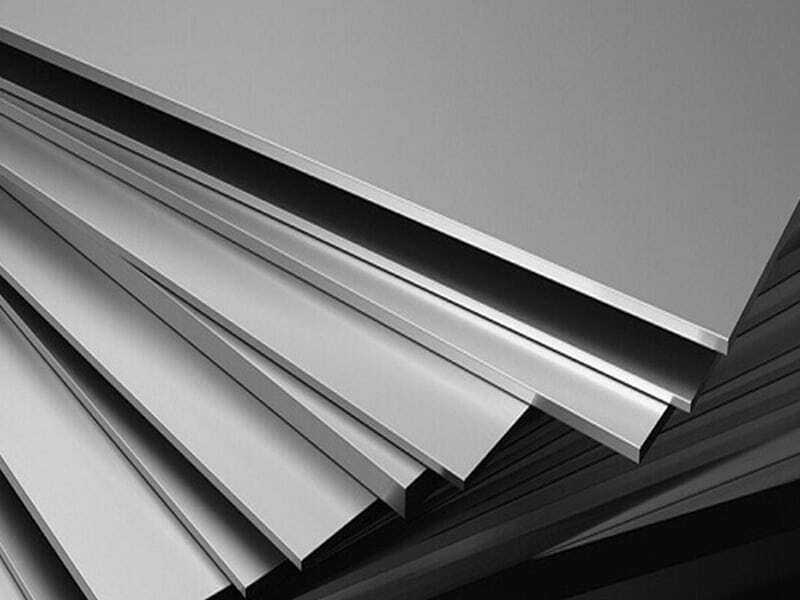
Rapid Prototyping & Rapid Manufacturing Expert
Specialize in CNC machining, 3D printing, urethane casting, rapid tooling, injection molding, metal casting, sheet metal and extrusion
CNC Machining Materials Selective Guide
There are around 21 types of CNC machining materials commonly used. This article will introduce in detail how to choose the right material after the design is determined, which can not only meet the needs of the project, but also save the budget. CNC machining is a versatile, high-precision traditional manufacturing technology, which is a ideal manufacturing processing for complex parts, from one prototype to small batch, high-volume production. Since 1960, CNC machining still be the most ideal option for custom parts. Well knowing that CNC machining is a subtractive process, which means that the machine cuts off a solid piece of material to make a part, so material selection will be an extremely important part of any manufacturing process. As CNC machining is compatible with material ranging from engineering plastics to metals. This creates challenges for designers and R&D teams when selecting materials for CNC projects. Next, let we discuss various key factors need to consider when choosing the right material.
Project requirements
Given the wide range of material options available for CNC machining, it is likely that there will be more than one material suitable for your prototyping or mass-custom parts. However, finding the most suitable CNC cutting material depends on your priorities: do you need a metal with excellent mechanical properties, such as titanium alloy? Or do you prioritize speed and choose a more machinable material (like aluminum 6061) or plastic (like ABS)? Or do you just want to get prototype machined at the lowest possible price?
Applications of CNC parts.Engineers should consider the end use and purpose of the part, which has a major impact on material selection. For example, stainless steel and carbon steel are suitable for CNC machining, but only stainless steel has nature corrosion resistance, wrongly selective of steel will affect the working life of the part. The selective of insulator material for medical ventilators and Nikon cameras is also different. Of course, FDA, FAA and any industry-specific regulations should also be a primary consideration.

Adapt to the particular environment. Outdoor environments and in controlled indoor environments are important factors that affect the working life of parts. If choose oxidation resistance material, as time went by its still maintain integrity. Rigid foam is a good example of moisture and rust resistance, and can maintain a stable complete structure for a long time.
Stress load requirements. High loads of stress will cause some materials get deformation even break. When you are considering which material to use for your parts, make sure you have considered stress loads. If your part is going to be working under high stress, the material it’s made of will need the elements needed to resist loads and prevent deformation. Such as stainless steel, aluminum 7075 and various alloys.
Requirements of tensile strength and temperature. The engineer should determine what kind of strength the part requested (tensile strength, wear resistance, etc,.) and how much t will withstand. These parameters will affect the range of material that can be selected. Temperature requirements exclude some materials from the beginning; almost all materials will expand or contract with temperature changes. Such as materials of precision parts, need to choose inert metals or plastics.
Project budget. Most of time material cost will affects material selection. Material cost is especially important when it comes to CNC machining, as the process will generate relatively large amounts of scrap. Some materials are very expensive (like metal titanium, cobalt-nickel alloys, etc.), considering the output of scrap which will have a significant impact on the cost efficiency of the overall project. So when engineers should carefully evaluate their budget before making the final decision.
Dimensional tolerance. Do not underestimate the importance of dimensional tolerance, in addition to influencing the entire CNC machining process working; it also plays an important role in material selection. And it has impact on the CNC cutting method and what type of tools and machines will be using, so it’s will be best to double checking the tolerance carefully. If the tolerance can be adjust or loosen, you can save money by re-evaluating the tolerance, tighter tolerance usually mean higher production costs. If you are not sure what the exact tolerance for the part you need, just ask for reputable CNC machining supplier DDPrototype to help you figure it out.

CNC machining materials characteristics
We summarized the relevant properties of most common CNC materials, these material properties data collected from material manufacturer. Metal and plastic materials are separated for comparison as the big difference of properties. Metals are mainly used in applications requiring high strength, hardness and heat resistance. Plastics are often used for their chemical resistance and electrical insulating properties. The materials properties of interest were the mechanical strength (expressed as tensile yield strength), the machinability (the ease of machining affects CNC pricing), the material cost, the hardness (mainly for metals) and the temperature resistance (mainly for plastics). The gathered informations were summarized in the tables below. A detailed description of each material option is given in the next section.
Summary table for metals
Material | Grade | Strength* | Hardness+ | Machinability | Cost | Typical applications |
---|---|---|---|---|---|---|
Aluminum | 6061 | Medium | Medium | ★★★★★ | $ | General purpose Aircraft components Automotive parts Bicycle frames Food containers |
6082 | Medium | Medium | ★★★★★ | $ | General purpose Automotive parts Food containers | |
7075 | High | Medium | ★★★★ | $$ | Aircraft & aerospace components Automotive parts Marine applications Sports equipment | |
5083 | Medium | Low | ★★★★★ | $ | Marine applications Construction Pressure vessels | |
Stainless steel | 304 | High | Medium | ★★ | $$ | General purpose Medical devices Food industry Marine applications Chemical processing |
316 | High | Medium | ★★ | $$ | Food preparation equipment Marine applications Architecture Surgical implants Chemical containers | |
2205 Duplex | High | High | ★ | $$$ | Oil & gas Marine applications Chemical processing Heat exchangers | |
303 | High | High | ★★★ | $$ | Aircraft components Machine parts Nuts, bolts, gears, bushings | |
17-4 | High | Very High | ★★ | $$$ | Turbine blades Marine applications Chemical vessels Oil & Gas Nuclear applications | |
Mild steel | 1018 | Medium | Medium | ★★★ | $ | General purpose Machinery parts Jigs & fixtures |
1045 | Medium | High | ★★ | $$ | General purpose Machinery parts | |
A36 | High | Medium | ★★★ | $ | Construction Machinery parts Jigs & fixtures | |
Alloy steel | 4140 | Medium | High | ★★ | $$ | General purpose Machinery parts Tooling |
4340 | High | High | ★★ | $$ | Aircraft landing gear Power transmission Tooling | |
Tool steel | D2 | High | Very High | ★ | $$ | Cold-working tooling Dies & stamps Cutting tools & knives |
A2 | High | Very High | ★ | $$ | Cold-working tooling Dies & stamps Cutting tools & knives | |
O1 | High | Very High | ★ | $$ | Cold-working tooling Dies & stamps | |
Brass | C36000 | Medium | Medium | ★★★★★ | $ | Mechanical parts Valves & nozzles Architecture |
* : Tensile Yield Strength – Medium: 200-400 MPa, High: 400-600 MPa + : Hardness – Medium: 50-90 HRB, High: 90 HRB – 50 HRC, Very High: above 50 HRC
Summary table for plastics
Material | Strength* | Operating temperature+ | Machinability | Cost | Typical applications |
---|---|---|---|---|---|
ABS | Medium | Up to 60oC | ★★★ | $ | Automotive Electronic enclosures Pipes & fittings Consumer products |
Nylon | High | Up to 100oC | ★ | $ | Automotive parts Mechanical parts Fasteners |
Polycarbonate (PC) | High | Up to 120oC | ★★ | $ | Architecture Automotive Electronic enclosures Food containers |
POM (Delrin) | Medium | Up to 82oC | ★★★★ | $ | Mechanical parts Electronic enclosures Bushings & fittings |
PTFE (Teflon) | Low | Up to 260oC | ★★★★ | $ | High temperature applications Chemical processing Electronic enclosures Food processing |
HDPE | Low | Up to 80oC | ★ | $ | Chemical containers Pipes & fittings Consumer products |
PEEK | High | Up to 260oC | ★★ | $$ | Medical applications Chemical processing Food processing High pressure valves |
* : Tensile Yield Strength – Low: 5-30 MPa, Medium: 30-60 MPa, High: 60-100 MPa + : Recommended maximum operating temperature for constant use
Overview of common CNC metal alloys
Aluminum alloys. Aluminum alloys have an excellent strength, high thermal and electrical conductivity and natural protection anti corrosion. They can be easily machined and with low bulk cost, so they are the most economical option for creating custom metal parts and prototypes usually. The strength of aluminum alloys lower than steel generally, but they can be anodized, creating a hard and protective layer on surface.


Aluminum alloys
Material characteristics: Typical density of aluminum alloys 2.65-2.80 g/cm3, can be anodized, non-magnetic.
Aluminum 6061.Aluminum 6061 is the most common aluminum alloy, with excellent mechanical properties, such as high strength, corrosion resistance and weldability.
Aluminum 7075.Aluminum 7075 has excellent fatigue properties, and can be heat treated to high strength and hardness, which comparable to steel. Commonly used in aerospace applications, like the aircraft wings.
Aluminum 2024.Aluminum 2024 has high heat resistance, impact resistance and excellent fatigue properties, generally used in military and aerospace applications.
Aluminum 5052.Aluminum 5052 has strong chemical and corrosion resistance. It is cannot do heat treatment, usually used in marine applications.
Aluminum 6063.Aluminum 6063 has medium strength and reinforce alloy with heat treatment. Commonly used in aluminum door and window and curtain walls frame.

Stainless steel.
Stainless steel (SS) is most commonly used material in CNC machining. Stainless steel covers a wide range of grades such as SS303, SS304,SS316 etc,. The difference of all material in SS range lies in the amount of doping material added. Sulfur is added in SS303 for better machinability and corrosion resistance. Nickel and chromium are added in SS304 for enhance the strength and reduce the magnetic properties. However, SS316 can be made of marine grade stainless steel by adding molybdenum alloy, which can be used in manufacture large ships.
Material characteristics: Typical density 7.7-8.0 g/cm3 , Non-magnetic stainless steel alloys: 304, 316, 303, agnetic stainless steel alloys: 2205 Duplex, 17-4.
Stainless steel 304.Stainless steel 304 as the most common stainless steel, has excellent machinability, corrosion resistance.
Stainless steel 316.Stainless steel 316 is another common stainless steel alloy with similar mechanical properties to 304. It has a higher corrosion and chemical resistance though, especially to saline solutions (for example seawater), so it is often preferred for applications in harsh environments.
Stainless steel 2205 Duplex.Stainless steel 2205 Duplex is the stainless steel alloy with the highest strength (double than other common stainless steel alloys) and has excellent resistance to corrosion. It is used in severe environments, with many applications in the Oil & Gas industry.
Stainless steel 303.Stainless steel 303 has excellent toughness, but lower corrosion resistance compared to 304. Due to its excellent machinability, it is often used in high-volume applications, such as the manufacturing of nuts and bolts for aerospace applications.
Stainless steel 17-4.Stainless steel 17-4 (SAE grade 630) has mechanical properties comparable to 304. It can be precipitation hardened to a very high degree (comparable to tool steels) and has excellent chemical resistance, making it suitable for very high-performance applications.
Mild steel
Mild steel has good mechanical properties, great machinability and good weldability. Due to their low cost, they find general-purpose applications, including the manufacturing of machine parts, jigs, and fixtures. Mild steels are susceptible to corrosion and attacks from chemicals.
Material characteristics: Typical density 7.8-7.9 g/cm3, Magnetic.
Mild steel 1018.Mild steel 1018 is a general-use alloy with good machinability and weldability and excellent toughness, strength, and hardness.
Mild steel 1045.Mild steel 1045 is a medium carbon steel with good weldability, good machinability, and high strength and impact resistance. Usually used for manufacturing nuts, bolts, gears, shafts, connecting rod and other small machine parts.
Mild steel A36.Mild steel A36 is a common structural steel with good weldability. It is suitable for a variety of industrial and construction applications.
Alloy steel
Alloy steel contain other alloying elements in addition to carbon, resulting in improved hardness, toughness, fatigue and wear resistance, but alloy steels are susceptible to corrosion and attacks from chemicals.
Material characteristics: Typical density 7.8-7.9 g/cm3 , Magnetic.
Alloy steel 4140.Alloy steel 4140 with good strength and toughness, this alloy is suitable for many industrial applications but is not recommended for welding.
Alloy steel 4340.Alloy steel 4340 can be heat treated to high levels of strength and hardness, while maintaining good toughness, wear resistance and fatigue strength. This alloy is weldable.
Tool steels
Tool steels are metal alloys with exceptionally high hardness, stiffness, abrasion and thermal resistance. They are used to create manufacturing tools (hence the name), such as dies, stamps, and molds. To achieve their good mechanical properties, they must undergo a heat treatment.
Material characteristics: Typical density 7.8 g/cm3 , Typical hardness: 45-65 HRC.
Tool steel D2.Tool steel D2 is a wear-resistant alloy that retains its hardness to a temperature of 425°C. It is commonly used to manufacture cutting tools and dies.
Tool steel A2.Tool steel A2 is an air-hardened general purpose tool steel with good toughness and excellent dimensional stability at elevated temperatures. It is commonly used to manufacture injection molding dies.
Tool steel O1.Tool steel O1 is an oil-hardened alloy with a high hardness of 65 HRC. Commonly used for knives and cutting tools.
Brass
Brass is a metal alloy with good machinability and excellent electrical conductivity. It is commonly used in architecture to create parts with a golden appearance for aesthetic purposes. Common brass grade are C35300 and C36000.
Material characteristics: Typical density 8.4-8.7 g/cm3, Non-magnetic.
Brass C35300.Brass C35300 has excellent corrosion resistance and wear resistance.
Brass C36000.Brass C36000 with high tensile strength and nature corrosion resistance. It is one of the most easily machinable materials, so it is often used for high volume applications.

Titanium alloys
Titanium is also biocompatible and suitable for medical device manufacturing, such as artificial bones. Titanium can be welded, passivated, and anodized to increase protection and improve it appearance.
Material characteristics: Typical density 4.5-4.51g/cm3 , Non-magnetic
Titanium is not particularly polished and is a poor conductor of electricity, but a good conductor of heat.
Engineers should also be aware of the challenges of CNC machining titanium, as it is difficult to do machining, and requires special cutting tool.
Magnesium
Magnesium is the lightest metals widely used for precision CNC machining. The specific gravity of magnesium is about 2/3 of aluminum, and 1/4 of iron.
Material characteristics: Typical density 1.8g/cm3 , Non-magnetic
Magnesium has excellent machinability, strength and robustness make it widely used in multiple industrial sectors. If you want your customized parts to have a combination of light weight, high strength, high rigidity, good heat dissipation, greater impact load capacity than aluminum alloys and corrosion resistance, then magnesium alloys are very good options. Magnesium alloy parts widely used in new energy vehicles, pharmaceuticals and chemicals, aviation, aerospace industry, 3C products, robots and other fields.
Magnesium alloy is an active metal, which can create chemical reaction in the air and is easy to oxidize. In order to improve the working life of the part, usually will take some professional surface treatment, such as micro-arc oxidation, electroplating, painting, powder coating, passivation and so on purpose for maximize improve the practicability.
The storage of magnesium alloys must be sealed at low temperature, and D-Type extinguishers and sand piles should be reserved for fire fighting. In the CNC machining process, the speed cannot be too fast; otherwise it will cause fire during the machining process. Also need use special magnesium alloy cutting fluid.
Inconel
Inconel is high temperature alloy that has gained popularity in recent years due to its many special properties. Inconel parts are suitable for environments that may be subject to water corrosion or oxidation. It is also ideal for environments where parts may be subjected to extreme pressure and heat.
In addition above mentioned material, there are several materials that are compatible with precision CNC machining processes. Such as cemented carbide, tungsten, palladium, invar, nickel, niobium, steel alloys, beryllium, cobalt, iridium and molybdenum. After considering the field of application of the custom part, it is crucial to choose the right material from among several options, as it determines the success of the CNC machining process and the cost also.
Overview of commonly used plastic material in CNC machining
CNC machines can cut the plastic also. In most cases, the following 7 plastics can be preferred for the cost, electrical insulation or other reasons. When the final part is injection molded, plastic is usually a suitable prototype material.
ABS
Material characteristics: Typical density 1.00-1.05g/cm3
ABS is one of the most common thermoplastic materials offering good mechanical properties, excellent impact strength, high heat resistance and good machinability. And widely used in injection molding mass production.
Nylon
Material characteristics: Typical density 1.14g/cm3.
Nylon is also known as polyamide (PA) and is a thermoplastic that is often used for engineering applications, due to its excellent mechanical properties, good impact strength and high chemical and abrasion resistance. It is susceptible to water and moisture absorption though. Nylon 6 and Nylon 66 are commonly used grades in CNC machining.
Polycarbonate
Material characteristics: Typical density 1.20-1.22g/cm3.
Polycarbonate is a thermoplastic with high toughness, good machinability and excellent impact strength (better than ABS). It can be colored, but typically it is optically transparent, making it ideal for a wide range of applications, including fluidic devices or automotive glazing.
POM (Delrin)
Material characteristics: Typical density 1.40-1.42g/cm3.
POM is commonly known with the commercial name Delrin, and it is an engineering thermoplastic with the highest machinability among plastics. POM (Delrin) is often the best choice when CNC machining plastic parts that require high precision, high stiffness, low friction, excellent dimensional stability at elevated temperatures and very low water absorption.
PTFE (Teflon)
Material characteristics: Typical density 2.2g/cm3.
PTFE is commonly known as Teflon, and is an engineering thermoplastic with excellent chemical and thermal resistance and the lowest coefficient of friction of any known solid. PTFE (Teflon) is one of the few plastics that can withstand operational temperatures above 200°C and is an outstanding electrical insulator.
HDPE
Material characteristics: Typical density 0.93-0.97g/cm3.
High-density polyethylene (HDPE) is a thermoplastic with a high strength-to-weight ratio, high impact strength, and good weather resistance. HDPE is a lightweight thermoplastic, suitable for outdoor use and piping.
PEEK
Material characteristics: Typical density 1.32g/cm3.
PEEK is a high-performance engineering thermoplastic with excellent mechanical properties, thermal stability over a very wide range of temperatures and excellent resistance to most chemicals. PEEK is often used to replace metal parts due to its high strength-to-weight ratio. Medical grades are also available, making PEEK suitable also for biomedical application.
Other CNC machining materials
In addition common used metals and plastics, wood and foam are used in CNC machining also, but not as the preferred material usually.
Wood.Wood is usually fewer choices, just hardwood, plywood, softwood, etc.
Rigid foam.Rigid foam serves as the foam with the highest insulation value. It can perform in temperatures as low as -100° F and as high as 200° F. Rigid foam also holds a higher R-value, which makes it a premium choice for floors, walls and other structure-based products that need to withstand moisture.
Carving foam.Carving foam can take on nearly any shape. It’s usually used as a model for molds because of its flexibility, but it’s also used in components such as gaskets and seals. Carving foam contains polyisocyanurate, which is dense and resistant to extreme temperatures.
Phenolics.If you need to meet military-grade specifications such as MIL-I-24768, phenolics can meet this requirement. There are several to choose from, such as CE, LE, G10, G10/FR4, G9, G11 and G7. Each has its own set of strengths. For example, the fine weave of phenolic linen yields good mechanical properties, dimensional stability and a better finish for machined components than CE material. However, phenolic linen is not suggested for electrical primary insulation. LE phenolics meet Mil-I-24768/13 FBE requirements, while CE phenolics meet Mil-I-24768/14 FBG requirements.
Summary
Which CNC machining material you will ultimately use for your parts depends on the project you are creating, we make a summary that can be used as a short CNC machining material selective guide.
Don’t assume metals are your best option. Non-metallic materials have become popular because they are lightweight yet durable — like foam you can mold into various shapes. Non-metals also retain small details during cutting. If your project seems like one that may benefit from the use of non-metals, plenty of options can benefit your final product.
Aluminum 6061 is the most common CNC machining metal material at lowest cost.
POM (Delrin) is the most economical CNC plastic because of its excellent machinability.
If request part with high strength, hardness or high temperature resistance, alloys will be preferred choice.
ABS is ideal option for lightweight applications, CNC machined ABS parts are often used as prototypes prior to mass-production with injection molding.
This is not an exhaustive list of CNC machining material, and CNC machining is a versatile manufacturing process that requires a thorough evaluation of project requirements, in order to select the most suitable material for the part. Still, achieving the ideal balance of cost, quality, and time remains challenging.
DDPROTOTYPE specialize in rapid prototyping manufacturing & mass production over 20+ years, till of today we have 40+ senior engineers with range of technologies can provide professional solutions. 50+ kinds of surface finishing options, over 60+ certified materials in metal/plastic can cover different rapid prototyping needs.
Let DDPROTOTYPE’s expert to guide you every step of the way, and make every step of the production process easier. By analyzing your design file, evaluating CNC project manufacturing feasibility, and proposing with cost-effective advice to make your CNC machining project processing more smoothly.