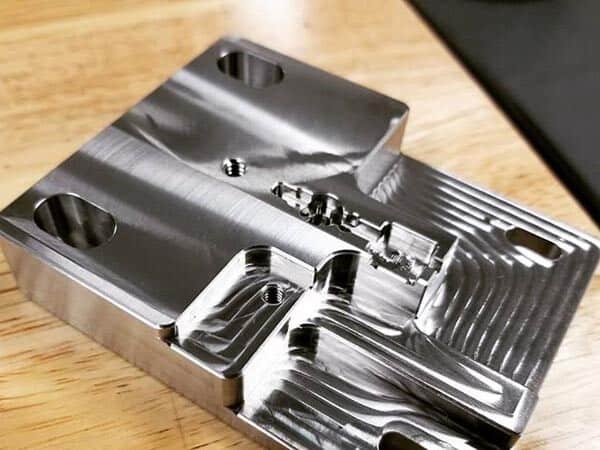
Rapid Prototyping & Rapid Manufacturing Expert
Specialize in CNC machining, 3D printing, urethane casting, rapid tooling, injection molding, metal casting, sheet metal and extrusion
How to reduce CNC machining cost
CNC machining is the most popular prototype machining technology, how to reduce CNC machining cost is a matter worthy of discussion. DDPROTOTYPE’s continuous and steady growth in CNC machining performance is due to its commitment to improvement, innovation, quality process and customer satisfaction. These are our basic tools to provide you (our customers) with the best quality products and services. We are always willing to expand our services to meet the needs of our customers, and we will add equipment to improve our capabilities when customers demand instructions.
People who have just come into contact with CNC machining may think that modern high automation will lead to fast, cheap and easy to produce parts. In fact, just running CNC machining to get the prototype parts of the blueprint will mean the soaring cost. The manufacturing cost of a single part can cost hundreds of dollars, which is really shocking.
However, there are many ways to reduce costs – in part design, some factors drive CNC machining costs down more than others. In the early stages of the development cycle, if you are aware of these factors, you can minimize CNC machininging costs.

Choose cheap and design intent materials
If you want to make prototype parts, of course you need to decide what materials to use to make them. There are many excellent materials to choose from. Each material has its unique performance, application and cost. The prices of different stock materials may vary greatly, but generally CNC machining costs depend on the overall availability and the difficulty of processing materials to produce a specific stock type (such as pipe or especially thick plate).
In order to give you a general idea of the range of costs that may be required to select materials, I conducted a quick search of the prices of different materials to find 6 “x 6” x 1 “plates. While ordinary plastics like ABS will cost you about $15, peek of the same size, known for its robustness and dimensional stability, costs as much as $220. Similarly, for metals, a 6061 aluminum plate costs about $23, a 304 stainless steel plate costs $137, and a precision ground 316 stainless steel plate costs as much as $282 each!

In general, you should only choose the cheapest materials that still meet the design requirements. Just doing functional prototypes? Try to stick with cheaper options like ABS and aluminum. On the other hand, if you are designing implantable medical devices, you may be forced to use more expensive materials, such as stainless steel, due to biocompatibility.
Reduce setup time
In addition to considering the manufacturing materials of parts, it is also important to consider how to make parts. Here, things start to get a little tricky because there is usually more than one way to process parts. We will start to discuss how to reduce the cost of CNC machining by studying how the design determines the preparation before machining.
Setup time consists of cam (Computer Aided Manufacturing) programming, machine setup and part fixing, and is often referred to as non recurring Engineering (NRE) cost. It usually accounts for a large part of CNC processing cost in the prototype stage and should be minimized.

At DDPROTOTYPE, all milling parts are produced with 3-axis, 4-axis or 5-axis CNC machine tools. Suppose your parts will be made on a 3-axis machine because of their versatility. With this machine type, features can only be machined on one side at a time, except for the part profile.
It is assumed that the part will be machined with 8 sides or more. In CNC machining, because there are at least 8 faces, prisms or strips or other shapes, it needs to be fixed on one side by vice or other clamps for machining. In this way, it needs to be turned 8 times, adding human factors, which is likely to affect the tolerance. At the same time, each setting requires its own CAM program and fixture steps. The processed prototype parts are likely to be scrapped, which will greatly increase the cost of CNC processing. It is advisable to reduce the number of machined surfaces as much as possible (ideally 1 or 2).

Avoid special clamps
Sometimes, your parts may have the function of requiring non-standard clamps, which is another reason for the increased cost. These fixture types are different and can be discussed separately, but here are two common fixtures and features you can avoid if you are not willing to add additional costs.
Soft jaws – parts with complex or organic geometry cannot always be secured reliably in a standard vise, so a set of jaws with geometry similar to the surface of the part is machined for better grip.
Sine bars – parts with features that are not parallel to or perpendicular to the surface of the blank, such as holes with a 20 degree angle, will need to be set using this device to allow the workpiece to be fixed at a custom angle.

Increase quantity to reduce unit cost
CNC machining the same parts requires the same processing steps. If you need more than one identical part, the price of machining only one prototype part will be greatly reduced. This means that if you are making multiple identical parts, you can reuse the same CAM programming and jigs, or you can cut multiple parts at once from the same stock. I recommend making more than one part per part, which can reduce the unit cost, but don’t make too many unnecessary parts.
Reduce machining time
The last aspect of cost savings is the actual time to process parts. In most cases, it depends on two things you have considered: material and part design.
1. Impact of material type
If your functional requirements give you material flexibility, choosing the most Machinable tool should save money. Generally, due to the risk of tool damage, harder materials require longer processing time, but there are exceptions to this rule. Remember the following tips:
Cutting plastic too fast can cause the tool to rub against the material instead of cutting it, leaving a poor surface finish. Aluminum, though harder than plastics such as ABS, is actually slightly easier to process, although the cost of the material may be a compromise.
As far as steel is concerned, the higher the carbon content of the alloy, the harder it will be and the more difficult it will be to process it. If possible, try a low carbon version of the alloy (for example, 316L higher than regular 316). 303 stainless steel is the fastest material.
Metals containing magnesium or zinc, such as brass, are highly Machinable.
2. Impact of part design
Similarly, your functional requirements may drive part design, but keep in mind the following considerations:
Tolerance – smaller tolerance = higher cost. Ddprototype makes all its CNC suppliers comply with ISO 2768 media standard, which is a reasonable standard for prototype design.
Hole size and depth – deep holes are processed slowly and are easy to cause tool damage. Avoid as much as possible.
Internal radius – the smaller the radius, the smaller the end mill is required to create it. The smaller the end mill, the slower the machining speed.
Cut depth – like holes, extra deep pockets take longer to process and may require special ordered tools. Try not to exceed 10 times the minimum inside radius (5 times the tool diameter).
Wall thickness – thin walls require extra care. Ddprototype recommends a minimum absolute value of 1.0mm for plastic and 0.5mm for metal.
Undercut – some features, such as O-ring grooves or keyways, can (and often must) be machined with tools designed for undercutting. In addition, it’s usually not a good idea to design parts with suspended materials.
Main points
There are many considerations that can help minimize the cost of CNC machining. Remember that everyone can be a challenge, especially if you are not familiar with product design and development. To speed up planning as you move into this phase, keep in mind three overall cost drivers that you should minimize:
1.Material cost, including inventory size and material value.
2.Number and complexity of fixtures.
3.Machining time to eliminate difficult part features and geometry as much as possible.

Keep these techniques in mind early in the design process to maximize the value of these cost saving methods.DDPROTOTYPE is an innovative CNC machining manufacturer, mainly serving high-tech OEMs (such as defense, semiconductor, automobile, medical instrument and robot industries). They have won a good reputation for their consistent high quality and reliability. Both the customer’s engineering and purchasing departments have found that ddprototype is the main supplier they can entrust to their most important projects.

DDPROTOTYPE aims to provide customers with the best prototype parts at competitive prices. Complete this task within the time frame to meet the delivery requirements of customers; stand out in the highly competitive industry through our commitment to excellent quality and our personal and attentive contact with customers.