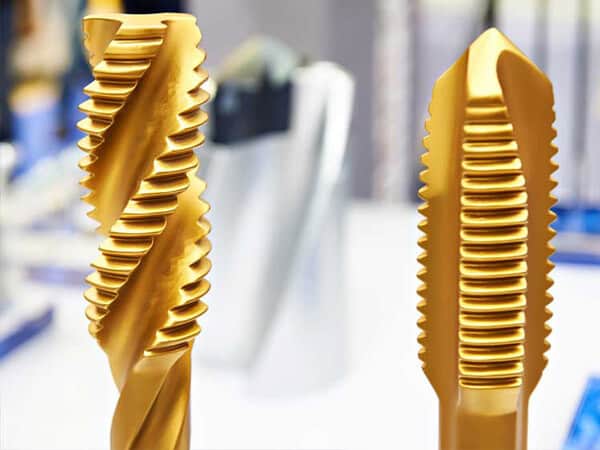
Rapid Prototyping & Rapid Manufacturing Expert
Specialize in CNC machining, 3D printing, urethane casting, rapid tooling, injection molding, metal casting, sheet metal and extrusion
Drilling and Tapping
Do you have any ideas on how to better design the drilling and tapping on the prototype?CNC machinist of DDPROTOTYPE has a lot of machining experience. He should sort out some guidelines and answer all questions about how to add threaded holes to parts.
What is the difference between drilling and tapping?
Drilling and tapping are two different actions. Drilling is the use of a drill to create a smooth hole in the material. Tapping is the action of producing a thread on the side of a hole.Various types of taps to match almost all available screw types, including metric and standard sizes. Select tap information including thread number, diameter, pitch and coarse fine thread. Tap guides are essential for creating straight and usable taps. When tapping on a machine such as a CNC milling machine or lathe, the tap will be automatically centered and straight. Please pay attention to the tap alignment when performing manually, because the human eye is not as accurate as the perfect 90 degree tap guide.

Use oil
Oil must be added when drilling and tapping. It prevents overheating, helps to remove chips from the bit, helps to cut, and prevents the bit from being squeezed.
Center drill
To create a drill and tap hole first, you need to use a center drill. This provides a center of alignment for larger bits because most bits are not fully centered when installed in the bit chuck. This ensures that the larger bit is drilled in the correct position and does not cross the part.

Pecking holes
Whether drilling or tapping, pecking helps ensure that the bit does not overheat or break. Pecking is a way to drill into a part, then back off to remove chips and cool the part. The usual way to do this is to rotate the handle for one full turn and then half a turn. Remove as much chips as possible and add oil to the surface and bit / tap each time the bit / tap is pulled out.
Power
Be careful not to apply too much downward force. Use the rotating force and tap pecking method to prevent the tap from breaking.
Rule of Thumb
As for the ratio of tapping bit to large diameter of thread, there are some rules of experience with strong prediction ability for standard V thread (ISO V thread and UTS V thread):
The coarse diameter of a good bit is 85% of the large diameter (± 2 PP)
The high quality tap drill should be 90% (± 2PP) of the large diameter.

For metric V threads, the concept of major negative pitch (i.e., the major diameter or maximum diameter of the desired screw in millimeters minus the screw pitch in millimeters per millimeter of the screw) produces a good tap drill diameter.
The main pitch reduction technology is also applicable to inch based threads, but you must first convert the thread per inch (TPI) ratio to a decimal calculated tone. For example, a screw with 1 / 20 in one pitch (20 threads per inch) has a pitch of 0.050 and a pitch of 1 / 13 in pitch (13 lines per inch) has a pitch of 0.077. Your results will only land near the tap size (not directly on one).

For these two rules of thumb (85% / 90% and major negative pitches), yield tap hole size is not necessarily the only possibility, but it is a good choice for general use.
85% and 90% of the rules work best in the range 1 / 4-1 (6.4-25.4mm) when size is most important in many shop floors. Some dimensions outside this range have different ratios.
How do I add threads to my 3D parts?
The short answer is that you don’t have to. In most 3D CAD applications, adding a thread is a time-consuming task and does not require adding a 3D tap to the part. If you want to add threads to some holes in a part, follow these steps
Make sure that the hole matches the pilot drill size required by the tap.
Please refer to which threaded holes and thread types and pitches in your ordering instructions or references.
If you need to customize thread depth, add any comments.

Can my parts be made of custom thread?
Usually, but it depends on the diameter. Tapping holes can be made with traditional taps, which are tools for standard thread sizes, or with a thread cutter, which is a small disc for cutting threads through the XYZ motion of a CNC controller. The diameter of the cutter is limited to more than 1 / 2 inch. Custom lines can be made with a tangent knife, but this may incur additional costs.