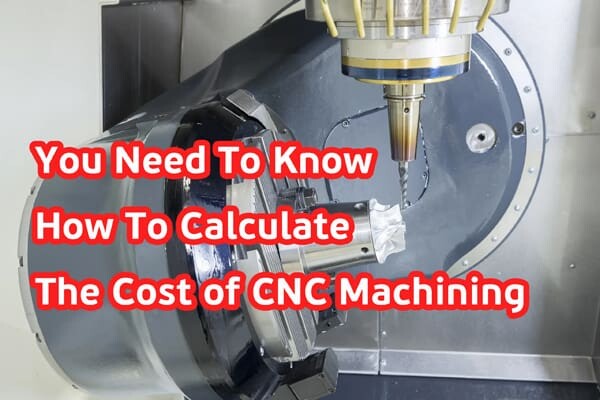
Rapid Prototyping & Rapid Manufacturing Expert
Specialize in CNC machining, 3D printing, urethane casting, rapid tooling, injection molding, metal casting, sheet metal and extrusion
You need to know how to calculate the cost of CNC machining
Although 3D printing is a hot topic in the world of manufacturing today, there is no denying that CNC machining remains one of the most cost-effective methods of on-demand production and is the preferred choice for manufacturing custom parts. CNC machining materials include hundreds of metals and engineering plastics. After determining the 3D drawings, are you confused about the cost of CNC machining? After submitting the CNC project to CNC machining suppliers in local or China, the respective quotations vary greatly.For example, the quotation from China is even 30%-50% lower than that of European and American countries. This is normal, there are many factors that affect the quotation of CNC machining, and there is no fixed cost that can be universally applied to different machining projects. The following tips read for 5 minutes, let you know how to calculate the cost of CNC machining, and provide some tips for optimizing your budget.
1.Factors affecting the cost of CNC machining
The cost of CNC machining involves labor, machinery, complexity, materials, and more. Designers should be aware of the various factors that affect price, and sometimes re-selection of materials or surface finishes can significantly reduce the cost of CNC machining while still meeting the needs of the project. CNC machine shops consider the following key factors when determining project costs:
① labor cost.
The CNC machine requires little human intervention once it is set up. A machinist, engieer or programmer must complete certain tasks before a CNC machine can work properly.

Programming. Programmers must convert CAD files into CAM files for CNC machine tools to execute code.
Mechanic. The mechanic will set up and adjust the machine for production, and someone always needs to cut the blank, place it in the workholding, and put the tool in place for the CNC machine to work.
Regular training. Any company has to keep up with the times, and even the most experienced mechanics will not fully grasp all the knowledge, which requires regular learning and communication, and this requires some cost.
Post-processing. After the production of custom parts, some post-processing processes are required, such as anodizing, painting, polishing, plating ,etc., which require manual participation. In addition, trial assembly create additional manual labor.
Please note: Labor is one of the important factors of CNC machining costs, that is why manufacturing is mostly located in Asian countries.
②Various costs of CNC machines.
CNC machining suppliers use machines such as CNC milling machines and CNC lathes for part fabrication. 3- and 5-axis mills and lathes provide flexibility for designing parts with complex geometries and tight tolerances. Tooling costs depend on the type of machine and the number of hours it will run, often referred to as machining time.


Different price of a single CNC machine. A production-grade 3-axis CNC machine costs $80,000 to $200,000; a production-grade 5-axis CNC machine costs $200,000 to $400,000; These machines are usually Japanese or American brands.
Different rates. CNC machining suppliers set hourly rates for the operation of different types of machines. 3-axis milling machine and 5-axis milling machine have different charges. In Europe, a three-axis machine costs about $35-40 per hour, while a multi-axis machine costs about $75-120 per hour; in China, the same hours are $10 and $30. The advantages offered by each machine depend on the geometric complexity of the part.
Depreciation costs. CNC machining suppliers must also consider the depreciation cost of the machine.
Please note that not all parts have to be machined through precision 5-axis CNC equipment to achieve the best quality.
③Part features
The characteristics of a part refer to the geometry and complexity in the design. Parts with complex features including sharp interior corners, thin walls, deep cavities, non-standard hole sizes and lettering which require more programming time, run time and setup time. Complex parts may also require specialized tooling, multiple setups, and specific CNC machines to manufacture, adding to the cost of the final product, such as an impeller that must require a 5-axis CNC machine.

Note that it is beneficial to simplify the design as much as possible to reduce the cost per part. In some cases, it may be more cost-effective to split the design into multiple parts and then assemble them.
④Material
The cost and machinability of materials will be the main factors that determine the cost of CNC machining. The subtractive manufacturing process removes material sequentially, so the amount removed is related to processing time and price. Different materials and sizes have obvious differences in the calculation of CNC machining costs, taking 6″x6″x1″ sheet as an example.
ABS is priced at $17 per block
POM (Delrin) is priced at $27 per block
Nylon 6 is priced at $30 per block
Aluminum 6061 is priced at $25 per block
Aluminum 7075 is priced at $80 per block
Stainless steel 304 is priced at $90 per block


Note that you will be charged for the overall sheet. Aluminum and plastic can be produced faster and at lower cost. The general rule of thumb is to choose the cheapest material when it comes to functionality and aesthetics.
⑤ Fixtures
During the CNC machining process, if the part needs to be turned over, then a fixture is necessary; if you need a custom fixture to fix the workpiece, you will need to pay for the extra fixture production.

⑥Production Volume
Reduce CNC machining costs through mass production. larger orders reduce the unit cost per item. For example, let’s say you want to order 10 units. CNC machining suppliers may price it at $9.99 per piece, which means you’ll pay $99.9 in total. However, if you ordered 100 units, the unit price might be $2.11,so totally $211.It’s understandable that once the design is complete, the CNC machining can be reused many times at no additional cost. According to incomplete statistics, the cost of each part is inversely proportional to the number of parts manufactured, and the unit cost of producing 1000 pieces is about 2 or3times lower than the cost of an independent unit.

⑦Part tolerance
Tolerances are usually given in hundredths or thousandths of an inch. Depending on the complexity and requirements of the part, tight tolerances will add the overall cost; therefore, if not necessary,we’d better not to set tight tolerances. Typical tolerance accuracy ranges from +/-0.02mm to 0.1mm, depending on detailed requirements.

⑧ Surface finishing
If the part requires additional finishing, the total cost will definitely be higher. These treatments include polish, brushing, painting, plating , anodizing and any other special finish. However, before implementing these treatments, their necessity and value should be assessed.
⑨ Accuracy of CAD drawings
Inaccurate and incomplete CAD drawings can ultimately lead to very expensive parts to produce. This is because incorrect information on the model can cause the part to be made twice. Considering the cost and efficiency of part machining, designers and CNC machining suppliers need to maintain close communication.
⑩ Profits of CNC machining suppliers
Each CNC processing supplier faces different problems, and the approved profits are also different. Generally speaking, the cost performance of CNC processing suppliers in China is obvious to all.
2. Skills to reduce the cost of CNC machining parts
Above we list the factors that affect the cost of a CNC project, usually, the most important is the time it takes to machining the part. Machining time is directly affected by your choice of material, geometry of part, tolerances set in drawings, type of machine required, as well as the skill level of the machinist required to achieve the part, etc., which affects cost. We’ve rounded up 10 tips to help you optimize your design and make more cost-effective choices.
①Optimize material selection
The material chosen affects the cost of raw materials and their machinability. Generally speaking, softer materials are easier to cut, such as aluminum 6061 and plastic are more common sources of CNC custom parts.
② Weigh the quantity
For the same part, ask the CNC machining supplier for prices in different quantities; and make a balance between price and quantity.
③ Carefully evaluate the finish
Whether surface treatments such as heat treatment, special coatings and anodizing have a significant impact on the function of the part, if it is not necessary, there is no need to make additional costs for the part.
④ Avoid complex geometric shapes
Use flat surfaces instead of curved surfaces whenever possible. For complex geometries, perhaps only a 5-axis CNC machine can meet the requirements.
⑤ Avoid thin walls
Parts with excessively thin walls—usually defined as thinner than 0.794 mm (1/32 inch)—can cause deformation during CNC machining, and can also cause shaking and broken, reduce machining speed, and increase machining time. If thin walls are necessary, then consider sheet metal fabrication, which is a more cost-effective process.
⑥Minimize deep cavity
Designing parts with deep cavities affects machining time. Drills are difficult to remove chips, and the slender tools required may easily break. Best practice is to keep the cavity depth at most one quarter of the part length.
⑦Keep the inner corners of the rounded corners
Tools such as mills and end mills automatically leave rounded inside corners, and narrow inside corner radii with an aspect ratio greater than 3:1 require more passes and special small tools, increasing machining time and requiring tool changes. Designers or Mechanical Engineer can reduce machining time and tool changes by maintaining the same radius for all interior corners.
⑧Maintain standard tolerances
Not every part needs tight tolerances. Typically, tolerance callouts are designed only for surfaces and features that are critical to the function and assembly. For not critical features, we can machining the parts with a standard tolerance of +/- 0.127 mm (+/- 0.005 in).
⑨Use standard drilling and tapping hole sizes
Standard hole size and standard drill size designs help reduce costs in many ways. A good rule of thumb is to have a thread depth of at most three times the hole diameter.
⑩Ensure the accuracy of CAD files
Consult an experienced machinist or engineer during the design phase to verify the accuracy of the CAD files. Likewise, consulting a knowledgeable manufacturer during the design phase can help you avoid designing unnecessarily expensive or difficult-to-machine parts. This can help you design parts that are functional and cost-effective to manufacture.
3.Outsource your CNC project
As you can see, there are many factors to consider when calculating the cost of CNC machining project. It’s important to keep these in mind when setting your budget.
If you’re still wondering As you can see, there are many factors to consider when calculating the cost of a CNC machining project. It’s important to keep these in mind when setting your budget. If you’re still wondering “How much does CNC machining cost?” then it’s time to get in touch with the professionals. Outsourcing your project is another great way to reduce CNC machining costs. Chinese companies are famous for their very affordable CNC machining prices, which attract many well-known companies in the world for CNC projects, especially in Shenzhen, where there is a strong supply chain and extremely convenient transportation, which increases competition for turning your ideas into reality.