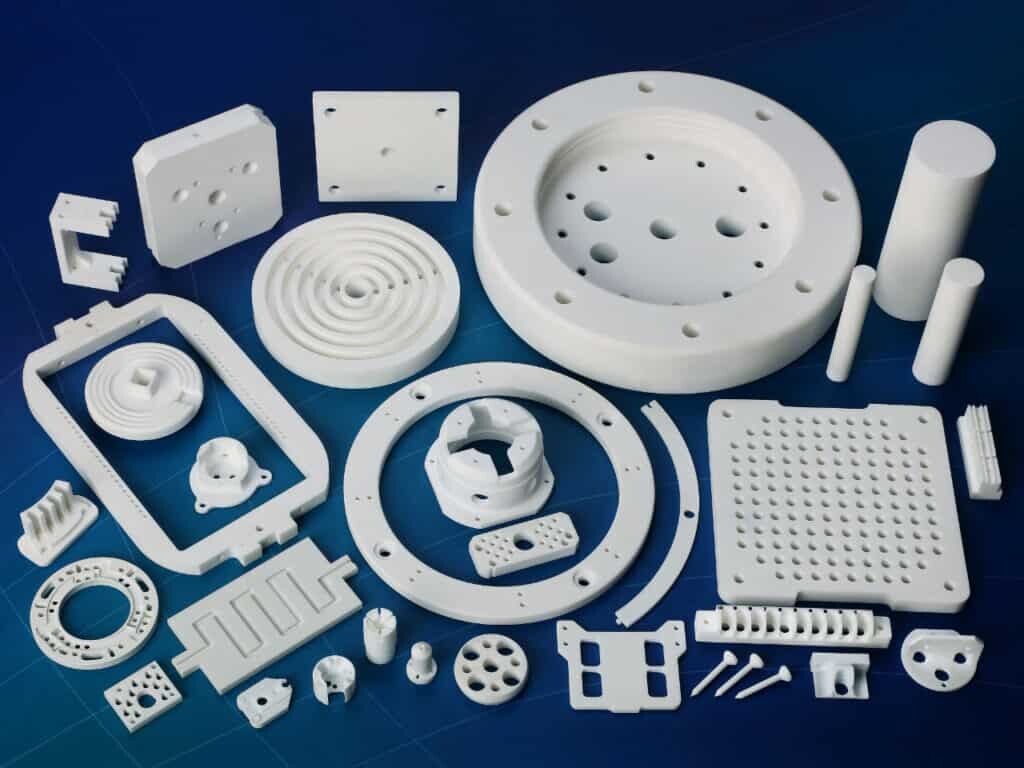
Rapid Prototyping & Rapid Manufacturing Expert
Specialize in CNC machining, 3D printing, urethane casting, rapid tooling, injection molding, metal casting, sheet metal and extrusion
Precautions for CNC Machining Ceramic Parts
CNC machining Ceramic parts have high temperature resistance, corrosion resistance, wear resistance, insulation and other properties, and widely used in semiconductors, optical fiber communications, lasers, medical equipment, petroleum, metallurgy, electronics and other industries. With the development of industry, the processing technologies of ceramic parts have become diversified, such as dry pressing through high-purity ceramic raw materials, high temperature sintering and CNC milling machining of the machinable ceramic. But CNC machining is considered as the most widely used processing technologies for the ceramic parts. Due to the unique brittleness ceramic materials, the ceramic parts very easy to get chipping issue during the CNC milling machining. Therefor, CNC machining of machinable ceramic parts requires more professional technology and senior experience. At the same time, a CNC machining shop has the ability machining the machinable ceramic parts, which is also an aspect that reflects the processing strength of a CNC workshop.
Precautions for CNC machining machinable ceramics
Ceramic is very hard. The hardness of most industrial ceramics is very high, second only to diamond, which is the main reason why CNC machining ceramic parts is pretty difficult. The hardness of metal materials such as aluminum and steel is far lower than that of ceramic materials, and the rigidity of ordinary CNC machine tools is not strong enough, which will cause large vibration during the machining processing, especially for the main shaft. The excessive vibration may cause the tool jumping and tool broken, which shorten the service life of the tool directly, and will affect the machining accuracy also. Second, it will reduce spindle accuracy also. The shavings produced during the machining processing of machinable ceramics are in the form of powder, which may enter to the precision parts inside the machine, causing the precision parts damage, such as screw, guide rail, etc, etc., and reduce the accuracy of the machine.


Professional machinable ceramics CNC machines are required. The upper limit of the speed limit of the machinable ceramics CNC machine is higher than ordinary CNC machine. Generally, the maximum speed of ordinary CNC machine is 24000rpm, while the maximum speed of ceramic CNC can reach 36000rpm, which will well support the CNC machine machining such hard ceramics, and also enhances the overall stability of the machine to prevent machine vibration during machining. Machinable ceramics CNC machines request multiple protection to prevent the ceramic powder entering the CNC machine. It is necessary to clean the ceramics powder continuously during the machining. At the same time, need checking the cooling system also, as the cooling system is quite important for a high-speed CNC machine.
Professional cutting tools are required. The hardness of ceramic materials is generally high, which makes machining is difficult. For example, the hardness of alumina ceramics is between 80°-90, second only to diamond,and its wear resistance is also quite high, equivalent to 266 times that of manganese steel. It is 171.5 times that of chromium cast iron, and it is obviously not realistic to process it with the usual tungsten steel tool (the hardness of tungsten steel is between 45°-60°). As previous mentioned, the hardness of most of the ceramic materials is second only to diamond, so the machining of ceramics is inseparable from diamond. The cutting tools used for CNC machining machinable ceramic materials are preferably diamond-coated tools,which with the longest life among the cutting tools. Machining the machinable ceramics with diamond-coated tools which turns relatively easy. But if machining high quality machinable ceramics parts, which will request senior operator with plenty experience also.

Characteristics of Ceramics
Like other materials, ceramics have its unique characteristics also, such as ceramics have ultra-high strength, extremely high hardness, high elastic modulus, high temperature resistance, wear resistance, corrosion resistance, oxidation resistance, thermal shock resistance, etc, and widely used in various industries.
Advantage of ceramics
1:Electrical insulators: Ceramics are excellent electrical insulators. Therefore, it used in critical insulating wires and components.
2:Wear resistance: Ceramics can withstand very high temperatures and can withstand repeated and extreme thermal cycles and friction. This is why they are suitable for machine parts that require friction, such as bearings.
3. Corrosion resistant: They are chemically inert; ceramics do not react with other chemicals, so they protect sensitive instruments from contamination.
4. Superior Hardness and Strength: Ceramics are known for their incredible hardness and strength. They have very high strength-to-density ratios compared to most modern engineering alloys.
5. Color: Ceramic can keep the color for a longer time. If you paint ceramic material, the color will stick to the surface and not be washed off for years to come.
6. Easy to clean: The ceramic won’t retain the residue and smell of chemicals. They are stain resistant and very easy to clean.
Disadvantage of ceramics
1. Low tensile strength: lower than metal. Therefore, metals are usually preferred for parts requiring high tensile strength.
2. High brittleness: Compared to metals, ceramics are brittle and have very low ductility. Ceramic can crack when hit by a heavy object and can cause permanent damage.
3. It is difficult to control the dimensional tolerance of ceramics during machining.


Application of Ceramic Parts
The physical, chemical and unique properties of ceramics have provided many irreplaceable parts for different industries and achieved high achievements, which are durability and excellent hardness characteristics. The following is an introduction to the application examples of CNC machining ceramic parts in some industries.
l Medical applications. Health professionals can implant these special types of ceramics into the human body without any type of adverse reaction. Another area is dental applications, using teeth made of ceramics such as zirconia as a substitute for real teeth.
l Industrial application. Complex, high-precision ceramic parts have also found success in the industrial area. Parts made of ceramics have excellent wear resistance and can be used for a long time in some critical parts.
l Electronic applications. Ceramic parts with electrical insulation are a better choice for protection against electrical hazards against electrical hazards.
How to do CNC machining for the ceramic?
l Processing “bisque”. CNC machining ceramics is more difficult if the ceramic has already been sintered, as chips and large pieces fly around. Ceramic components can be processed most efficiently in a “green” compacted state or in pre-fired “bisque” form prior to final sintering. Generally, ceramic parts in pre-sintered state can be processed by milling, drilling, turning and other methods. In terms of cutting tools, titanium nitride (TiN) coated steel cutting tools, tungsten carbide cutting tools and polycrystalline diamond (PCD) cutting tools are used for the processing of pre-sintered ceramics.
l Grinding process. The most common machining process is grinding. Grinding ceramics is also best done with a liquid coolant to lubricate the area being ground. For sintered ceramics, resin-bonded grinding wheels are preferably used, in which synthetic or natural diamonds of varying particle sizes are pressed in polymeric resins in varying concentrations. With the help of grinding wheels, ceramic parts can be polished to a mirror finish.
l Reserve more machining allowance. The workpiece is CNC machined with more allowance and then ground with a grinder to create a precision ceramic part.
l Double-sided processing. Work from the ceramic side first, until about halfway, remove the piece, turn it over, and work the other side. This method has disadvantages, because there is no guarantee that there will be no errors in the position coordinates of the two clamps, so there will be misalignment when the two sides are connected, but the misalignment will not be exaggerated, and it is acceptable in most cases.
Tips for designing ceramic parts
When designing ceramic parts, you must consider certain inherent properties of ceramics. Keep in mind that ceramics are very brittle. Therefore, it is crucial to avoid focusing stress on specific points. Mastering the art of designing ceramic parts will aid in CNC machining:
l Convert tensile stress to compressive stress: This will allow the material to absorb more stress without breaking.
l Avoid long, sharp edges.
l Use circular designs instead of oval ones.
l Make sure the holes are not too close together.
l Avoid sudden cross-sectional changes.
l Avoid complex wall designs and shapes and use simple ones instead.
Are you confused about CNC machining ceramic parts ? Find a reliable professional CNC machining workshop that provides high-quality, on-demand rapid manufacturing services for custom part prototyping and product manufacturing. Get quality ceramic CNC machining services at the favorable price.
600K+ projects experience in prototyping & large-scale manufacturing up to now



