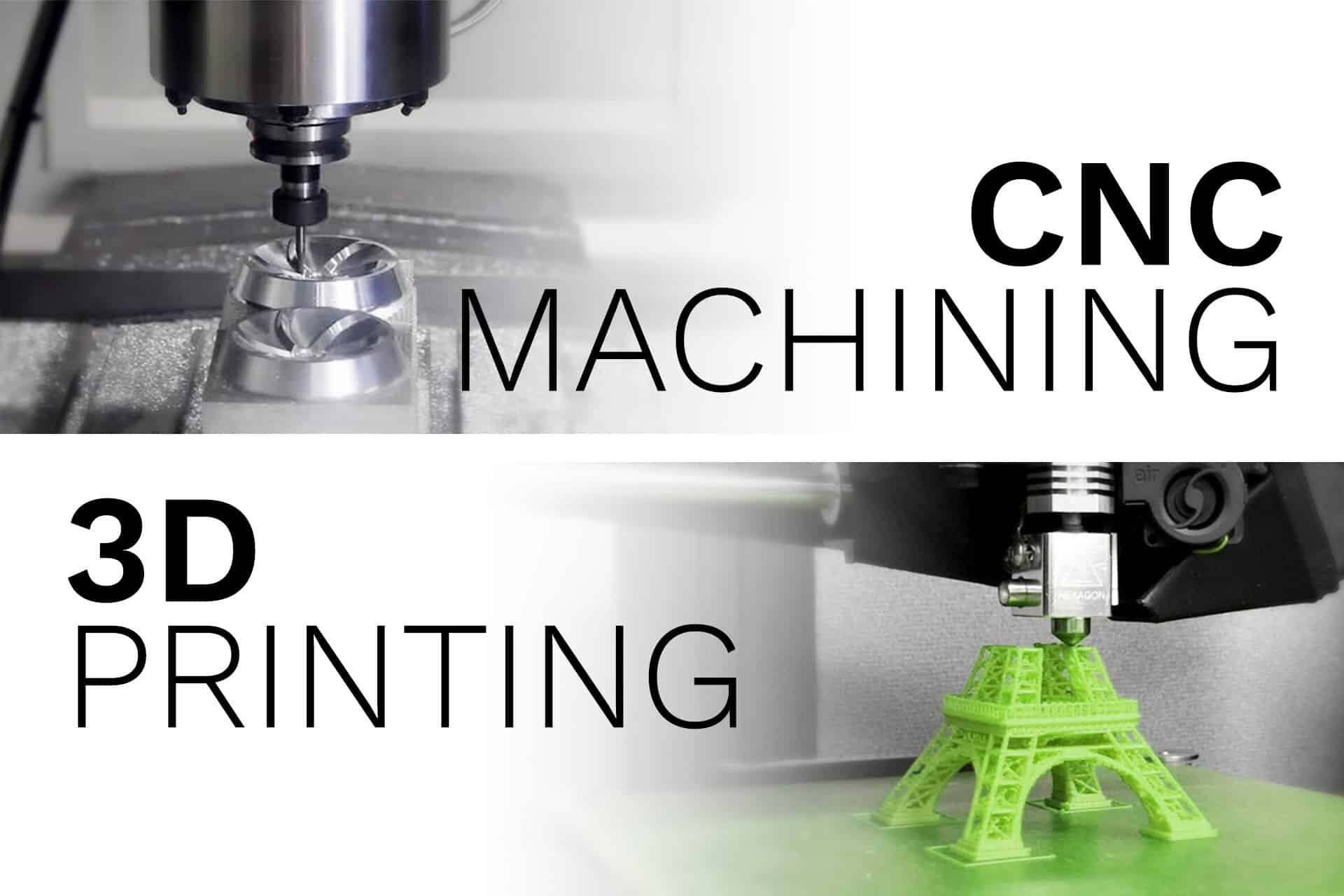
Rapid Prototyping & Rapid Manufacturing Expert
Specialize in CNC machining, 3D printing, urethane casting, rapid tooling, injection molding, metal casting, sheet metal and extrusion
CNC machining or 3D printing for your project?
About a decade ago, news of 3D printed firearms dominated the headlines in the manufacturing press, and 3D printing is still a hot topic today. With the development of science and technology, the technology of 3D printing has become more and more mature, and the plastic or metal parts manufactured are used in various fields, but they have not completely replaced the traditional manufacturing process, such as CNC machining, vacuum casting, injection molding, etc. So this creates confusion for designers. If I have a prototype or a small batch project, how do I choose the most suitable processing technology? In this post, I will share some technical guidelines on CNC machining and 3D printing to help you understand how the two differ in multiple dimensions such as accuracy, materials, cost, quality, efficiency and speed to determine your project Choose between CNC machining or 3D printing.
1,Subtractive and Additive Manufacturing
The main difference between the two is that CNC machining is subtractive manufacturing, while 3D printing is additive manufacturing.
CNC machining. As we all know, CNC machining is a subtractive manufacturing process that starts with a solid piece of material (often called a blank) and then uses a tool to cut and remove excess material to create a part. It is one of the most popular manufacturing methods for prototypes and small to high volume production parts, with repeatability, high dimensional precision, high surface finish, and compatibility with many materials, including wood, metal, and plastic.

3D printing.3D printing works in the opposite direction and is an additive manufacturing process. Although CAD and CAM software is also used to draw and create custom parts, it does not start with cutting material, but using plastic filament (FDM), resin (SLA/DLP), plastic or metal powder (SLS/DMLS/SLM), etc. Material is added and cured layer by layer until the final product is created. 3D printing has the ability to create complex geometries, high accuracy, fast turnaround and, in some cases, lower part cost.

Off topic. If you combine CNC machines and 3D printers and assemble them into a device that has both advantages, is it a no-brainer? Practitioners who do have this crazy idea, like the ZMorph 2.0 SX, which is both marketed as a 3-axis CNC milling machine and can also be used as a 3D printer. Additionally, several companies have recently completed successful Kickstarter campaigns using these combined machines, such as Mooz’s 3-in-1 3D printer. Currently, such a compatible machine is still in the exploratory stage.
2. Comparison of materials used.
Both CNC machining and 3D printing are compatible with a wide range of materials, including plastics and metals. 3D printing is more geared towards making plastic parts. This is currently changing, with manufacturers such as 3D Systems, Arcam, Desktop Metal and Markforged developing better and cheaper ways to 3D print metals.
CNC machining.The most commonly used plastics in CNC machining include ABS, Nylon (PA66), Polycarbonate (PC), Acrylic (PMMA), Polypropylene (PP), POM and PEEK, among others. Aluminum is the most widely used in CNC machining. According to Martin, an engineer at DDPROTOTYPE, an advanced prototype manufacturer in China, “70% of our material is aluminum, and the various parts we make are used in various industries.” Aluminium is a recyclable material with good properties and easy processing, other commonly used metals include stainless steel, magnesium alloys, zinc alloys, titanium alloys, copper, etc.
3D printing.Commonly used thermoplastics for 3D printing include ABS, PLA, nylon, ULTEM, and other photopolymers. 3D printers can also print parts for ceramics and even human implants. The metals most commonly used in 3D printing include aluminum, stainless steel, titanium, and Inconel. It is important to note that expensive 3D printed industrial machines (probably upwards of $100,000) are required. Some materials, such as superalloys or TPU (flexible materials) cannot be CNC machined, so manufacturing processes such as 3D printing or rapid tooling must be used. 3D printing cannot process wood because no material can simulate real wood.
Comparison of commonly used materials.
Manufacturing Process | Plastic | Metal |
CNC Machining | ABS, Nylon, Polycarbonate, PEEK、PC、PMMA、PP、POM PEEK, etc. | Aluminum, stainless steel, magnesium alloy, zinc alloy, titanium alloy, copper, etc. |
3D Printing | ABS, PLA, Nylon, ULTEM, ASA, TPU (flexible material), etc. | Aluminium, Stainless Steel, Titanium, Inconel, etc. |
Data source DDPROTOTYPE.
3. Accuracy and size of machined parts
According to the DDPROTOTYPE team, based on considerable experience, “for tolerances, CNC machining is superior to all 3D printing processes, even DMLS.” If your parts need to have tight tolerances, 3D printing may not be the best choice.
CNC machining. CNC machining can achieve very tight tolerances and better surface finishing, such as 0.005mm, and can be accurately machined for very large to very small parts. Due to the rounded nature of the tool, the inside corners always have a radius, but the outside surfaces may have very sharp edges.
3D printing. Different 3D printers offer different dimensional accuracy. The minimum wall thickness is limited by the size of the end execution (e.g. nozzle diameter in FDM or laser spot size in SLS). Because parts are built layer by layer, the final part may have layer lines, especially on curved parts. Industrial-grade machines can make parts with very good tolerances. If tight tolerances are required, machining is required during post-processing. This adds an extra step and is less efficient than CNC machining.
The table below lists tolerances, wall thicknesses and maximum part sizes for various technologies
Manufacturing Process | Tolerance | Min. Layer Thickness | Max. build volume |
CNC | ± 0.005 – 0.125 mm | cutting depth 0.01 mm | Up to 2000 x 800 x 1000 mm |
SLS | ± 0.3 mm | 0.1-1.5 mm | Up to 340 x 340 x 605 mm |
FDM | ± 0.3 mm | 0.2-0.8 mm | up to 914 x 610 x 914 mm |
MJF | ± 0.3 mm | 0.08 mm | up to 380 x 284 x 380 mm |
DMLS | ± 0.1 mm | 0.4mm | Up to 230 x 150 x 150 mm |
Data source DDPROTOTYPE.
As you can see from the icon, CNC machining can produce larger and more precision parts than common 3D printing techniques, such as FDM, SLS or MJF, etc. For parts in medical equipment, aerospace and other fields that require high precision, CNC machining is an ideal choice.
4. Speed
3D printing techniques such as MJF and FDM are known to excel at rapid manufacturing when manufacturing smaller quantities of parts, depending on part geometry and size. This is because once the 3D file is ready, choosing the orientation, fill and supports, and click the button, no additional setup is required, and it usually only takes several hours for the part to be finished. Post-processing depends on the machining process and the requirements of the 2D file.
CNC machining. Compared to 3D printing, the process of CNC machining is labor-intensive and requires more operators and settings. Skilled machinists select materials, machines, programming, tools and their rotational speeds, cutting paths, manually position fixtures, and even build custom fixtures in advance. This extends the processing time. In addition, post-processing techniques such as anodizing, electrophoresis, etc.can be finished here which may require more time.
Martin said, “At DDPROTOTYPE, if you choose ABS to machining 50pieces of medium-complex parts, the turnaround time with FDM technology is 1 working day on average, while for CNC machining, the turnaround time is 3 days. If you need to manufacture more than 500pieces of parts, the manufacturing efficiency of CNC machining comes into play, which is much faster than 3D printing because of the repeatability of CNC machining.” While some printers on the market have impressive print speeds, 3D printing generally uses more for prototyping rather than production. For some simple-structured parts, they can be machined in minutes on a CNC, but can take hours on a 3D printer.
5,Model Complexity
3D printing. 3D printing can process parts of any shape with very few geometric constraints on the part. Most 3D technologies such as FDM or SLM/DMLS require support structures that can be removed during post-processing. Any free-form plastic part can be easily fabricated using powder fusion processes such as SLS or Multi Jet Fusion (MJF), and no supports are required. The ability of 3D printing to manufacture highly complex geometries.
CNC machining. Of course, CNC can also machining fairly complex parts. Often, in order to make complex parts, it is necessary to re-flip and fix the position during the machining process, because even with 5-axis CNC machines, sometimes the tool cannot reach all surfaces of the component.
6. Cost
Simply discussing the price, the difference between CNC milling and 3D printing does not seem to lead to an accurate conclusion. This varies with various factors, such as material, quantity, difficulty of processing, etc.
No matter making 1 part or 100 parts, the cost of a single part made by 3D printing remains basically the same and is usually lower than CNC machining. For larger quantities of parts, such as 100+, CNC machining is more economical. According to Martin, one of our most common misconceptions is that CNC machining services are expensive. In fact, CNC prototyping can start as low as about $20 per part, with unit prices dropping dramatically as more quantities are manufactured.
7. Environmental protection
CNC machining starts with a blank and uses different tools to remove excess material. As a result, large quantities of fine dust and small pieces of material are left behind that cannot be recovered, requiring cleaning and disposal. In the 3D printing process, on the other hand, raw materials are fed into the printer to build the part layer by layer. This process requires only the use of raw materials, no mess or waste, so it is a more environmentally friendly manufacturing process.
8. Case studies
We study the difference between CNC machining and 3D printing through two examples, which seem to be more intuitive and understandable. These are 2 projects that DDPROTOTYPE has undertaken in 2021. We take plastic shell processing and metal bracket processing as examples.
Plastic housing prototype. Manufacturing plastic shell for electronics is a critical step before mass production. Fast manufacturing, low cost, and shortened development time are customer’s requirements. There are snaps, living hinges, interlocking joints and other fasteners in the electronic housing etc. These functions can all be achieved by CNC machining or 3D printing (FDM or SLS). High-precision and aesthetically pleasing plastic prototypes can be made with either CNC or SLS, but desktop-grade FDM has shorter processing times and lower costs. DDPROTOTYPE summarizes the comparison of each process, as shown in the table.
CNC machining | Desktop FDM | SLS | |
Cost | $$ | $ | $$ |
Commonly used material | ABS、Nylon | PLA、ABS、Nylon | Nylon |
Delivery | 5 days | 1.5 Days | 2Days |
Accuracy | ± 0.121mm | ± 0.485 mm | ± 0.287 mm |
Low-cost housing prototype made with FDM 3D Printing
Metal prototype of impeller.Metal impellers can operate under high loads and temperatures, and need to fit into precision shafts. The customer requires that the dimension of the impeller be more precise and the material quality be better.

CNC Machining | SLM/DMLS | Binder Jetting | |
Cost | $$ | $$$$ | $$$ |
Common Materials | Aluminium,Stainless Steel, Brass | Stainless Steel, Aluminum ,Titanium, Inconel Cobalt Chrome | Stainless Steel, Inconel Cobalt Chromium, Tungsten, Carbide |
Accuracy | ± 0.022 mm | ± 0.108 mm | ± 0.214 mm |
Mechanical Behavior | Very Good | Very Good | Good |
9. Quick Summary
There is no clear answer, no technology that is armed with all advantages, and both CNC machining and 3D printing has its unique advantages and disadvantages, which will depend on factors such as material, lead time, geometric complexity, precision, quantity, and budget. DDPROTOTYPE has carefully summed up a comparison chart for your reference.
CNC machining | 3D Printing | |
Mechanical properties | ⭐⭐⭐ | ⭐ |
Prototyping | ⭐ | ⭐⭐⭐ |
Cost | Cheaper for mid-large series | Cheaper for small series |
Turnaround time | ⭐ | ⭐⭐⭐ |
Polymer selection | ⭐⭐ | ⭐⭐⭐ |
Design complexity | ⭐⭐ | ⭐⭐⭐ |
Dimensional accuracy | ⭐⭐⭐ | ⭐ |
Details and resolution | ⭐⭐⭐ | ⭐⭐ |
Large part size | ⭐⭐⭐ | ⭐ |
Good-⭐ Better-⭐⭐ Best-⭐⭐⭐ |
10. Tips for choosing the right manufacturing method
Before choosing the right manufacturing process, please refer to the tips before make the final decision.
How does the quantity affect the choice of manufacturing methord?Choosing 3D printing is worth considering when you need small batches of parts (less than 50pieces). When the quantity reach to 100 to1000 pieces, then CNC machining would be better.
Are the partsmanufactured complex? For small quantity but highly complex custom parts, 3D printing is often cheaper and faster. CNC machining requires more operators and setup, and generally costs more than 3D printing.
What materials are required? Since CNC machining is a more mature technology, there is a wider range of compatible materials. But for metal superalloy materials that are very difficult to process, such as titanium or flexible TPU, it is more wise to choose 3D printing.