM parts often have some holes, uneven strength, poor surface finish, and obvious ripple marks. Compared to SLA or SLS, FDM is not efficient.
SLM
SLM: SLM is a technology that uses high-power lasers to melt and fuse metal powders to produce prototypes or parts. Common metal powders include titanium, stainless steel, aluminum, and cobalt chromium alloys, which can be used to manufacture precision metal parts with high strength, durability, and complexity.

Advantages: Precision parts manufactured by SLM are widely used in industries such as aerospace, automotive, National defense, and medical treatment.
Cons: SLM-made parts or prototypes can be expensive and need to be controlled by a skilled machinist.
POLYJET
POLYJET: PolyJet uses a printhead to spray photosensitive polymer resin layer by layer, and uses UV curable materials to build prototypes or parts. The resin layer sprayed by this process can be very thin and can produce parts with smooth surfaces. Print heads can be sprayed with different materials, allowing for the construction of multi material prototypes.

Advantages: Polyjet is affordable and can be used to manufacture flexible parts with complex structures, as well as to make prototypes of wrapped molded parts using flexible and rigid materials.
Disadvantages: Polyjet parts are not strong enough for functional testing, and may turn yellow after long-term exposure to light.
CNC machining: The cutters rotate along with a set path to cut solid blocks (or bars) of plastic or metal, removing excess material to produce parts or prototypes, which is a material reduction process. Compared to additives, CNC machined parts have excellent strength and surface finish, and are relatively complete. The range of materials selected is very wide, with thousands of types, which can produce CNC parts with multiple functions, such as tensile strength, impact resistance, thermal deformation temperature, chemical resistance, and biocompatibility. Good tolerances are suitable for assembly and functional testing.

Advantages: CNC parts have good surface finish and strict tolerances, and a variety of engineering grade thermoplastics and metals can be selected. Compared to 3D printing, prototypes can be delivered within 24 hours depending on the complexity of the part.
Disadvantages: For some complex parts, CNC machining may have some limitations. For example, it is very difficult to machine hollow thin-walled parts, and sometimes it is necessary to flip over and fix the workpiece with customized fixtures. Therefore, for machining parts with complex geometric shapes, the cost of CNC machining is relatively high.
Vacuum Casting: Strictly speaking, vacuum casting is a process for manufacturing small batches of parts. The process of defoaming, mixing, preheating, and molding the poured polyurethane material under vacuum conditions, and conducting a 2-3 hour secondary curing molding process in a constant temperature box at 60 ℃ – 80 ℃.

Advantages: The replica made by vacuum casting can reach the strength and hardness of raw materials such as ABS, and can also be equipped with colors according to requirements. The vacuum replica process can produce small batches of plastic parts with complex structures and uniform wall thickness that can meet certain functions and appearances.
Disadvantages: Each mold can produce up to 25 copies (depending on the complexity of the mold and the casting material); If the parts require high quality (such as transparent or complex structures), only 12 or even 10 replicas can be made from one mold.
How much does rapid prototyping cost?
This question is difficult to answer. Rapid prototyping depends on a variety of different factors, with significant differences in costs. For example, if information such as processing technology, size, quantity, surface finish, quantity, material, and surface treatment is uncertain, it is difficult to assess how much it will cost to manufacture a prototype, which can range from tens of dollars to thousands of dollars. If you have completed the design of a prototype project, fell free to contact DDPROTOTYPE, a top rapid prototyping manufacturer in China, to provide you with a free quotation and provide constructive suggestions and feasible solutions for your design for free.