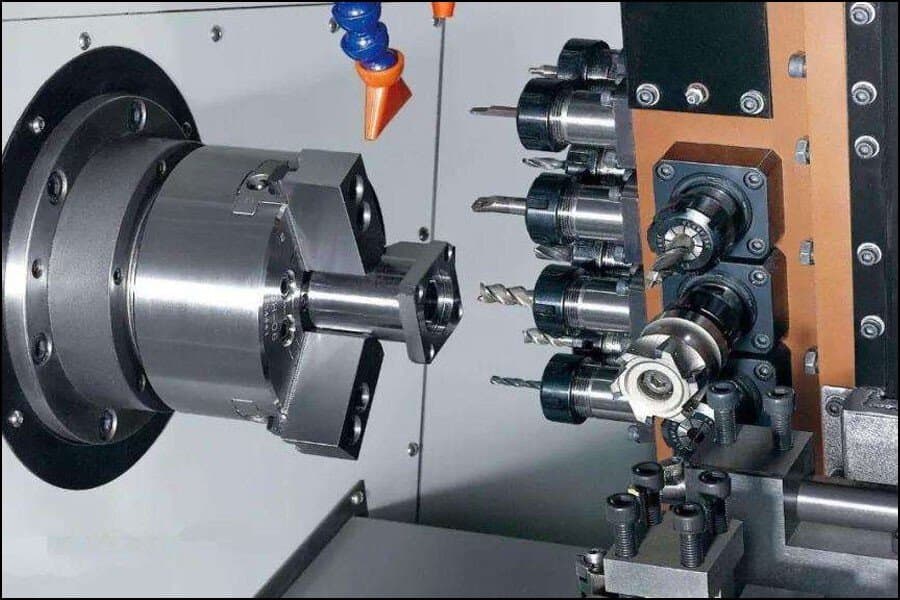
ラピッド プロトタイピング & ラピッド マニュファクチャリング エキスパート
CNC 機械加工、3D 印刷、ウレタン鋳造、ラピッド ツーリング、射出成形、金属鋳造、板金、押出成形を専門としています
旋削とフライスを組み合わせた加工についてお話します
数値制御技術、コンピュータ技術、工作機械技術、加工技術の継続的な発展により、従来の加工概念では、加工速度、効率、精度に対する人々の要求を満たすことができなくなりました。 そこで誕生したのが複合加工技術です。 一般的に複合加工とは、異なる工程や異なる加工方法をXNUMX台の加工装置で完結できる加工技術の総称を指します。
現在の複合加工技術は主に XNUMX つの異なるタイプに現れています。XNUMX つはエネルギーまたは運動モードに基づく異なる加工方法の複合です。 もう XNUMX つはプロセス集中の原則に基づいており、主に機械加工技術に焦点を当てています。 複合ターンミリング複合加工は、この分野で近年最も急速に成長している加工方法の XNUMX つです。
現在の航空製品部品は、多品種・少量生産、複雑な工程が特徴で、全体的に薄肉構造や難削材が多用されています。 したがって、製造プロセスでは、長い製造サイクル、大量の材料除去、低い加工効率、および加工変形が一般的です。 ボトルネックを真剣に待っています。

航空複合製品の加工効率と加工精度を向上させるため、職人たちはより効率的で正確な加工方法を模索してきました。 旋削フライス複合加工装置の出現は、航空部品の加工精度と効率を向上させるための効果的なソリューションを提供します。
従来の数値制御処理技術と比較して、複合処理の優れた利点は主に以下の点に現れます。
(a) 製品の製造工程チェーンを短縮し、生産効率を向上させます。
ターンミリング複合加工では、XNUMX 回のクランプで加工手順のすべてまたはほとんどを完了できるため、製品製造プロセスチェーンが大幅に短縮されます。 これにより、クランプ変更に伴う生産補助時間が短縮されるとともに、治具の製造サイクルや待ち時間が短縮され、生産効率を大幅に向上させることができる。

(b) クランプ回数を削減し、加工精度を向上させます。
カードの取り付け回数が減ることで、位置決めデータの変換によって生じる誤差の蓄積が回避されます。 同時に、現在の旋削フライス複合加工装置のほとんどはオンライン検出機能を備えており、製造プロセスの重要なデータを現場で検出および精密管理することができ、それによって製品の加工精度を向上させることができます。

(c) 床面積を削減し、生産コストを削減します。
ターニング・ミーリング複合加工装置の単価は比較的高いですが、製造プロセスチェーンの短縮と製品に必要な設備の削減、治具の数、作業場の床面積および設備の削減により、メンテナンスコスト、固定資産全体の投資、生産運営および管理コストを効果的に削減できます。

複合加工のキーテクノロジー
複合加工は従来の単体加工とは比較にならない利点を持っていますが、航空機製造分野におけるターニング・ミーリング複合加工の稼働率は十分に活用されていないのが現状です。 その主な理由は、航空機製造分野における旋削・ミーリング複合加工の適用時期がまだ比較的短く、構造特性に適した旋削・ミーリング複合加工技術、数値制御プログラミング技術、後処理およびシミュレーション技術がまだ確立されていないことである。航空部品の一部はまだ探索段階にあります。
ターニングミーリング複合加工装置の性能を最大限に発揮し、製品の加工効率と精度を向上させるためには、上記の重要な基礎を総合的に克服・解決し、統合的なアプリケーションを実現する必要があります。
1. CNC旋削・フライス複合加工技術
従来の加工機とは異なり、ターンミーリング複合マシニングセンタは実質的に生産ラインに相当します。 部品の加工特性やターンミーリング複合加工の加工特性に応じて、適切な加工ルート、クランプ方法をどのように策定し、適切な工具を選択するかが、効率的な精密加工を実現する鍵となります。
複合加工の最大の特徴は工程の集中化です。 したがって、科学的かつ合理的なプロセス ルートが、旋削およびフライス複合加工の効率と精度を向上させる重要な要素となります。
S192Fに乗ります CNCフライス盤 例として、スイスのBaomei Companyの旋削複合マシニングセンターがあります。 この工作機械は、XNUMX軸フライス加工、旋削加工、ボーリング加工、穴あけ加工、ソーイング、自動送りなどの機能を備えています。

強力な前向き高速補間機能などを備え、特にシャフトや回転部品などの高速精密加工に最適です。 航空機用インペラの加工において、このマシニングセンタは優れた利点を持っています。
バーをインペラブランクとして使用する場合、従来のインペラ加工ルートでは、まず CNC 旋盤を使用してインペラの外形を旋削し、次にベンチマークを完成させます。 これに基づいて、5 軸 CNC マシニング センターを使用して、溝加工、荒加工、中仕上げ加工、およびプロファイルとハブの仕上げ加工を行います。 最後に、XNUMX 軸マシニング センターまたはボール盤で穴加工が行われます。
しかし、 S192F ミーリング&ターニングマシニングセンタは、一度のクランプで上記工程の全ての加工が完了するだけでなく、バー材の場合はソーイング機能や自動送り機能により羽根車の一括加工も実現します。 プロセス全体は手動介入なしで処理できます。
すべて自動的に行われます。 主軸でバー材をクランプ→羽根車外形荒加工→外形仕上げ→XNUMX軸フライス加工と溝加工→ランナー荒加工→半加工という工程ルートの設定が可能です。・ランナーの仕上げ→ランナーの仕上げ→穴あけ→バックスピンドルのクランプ→羽根車底面の旋削→穴あけ。

インペラの加工プロセス全体が XNUMX 回のクランプで完了し、加工効率と精度が大幅に向上することがわかります。
ダブルタレットを備えたCNCターニングフライスマシニングセンターの場合、ダブルタレットを備えた装置はデュアルチャネル制御システムを備えており、上部と下部のタレットを個別に制御でき、コード内の同期ステートメントを通じて同期加工を実現できます。
設備の加工能力を最大限に発揮するため、加工条件が許せばダブルツールホルダの同期動作により部品の多工程同時動作を実現します。
上下の工具ホルダを同期してセットすることにより、内穴の荒加工を形状を荒加工しながら完了させることができ、加工効率がさらに向上します。 上下のツールホルダーが同期して動くことで一連の穴加工が完了し、加工効率が向上するだけでなく、加工穴の軸力を相殺してワークの変形の影響を軽減します。 この機能を実現するには、プロセス設計の初期段階でプロセス計画を体系的かつ綿密に調査し、プロセスルートの直列順序と並列順序を決定し、上記の機能を合理的な組み合わせで実現する必要があります。加工プログラムの説明。
2. 旋削・フライス複合加工のためのCNCプログラミング技術
ターンミーリング複合加工技術の開発により、NC プログラミング技術に対する要求も高まります。これは、実際の生産およびアプリケーションにおけるターンミーリング複合加工装置を制限するボトルネックでもあります。
実際の生産におけるターンミーリング複合加工の適用時間は短いため、専門的な複合加工ソリューションがない場合、通常は汎用の CAM ソフトウェアを使用して加工プログラムの一部を計画し、その後職人が手動で複合加工を統合します。複合加工工作機械の加工プログラムの要件を満たすプログラム。

このソリューションは職人に非常に高い要求を課します。 従来の NC プログラミング技術と比較して、旋削およびフライス複合加工のプログラミングの難しさは主に次の側面に反映されます。
(a) 工芸品にはたくさんの種類があります。 職人にとっては、CNC 旋削、多軸フライス加工、穴あけなどのさまざまな加工方法のプログラミング方法を習得できるだけでなく、工程間の接続や工具の前進および後退の方法を正確に定義する必要があります。 したがって、NCプログラミングを行う際には、次の工程のプログラミングや進み具合や送り量の設定を容易にするために、現在の加工が完了した後の加工モデルや取り代の配分を直感的に理解する必要があります。撤退ツール。

(b) プログラミング工程における直列と並列の順序は、工程経路に応じて厳密に決定する必要があります。 ターンミーリング複合マシニングセンターで加工される場合、多くの部品は原材料から完成品まで処理されるため、加工プログラムの結果はプロセスルートと一致している必要があります。 同時に、NC 加工プログラミングのプロセスでは、多チャンネルの並列加工も総合的に考慮する必要があります。 効率的な複合加工を実現するには、プロセス、プログラミング、シミュレーションの統合プロセス ソリューションを開発する必要があることがわかります。

(c) 現在の一般的な CAM ソフトウェアは、ターンミーリング複合加工の一部の機能をサポートしていません。 従来の単一装置の加工と比較して、旋削とフライス複合加工の工作機械の動作と加工機能ははるかに複雑です。 現在の汎用 CAM ソフトウェアは、オンライン測定、ソーイング、自動送り、心押し台制御などの高度な機能のプログラミングを完全にサポートするには十分ではありません。そのため、一般的な CAM ソフトウェアでコンパイルされたプログラムには依然として多くのマニュアルが必要です。自動旋削およびフライス複合加工に適用する前に、対話型の方法を使用できます。
(d) 加工手順の統合。 現在、一般的なCAMソフトでコンパイルされたNCプログラムはそれぞれ独立しています。 旋削やフライス加工などの複雑な自動完全加工を実現するには、これら独立した加工プログラムを統合して統合する必要があります。 この統合は、部品のプロセス ルートに基づいて行う必要があります。まず、どのプログラムが並列であるかを決定し、次にさまざまなプロセス方法の加工シーケンスを決定し、正確な工具交換、クランプ交換、データム変換、工具の前進と後退の指示を与える必要があります。 。

旋削とフライスを組み合わせた加工用の NC プログラムをコンパイルすることは非常に困難であり、現在の汎用 CAM ソフトウェアには旋削とフライスを組み合わせた加工において依然として多くの欠陥と欠陥があることがわかります。 これらの欠点を補うためには、既存の汎用CAD/CAMソフトをベースに、製品技術や複合加工機に適した専用のプログラミングシステムを開発することがより現実的な解決策となります。 一方で、ソフトウェア購入への繰り返しの投資が削減され、同時に、不均一なプログラミング プラットフォームによって引き起こされる再利用できないプロセス知識や複雑な人員配置などの欠陥を回避できます。
3. ターンミーリング複合加工の後加工技術
NC プログラミング技術に対応して、複雑な加工方法と多くの可動部品により、ターンミーリング複合加工は、現在の加工後のソフトウェアと技術に対するより高い要求を押し上げます。 従来の CNC 装置と比較して、後加工の難しさは主に次の点に反映されます。
(a)異なる工程間の接続動作には厳しい精度が要求されます。 旋盤フライス複合装置では多種多様な加工技術が実行されるため、正確性と安全性を確保するために、現在のプロセスが完了した後、加工方法、工具、可動部品の自動切り替えをタイムリーかつ正確に完了する必要があります。加工工程の様子。

この目標を達成するには、合理的な工具の前進・後退方法や自動工具交換、クーラントのオン・オフのタイミングを設定する必要がありますが、さらに重要なのは位置を設定することです。現在のプロセスを加工する際の他の非可動部品の影響。 この方法によってのみ、工具交換および加工中の工作機械の可動部分と非可動部分との衝突を回避することができ、加工プロセスの安全性と安定性を確保することができます。
(b)加工順序やNCプログラムを自動判断する必要がある。 複合加工のプロセスルートは比較的長いため、完成後の NC コードを手動で整理および統合することに依存すると、非効率であるだけでなく、エラーが発生しやすくなります。 理想的なソリューションは、後加工中に工具位置ファイルに含まれる加工順序と加工方法を自動的に決定し、後加工完了後に NC コードに自動的に維持できることです。

このため、NCプログラミング完了後の工具位置ファイル情報には、対応する加工方法や工具位置情報だけでなく、対応する加工順序、使用する工具の種類や番号も含める必要があります。機械加工後のプロセスで加工することができます。 処理順序、処理方法、ツールの自動決定を実現します。
(c) さまざまな加工方法による後加工技術。 ターンミーリング複合加工の後加工プログラムには、多軸 CNC ミーリング、旋削、穴あけの後加工だけでなく、ソーイング、自動送り、心押し台制御、プログラム サイクル コールの機能も必要です。 フライス複合加工の加工後アルゴリズムには、基本的に既存のあらゆるタイプの CNC 加工プロセスの後加工方法が含まれており、異なる加工方法間のシームレスな統合とモーション接続も実現できなければなりません。

(c)制御システムの先進機能を最大限に活用する。 現在、旋削およびフライス加工複合マシニング センターに使用される CNC システムは、Baomei S31FT で使用される FANUC 192i システムや WFL 840 で使用される SINUMERIK150D システムなど、すべて非常に高度な制御システムです。
これらの高度な制御システムのほとんどは、自動送りの最適化、工具ベクトルのスムージング、超前向き、高速・高精度の補間などの高度な機能を備えています。 したがって、旋削・ミーリング複合加工機の性能を最大限に発揮するには、これらの先進的なCNCシステムの機能を、加工後の段階で完成する加工コードの適切な位置に反映させる必要があります。
(d) 加工および非切削機能の呼び出し。 複合加工工作機械は、旋削、フライス加工、穴あけ、ボーリングなどの切削機能に加え、自動送り、アンロード、主軸ドッキング、心押し台制御など、各工程間の移行に必要な非切削機能も備えています。 。

加工後においては、これらの関数をプログラムの共通モジュールとして呼び出す必要があり、呼び出す順番やタイミングは加工経路に応じて決定する必要があります。 これらの機能は、現在の加工後ソフトウェアでは利用できません。
4. 旋削・フライス複合加工のシミュレーション技術
ターンミーリング複合加工には多くの可動部品と複雑な機能があるため、プログラミング完了後の加工シミュレーションは特に重要です。我が国の航空製造工場のターンミーリング複合加工は実際に導入されているという事実により、短期間の生産では、現時点では成熟したシミュレーション アプリケーション技術が存在しません。そのため、ほとんどのメーカーは試し切り加工を通じてプログラムを検証し、最適化します。これは、長いプロセス準備サイクルと開発につながります。 高いリスクと加工コスト。
旋削とミーリングの複合加工の応用レベルとプログラミング効率を向上させるためには、シミュレーション技術の適用を強力に推進する必要があります。現在、旋削とミーリングの複合加工のシミュレーションに使用されるソフトウェアには、主に TopSolid、Gibbs、などがありますが、これらのソフトウェアは一般に高価であり、我が国の航空製造分野では導入されることはほとんどありません。実際、旋削とフライスを組み合わせた加工のシミュレーションは、現在の汎用CNC加工シミュレーションソフトウェアの助けを借りて実現することもできます( Vericut、NCSimulなど)、ターニング・ミーリング複合加工機の構造、動作特性、特殊機能やCNCシステムに合わせて、カスタマイズやマクロ機能開発により、加工工程の動作シミュレーションを実現します。

一般的な CNC 加工シミュレーション ソフトウェアを使用してターン ミーリング複合加工のシミュレーションを実現するには、まずシミュレーション システム内で比較的実際の工作機械環境を構築する必要があり、相対運動関係と幾何学的位置関係の確立に重点が置かれます。工作機械の可動部分の間。
これに基づいて、機械加工プロセスで使用される工具ライブラリと対応する工具番号を確立します。 次に、工作機械装置の数値制御システムと数値制御プログラムの加工ベンチマークを構築し、完成後のNCコードをシミュレーションシステムにロードすることで、加工プロセスのシミュレーション作業を実行できます。 従来のNC加工とは異なり、一部の機能(多チャンネル加工、心押し台制御など)はマクロ機能の開発とカスタマイズによって完成させる必要があります。

旋削・フライス複合加工技術の応用展望と開発提案
近年、旋削およびフライス加工の複合マシニングセンターが、我が国の航空機、航空エンジンおよび付属品工場、その他の航空メーカーに導入されています。 設備の種類は主にオーストリアのWFL社のターンミーリングコンパウンドシリーズ製品とスイスのBaomei社のミーリングターニング複合マシニングセンターに焦点を当てています。
しかし、実用化までの期間が短いため、製品のプロセス特性や装置のプロセス特性に適合した成熟した加工技術、プログラミング方法、加工後の技術的手段が一般に不足しています。 したがって、現在導入されているターンミーリング複合加工機は基本的に稼働レベルが比較的低い状況にあります。
航空製品の製造プロセスで直面する主な問題は、長い加工ルート、複雑なプロセス、低い加工効率、深刻な加工変形、および高い加工コストにあります。 ターンミリング複合加工は、航空機製造とエンジン製造の両方に非常に幅広い用途があります。 開発スペース。

例えば、航空機の機体フレーム全体のフライス加工では、通常、ブランキング/ブランク準備、データム加工、内部形状荒加工、形状荒加工、仕上げデータム、中仕上げ、内部形状仕上げ、中仕上げを経る必要があります。
仕上げや形状の仕上げ、穴加工、フィッターのドレッシング、検査など数十の工程を複数回の反転とクランプで完了できます。
現在、航空エンジン分野のブリスク加工全般にも、旋削・フライス加工、フライス加工、研磨、表面処理・強化、探傷など数十工程を経て初めて完成する一体鍛造ブランクが使用されています。
これらの部品の製造サイクルは長いことが多く、加工時間は通常数百時間に達し、加工プロセスではさまざまな種類の CNC 工作機械や多数の治具、工具、測定ツールなどが必要になります。 さらに、クランプの交換を繰り返すと、部品の製造工程での待ち時間が長くなり、生産サイクルに影響を与えるだけでなく、クランプ誤差が蓄積され、部品の寸法精度や加工結果に影響を及ぼします。 。

旋削加工とフライス加工を組み合わせた加工は、上記の典型的な航空部品のプロセスのすべてまたはほとんどを XNUMX 回のクランプで実現できるため、複雑な航空部品を効率的かつ精密に加工するための新しい方法を提供します。
そのアプリケーションの利点は主に次の側面に反映されます。
(a)クランプ回数が大幅に削減され、加工効率が向上し、工作機械やクランプ方法の変更による誤差も解消されます。
(b) プロセスがより集中するため、加工プロセスチェーンが大幅に短縮され、待ち時間と機械の非稼働時間が削減されます。
(c)位置決め状態を変えないことを前提に、旋削、フライス、穴あけ等の多様な加工方法の加工工程を実現し、治具の数を削減し、寸法精度の安定性を確保します。
(d) 現在の旋削・ミーリング複合加工の多くはオンライン計測機能を備えており、工程内や工程間での加工結果をその場で計測することができ、加工工程全体の精度管理を実現します。 旋削フライス複合加工装置のこれらの利点は、現在の航空複合部品の製造プロセスの欠点を効果的に補い、製品の加工精度と効率を大幅に向上させることができることがわかります。
先進複合加工機の加工効率を最大限に発揮し、航空製品の製造効率と品質をさらに向上させるためには、以下のような取り組みが急務となっております。
(a) 航空製品部品の技術的特性と組み合わせて、加工ルートの策定、クランプ方法、工具、冷却および切断パラメータの合理的な選択を含む、これに適合する複合加工技術について徹底的な研究を行う。 、など。
(b) 複合加工装置の動作構造と製品のプロセス特性に応じて、対応する CNC プログラミング、ポスト加工、切削シミュレーション、その他のシステムを開発およびカスタマイズして、プロセス-プログラミング-ポストシミュレーションの統合ソリューションを形成し、コスト削減を実現します。職人の複合加工要件。
(c) フォームプロセスの仕様。 シミュレーション、試し切り、実生産で蓄積したプロセス経験を組み合わせて、ターンミーリング複合加工に適したプロセス仕様を確立し、その後の他の部品の加工をガイドします。
(d) 人材の育成に留意する。 現在の機械加工分野の最先端技術を代表する複合加工機。 プロセスの準備と運用保守の両方が従来の装置に比べて複雑になります。 設備の健全かつ効率的な運用を実現するには、ハイレベルの研究開発チームが鍵となります。
まとめ
現在の複合加工機は、加工範囲の拡大、高効率化、大規模化、モジュール化の方向で発展しています。 航空製品製造の分野は、常に高度な製造技術が役割を果たす重要な段階です。
航空製品のアップグレードの加速に伴い、プロセスが分散した機械加工装置は、プロセスが集中化された柔軟な自動化装置に徐々に置き換えられます。 より広範な開発とアプリケーションのスペース。