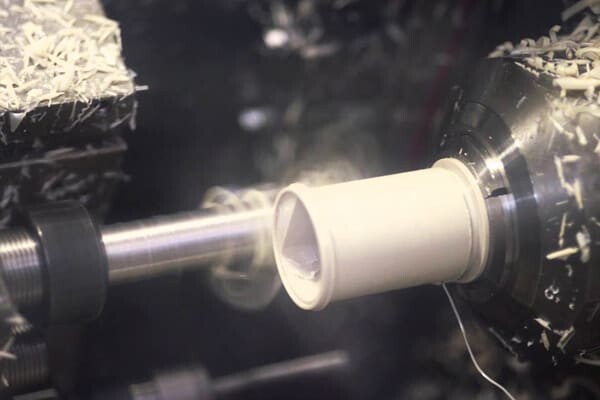
Rapid Prototyping & Rapid Manufacturing Expert
Specialize in CNC machining, 3D printing, urethane casting, rapid tooling, injection molding, metal casting, sheet metal and extrusion
What You Should Know About CNC Machining PEEK
Polyetheretherketone (PEEK) is a high-performance engineering thermoplastic used to manufacture parts exposed to high temperatures, chemicals and other harsh environments. It is prone to cracking during processing and requires special experience and knowledge to handle. PEEK is also a very pure polymer with excellent abrasion resistance, heat resistance, corrosion resistance, dimensional stability, biocompatibility and non-absorption of water. This lightweight thermoplastic is an ideal replacement for most soft metals.
1.Overview of PEEK
Similar to PPS, PEEK is chemically and water-resistant, while with a melting point of 343°C, it can work at higher temperatures. It can be continuously subjected to high temperatures of 250°C without permanent loss of physical properties. PEEK materials are available in the form of pellets, filaments, sheets, bars and tubes with unfilled, also can be reinforced strength with 30% glass fiber filled and 30% carbon fiber . It is usually classified as industrial grade or medical grade. Industrial-grade PEEK plastics are used in the aerospace, automotive, chemical, electronics and energy industries, while medical-grade PEEK plastics are used in healthcare and dentistry.

At A Glance
Processes | Lead Time | Colors | Tolerance | Price | Applications | Grades |
CNC Mill | As fast as 3 days | Opaque beige | With drawing: as low as +/- 0.005 mm | $$$ | Metal-alternative for high-stress applications | Standard PEEK, 30% Glass Filled |
Material properties
PEEK | |||||
Yield Strength (tensile) | Elongation at Break | Hardness | Density | Maximum Temp | McMaster Part Number |
14,000 psi | 20% | Rockwell R125 | 0.047 lbs / cu. in. | 480°F | 8504K811 |
PEEK (30% Glass Filled) | |||||
Yield Strength (tensile) | Elongation at Break | Hardness | Density | Maximum Temp | McMaster Part Number |
14,000 psi | 3% | Rockwell R126 | 0.054 lbs / cu. in. | 480° F | 8678k14 |
Design Recommendations
Min Wall Thickness | Min End Mill Size | Min Drill Size | Max Part Size | Undercuts | Grades |
0.5 mm | 0.8 mm (0.03 in) | 0.5 mm (0.02 in) | 1200 x 500 x 152 mm [x,y,z] (mill) 152 x 394 mm [d,h] (lathe) | Square profile, full radius, dovetail profiles | Depth must not exceed 12x drill bit diameter. For end mills, depth must not exceed 10x tool diameter. |
CNC machining of PEEK parts
Custom PEEK components include: Rollers and Wheels, Bearings, Bushings, Seals, Gaskets, Piston Parts, Medical Implants, Orthopedic Instruments, Drug Delivery Systems, Dental, and etc.


2.PEEK CNC machining suggestion
Annealing process. CNC machining shops typically stock bars with diameters ranging from 6mm to 150mm. Before machining, PEEK must be stress relieved by an annealing process. This is to prevent the formation of surface cracks and internal stress due to heat generated during cutting. In long-time PEEK machining, additional annealing procedures are required, such as an annealing procedure before roughing, and a second annealing before finishing to eliminate the possibility of crack formation. The cost factor for PEEK CNC machining is 0.9 compared to steel 12L14.
Type | General Characteristics | Alloy | Common Applications | Tolerances for 1/2″ Dia. | Material Cost Factor | Machining Cost Factor |
High strength plastic resin, extremely high resistance to heat, moisture, and chemicals | PEEK | Bearings, Bushings, Pump components, Medical implants, Aerospace components | +0.004-0 | 71.6 | 0.9 | |
Compared with other materials | ||||||
Type | General Characteristics | Alloy | Common Applications | Tolerances for 1/2″ Dia. | Material Cost Factor | Machining Cost Factor |
Designed for excellent machinability. Case hard only | 12L14 | Endless commercial products; probably more pounds used in turned products than any other material | Cold drawn | 1 | 1 | |
Designed for machining, non-magnetic | 303 | Electronic hardware, automotive, aerospace, medical instruments, and many applications requiring corrosion resistance | Cold finished | 1.9 | 2.7 | |
Strength, corrosion and wear resistance, and excellent machinability | C35300 | Well suited for parts with knurling or threading | +0015 | 3.5 | 0.07 | |
Designed for machining | 2011 | Electronic hardware, endless commercial products | Cold finish | 3.8 | 0.6 | |
High strength, light weight, good bio-compatibility | Ti-6Al-4VEli | Medical implants | Ground & polished | 30.2 | 6 |
Soften PEEK before machining. Industrial grade machining method is similar as most medical grade PEEK polymers. However, medical grade PEEK will often contain harder carbon fibers, which requires softening the PEEK material prior to machining, thereby reducing tool wear. DDPROTOTYPE, a leading prototyping company in China, summarizes cutting data based on 20+ years of machining experience to help designers understand the machining technology of traditional medical grade and carbon fiber reinforced PEEK polymers.
Machining Guide | ||
| Natural | Carbon-fiber-reinforced |
Sawing | — | Preheat material to 120 C degrees |
Clearance angle—degrees | 15 to 30 | 15 to 30 |
Rake angle—degrees | 0 to 5 | 10 to 15 |
Cutting speed—m/min | 500 to 800 | 200 to 300 |
Pitch—mm | 3 to 5 | 3 to 5 |
| ||
Drilling |
| Preheat material to 120 C degrees |
Clearance angle—degrees | 5 to 10 | 6 |
Rake angle—degrees | 10 to 30 | 5 to 10 |
Cutting speed—m/min | 50 to 200 | 80 to 100 |
Feed rate—mm/rev | 0.1 to 0.3 | 0.1 to 0.3 |
| ||
Milling |
| No material preheat is necessary |
Clearance angle—degrees | 5 to 10 | 15 to 30 |
Rake angle—degrees | 10 to 30 | 10 to 15 |
Cutting Speed—m/min | 50 to 200 | 200 to 300 |
| ||
Turning |
| No material preheat is necessary |
Clearance angle—degrees | 6 to 8 | 6 to 8 |
Rake angle—degrees | 0 to 5 | 2 to 8 |
Cutting speed—m/min | 250 to 500 | 150 to 200 |
Feed rate—mm/rev | 0.1 to 0.5 | 0.1 to 0.5 |
Use professional tools.DDPROTOTYPE also recommends using silicon carbide cutter for natural PEEK and diamond tools for carbon fiber reinforced PEEK. It should also be noted that during machining, pure water is used as a coolant to eliminate the cutting heat generated during machining.
Drilling holes. Deep hole drilling of PEEK can cause cracks,because PEEK has a lower elongation compared to other plastics.
Prevent pollution. It is same as machining other medical components. the workpiece must be prevented pollution during machining PEEK, the CNC machine, clamping fixtures and tools of the workpiece must be protectedand divided from others, and cannot be mixed with other tools, the operator must wear gloves.
3.Other manufacturing processes
PEEK materials are not limited to CNC machining, they can also be processed by 3D printing or injection molding. What manufacturing process to be selected depends on the desired end product, time and budget.
For 3D printed PEEK parts, which are becoming more and more popular in the medical field, parts with complex geometries can be easily realized, especially for medical implants, the optioned materials are mostly in the form of FFF filament and SLS powder. PEEK injection molded parts are widely used in the medical and aerospace fields. However, its melting point is at a higher temperature that exceeds the upper limit of the capabilities of many injection molding machines. Therefore, in the injection molding manufacturing, PEEK is considered as a special material. You can also choose other high temperature materials such as PEKK or Ultem.
Machining | CNC Machining | 3D printing | Injection molding |
Complex geometries | Okay | Okay | Good |
Mechanical performance | Good | Good | Okay |
Accuracy & repeatability | Good | Good | Okay |

4.Surface treatment
The natural color of PEEK parts is opaque gray. Due to the structure of PEEK is difficult to bond to paints and coatings. Fortunately, due to PEEK’s inherent chemical resistance, it is often possible to keep parts in their machined condition.
As Machined: Using CNC machining process, PEEK parts can achieve a surface finish of 125 uin Ra. That is quite smooth.
Bead Blast: The surface can be ground by a glass bead machine to remove any marks on PEEK parts
Other services:including polishing, edge finishing, laminating, decal application.
5.Common Questions about PEEK CNC Machining
Q1: What is the reason for the deformation of PEEK CNC machining?
There is no annealing step to remove the internal stress, or the internal stress is not completely removed.
The CNC cutting depth is too deep.
No coolant to remove heat generated during cutting.
Irregular, uneven cutting, or more cuts on one side than otherside.
The clamps are not strong enough, which causing vibrations.
The clamp is too tight,whichdeforming the workpiece.
Q2:How to fix burrs on PEEK parts?
Because PEEK has the characteristics of high toughness, it is easy to have burrs in the process of machining. After more than ten years of experience of DDPROTOTYPE, there are currently four methods to remove burrs.
Keep the tools sharp, preferably diamond tools.
Add chamfer feature to get rid of the burr from edges.
Use second operation progress to remove the burr.
It is best to use glass filled or carbon filled PEEK material, common types of PEEK is do easyto haveburrs.
As a professional on-demand manufacturing company with over 20 years experience, DDPROTOTYPE offers a wide range of PEEK manufacturing services, ensuring high quality PEEK parts to your specifications at a very economical cost. If you have any questions about the PEEK project, please feel free to contact our manufacturing specialists, DDPROTOTYPE will provide you with free advice on design and material machining experience.