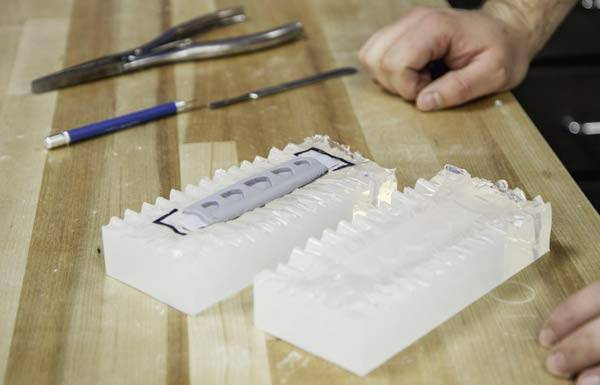
Experte für Rapid Prototyping und Rapid Manufacturing
Spezialisiert auf CNC-Bearbeitung, 3D-Druck, Urethanguss, Rapid Tooling, Spritzguss, Metallguss, Blech und Extrusion
Alles, was Sie über das Vakuumgießen wissen sollten
Vakuumgießen ist einer der wichtigsten Prozesse zur Herstellung von Prototypen. Es hat die Vorteile niedriger Kosten und stabiler Produktqualität. Es eignet sich sehr gut für schnelle technische Tests (Schnelltests von Projekten), die Überprüfung von Designkonzepten und die physische Anzeige (Anzeige der physischen Struktur des Produkts). Vor der Entwicklung von einem Konzept oder einer Idee zur ausgereiften Massenproduktion müssen Designer kontinuierlich Probleme entdecken und die Produktplanung verbessern. Viele industrielle Kunststoffteile wie Autoteile, Roboter, medizinische Geräte und 3C-Produkte verwenden normalerweise das Spritzgussverfahren. Millionen von Einheiten werden produziert, aber die Kosten für das Öffnen der Form sind sehr hoch und die Zeit für die Entwicklung der Form ist relativ lang (und der Design- und Produktionszyklus der Form ist lang). Was es für Designer schwieriger macht, ist, dass ein kleiner Fehler im Plan zu einer großen Verschwendung führt (die Kosten für die Änderung der Form sind ziemlich hoch). Sie müssen wissen, dass ein Satz Stahlformen normalerweise 10,000 oder sogar Zehntausende von Dollar kostet und die Zeitkosten nicht kompensiert werden können. Daher ist es ein wesentlicher Schritt, kleine Chargen von Kunststoffteilen herzustellen, um das Design zu überprüfen, z. B. 20-500 Stück. Derzeit ist Vakuumgießen das bevorzugte Verarbeitungsverfahren.

Was ist Vakuumgießen?
Beim Vakuumgießen, auch bekannt als Silikonform, wird die hergestellte Silikonform verwendet, um Kunststoffteile nachzubilden. Das gegossene Polyurethanmaterial wird entschäumt, gerührt, vorgeheizt und unter Vakuumbedingungen gegossen, und der sekundäre Aushärtungsformprozess wird in einem Thermostat bei 60°C–80°C für 2–3 Stunden durchgeführt. Die Nachbildung aus Silikonverbundform kann die Festigkeit und Härte von ABS und anderen Materialien erreichen und kann je nach Bedarf auch mit Farben ausgestattet werden. Das Vakuumgussverfahren kann kleine Chargen von Kunststoffteilen mit komplexen Strukturen, gleichmäßiger Wandstärke und bestimmten Funktionen und Aussehen herstellen.

Der Herstellungsprozess des Vakuumgießens
Der Herstellungsprozess des Vakuumgusses ist in drei Schritte unterteilt: Herstellung des Hauptformprototyps, Herstellung der Form und Gießen der Teile.
Schritt 1: Prototyp der Urform
Sie können jedes Material mit stabilen Eigenschaften auswählen, um den Prototyp der Hauptform herzustellen. Es besteht normalerweise aus Kunststoff- oder Metallmaterialien. Die einzige Anforderung ist, dass dieses Material bei einer hohen Temperatur von 40 °C über einen bestimmten Zeitraum stabil sein muss.
Bemerkenswert ist, dass der Prototyp eine entscheidende Rolle für die Qualität der kopierten Teile spielt. Wenn Sie hochpräzise, hochglänzende oder auch hochtransparente Kunststoffteile bearbeiten möchten, dann wird der Urform-Prototyp am besten per CNC-Bearbeitung bearbeitet.
Es ist auch eine ideale Wahl, den Prototyp des Master-Modells im SLA-Verfahren herzustellen, aber im Vergleich zu dem Prototyp des Master-Modells, der per CNC verarbeitet wird, können die Kosten für das endgültige Teil ganz anders sein (die Genauigkeit wird etwas schlechter sein und der Stückpreis). etwas niedriger sein); Wenn Sie sich für das Vakuumgussverfahren zur Herstellung von Teilen entscheiden, werden die Angebote verschiedener Hersteller sehr unterschiedlich sein, sogar um ein Vielfaches unterschiedlich (einer der Gründe, warum die Angebote verschiedener Hersteller unterschiedlich sind).
Die Oberfläche des Hauptmodell-Prototyps kann auch mit Sprühstruktur oder Matteffekt gestaltet werden. Die Silikonform reproduziert die Details und Texturen genau, und die Oberfläche der endgültigen Replik behält ein hohes Maß an Konsistenz mit dem Prototyp bei.
Schritt 2: Stellen Sie die Silikonform her
Die Gießform besteht aus flüssigem Silikon, auch bekannt als RTV-Form. Silikon ist chemisch stabil, selbstlösend und flexibel, minimiert die Schrumpfung und reproduziert Teiledetails effizient vom Prototyp bis zur Form. Kieselgel und Härter gleichmäßig verrühren. Das Aussehen des Formkieselgels ist eine fließende Flüssigkeit, Komponente A ist Kieselgel und Komponente B ist Härter. Beispiel: Nehmen Sie 100 Gramm Kieselgel und fügen Sie 2 Gramm Härter hinzu (Hinweis: Kieselgel und Härter müssen gleichmäßig gerührt werden. Wenn sie nicht gleichmäßig gerührt werden, härtet ein Teil der Form aus und ein Teil nicht ausgehärtet, und das Silikon wird ungleichmäßig ausgehärtet.Dies wirkt sich auf die Lebensdauer der Silikonform und die Anzahl der Formumdrehungen aus und führt sogar dazu, dass die Form verschrottet wird.
Bringen Sie Klebeband an flachen Stellen um den Prototyp herum an, um nach dem anschließenden Schneiden der Form eine Trennfläche zu bilden. Der Prototyp wird dann in einen Gießkasten gehängt und Klebestifte werden auf die Teile gelegt, um Angüsse und Entlüftungslöcher für die Entlüftung während des Silikonformprozesses bereitzustellen. Gießen Sie das Kieselgel in die Box und evakuieren Sie dann die Luftblasen. Die Zeit sollte nicht zu lang sein. Unter normalen Umständen sollte sie zehn Minuten nicht überschreiten, um zu verhindern, dass das Streichen oder Gießen unmöglich ist, nachdem Vernetzungsreaktionen aufgetreten sind.
Legen Sie die Gießbox zum Aushärten in den Ofen, die Temperatur beträgt 40 ℃, die Zeit beträgt 8-16 Stunden, diese Zeit hängt vom Volumen der Form ab.
Nachdem der Silikonkautschuk ausgehärtet ist, entfernen Sie die Schachtel und den Klebestift, schneiden Sie entlang der Trennlinie und nehmen Sie den Prototyp heraus. Zu diesem Zeitpunkt bildet der Silikonkautschuk einen Hohlraum, der genau die gleiche Form wie der Prototyp hat; Auf diese Weise kann die Silikonform erfolgreich hergestellt werden.
Schritt 3: Vakuumgießen
Die Form zum Erstarren in den Ofen stellen und auf 60-70℃ vorheizen.
Wählen Sie ein geeignetes Trennmittel und verwenden Sie es richtig, bevor Sie die Form schließen, was sehr wichtig ist, um Anhaftungen und Oberflächenfehler zu vermeiden.
Bereiten Sie das Polyurethanharz gemäß Ihren Designanforderungen vor, mischen Sie das Zweikomponentenharz im richtigen Verhältnis, rühren Sie es dann vollständig um, entgasen Sie es 50-60 Sekunden lang unter Vakuum und erwärmen Sie es vor der Verwendung auf etwa 40 °C.
Gießen Sie Polyurethanharz in den Hohlraum der Form. Nachdem die Kavität gefüllt ist, stellen Sie die Form in eine Vakuumumgebung, um die Luft in der Kavität zu entfernen, und füllen Sie jede Position der Form mit flüssigem Silikon, um sicherzustellen, dass die Form des geformten Produkts genau der des Prototyps entspricht.
Stellen Sie die Form weiterhin in den Ofen, um sie erneut auszuhärten. Durchschnittliche Aushärtezeit: 1-3 Stunden für kleine Stücke, 3-6 Stunden für große Stücke.
Nach dem Aushärten nehmen Sie das gegossene Teil aus der Silikonform und Sie erhalten eine Nachbildung des Originalteils.
Wiederholen Sie diesen Zyklus.
Materialauswahl für Vakuumguss
Polyurethan Harze sind Polymere mit einer breiten Palette von Eigenschaften und Anwendungen. Hersteller von Vakuumgussteilen beziehen Polyurethanharze, darunter Hei-Cast aus Japan und Axson aus Frankreich. Die Materialeigenschaften sind ähnlich wie bei technischen Kunststoffen wie ABS, PMMA, PC, PP, PA usw. Die Arten von Gießharzen können von transparent, durchscheinend bis zu farbigem, weichem Gummi oder hartem Kunststoff und sogar schlagzäh, hoch sein -temperaturbeständige (120°C) oder feuerbeständige (UL94-V0) Materialien. Vakuumgussverfahren kann für sekundäres Spritzgießen verwendet werden und es können auch Einsätze hinzugefügt werden;
Technische Parameter des Vakuumgießens
Beschreibung | Toleranzhinweis |
Genauigkeit | Aufgrund der thermischen Ausdehnung der Flüssigkeit und der natürlichen Eigenschaften der flexiblen Form beträgt die erwartete Schrumpfrate +0.15 %; Die Standardtoleranz beträgt ±0.15 mm/100 mm, und die höchste Genauigkeit kann ±0.05 mm erreichen. |
Maximale Größe | Vakuumgießgeräte können eine maximale Größe von 2d,0M*1.2M*1.0M aufnehmen. |
Mindestwandstärke des Teils | Um eine ausreichende Formfüllung zu gewährleisten, ist eine Wandstärke von mindestens 0.75 mm erforderlich. Für beste Ergebnisse empfehlen wir eine Wandstärke von mindestens 1.5 mm. |
Typische Anzahl von Replikaten | Bis zu 25 Repliken pro Form (je nach Formkomplexität und Gussmaterial); nur 12 oder sogar 10 Replikate können für eine Form hergestellt werden, wenn das Teil eine hohe Qualität erfordert (z. B. transparente oder komplexe Strukturen) . |
Typische Lieferzeiten | Innerhalb von 50 bis 10 Tagen können je nach Teilegröße und Stückzahl bis zu 15 Gussmuster hergestellt werden |
Veredelungsoptionen für das Vakuumumspritzen
Matt/matt.Der Master-Prototyp ist matt sandgestrahlt, das Replikatteil hat ein glattes Satin-Finish, und transparente und durchscheinende Teile mit diesem Finish erscheinen matt. Eine matte Oberfläche ist für Handheld- und High-Touch-Bereiche nützlich, da sie die Sichtbarkeit von Fingerabdrücken verringert.
Halbglänzend. Ein Finish, das etwas Glanz hat, aber nicht sehr reflektierend ist. Die halbglänzende Oberfläche liegt zwischen hochglänzend und matt, mit einer glatten, leicht zu reinigenden Oberfläche.
Hochglanz. Erstellen Sie ein hochreflektierendes Finish, indem Sie den Master-Prototypen polieren, bevor Sie die Form herstellen. Hat die höchste Transparenz für transparente Teile. Specular kann für kosmetische Modelle, Linsen und mehr verwendet werden.
Polyurethan kann mit Pigmenten gemischt werden, um eine Vielzahl von Farben zu erzielen. Schwarz, Natur, Klar und verschiedene benutzerdefinierte Farben (Raoul- oder Pantone-Farben, die Ihrer Wahl am nächsten kommen).



Vorteile des Vakuumgießens
Schnelle Abwicklung. Bis zu 50 Teile können je nach Teilespezifikation (Größe, Konstruktion) und Menge in 7-15 Tagen oder weniger geliefert werden. Im Vergleich zum Spritzgießen ist die Produktionszeit beim Vakuumgießen kürzer. Herkömmliche Spritzgussformen benötigen 4 bis 8 Wochen, um die Produktion abzuschließen. Während die Silikonform nur 1-2 Wochen benötigt, um vollständig fertig zu sein, können alle komplexen Teile in kurzer Zeit fertiggestellt werden.
Niedrige Kosten. Silikon ist im Vergleich zu Spritzgussformen kostengünstiger. Das Spritzgießen basiert auf der Stahl- oder Aluminiumfertigung. Die Kosten für eine Silikonform können zwischen Hunderten und Tausenden liegen, während die Kosten für ein Spritzgussteil zwischen Tausenden und Zehntausenden liegen.
Kann große Teile herstellen. Abhängig von der Art der verwendeten Ausrüstung können durch Vakuumgießen sehr große Teile hergestellt werden, z. B. Automobilgehäuse, große Robotergehäuse, medizinische CT-Gehäuse usw.
Die Oberflächenbeschaffenheit ist besser als beim Spritzgießen. Der Vakuumprozess entfernt Luftblasen und ermöglicht dem Material, sich vollständig mit der Kavität zu verbinden, wodurch Details erfasst werden.
Vakuumguss kann das Erforderliche realisieren komplexe Teile oder Designs auf einmal, während die CNC-Bearbeitung meistens nach Größe und Struktur aufgeteilt und produziert werden muss.
Verschiedene Farben zur Auswahl. Für eine Vielzahl von Farboptionen können dem Harz Farbpigmente zugesetzt werden.
Wiederholbarkeit. Die Silikonform kann etwa 20 Mal verwendet werden, bevor sie ersetzt werden muss.
Anwendung des Vakuumgusses
Geeignet für Kleinserienfertigung. Das Vakuum-Doppelformen ist ideal für kleine Chargen – wenn sich die Mengen als unzureichend erweisen, um in Spritzgussformen zu investieren – und für Erstserien- (Erstserien-) Produktionsteile, die Wochen fertiggestellt werden können, bevor die Produktionsformen fertig sind.
Das Vakuumgießverfahren ist relativ günstig, wodurch alle notwendigen Designänderungen einfach und wirtschaftlich werden. Darüber hinaus können verschiedene Materialien für dieselbe Form verwendet werden, sodass Designs mit mehreren Materialien getestet werden können.
Markttest. Hochwertige Oberflächen machen Vakuumgussteile ideal für Verbrauchertests, Benutzerbewertungen und Konzeptmodelle. Wenn Sie nicht wissen, welche Farbe für das Produkt am besten geeignet ist, können Sie nach demselben Designkonzept eine Silikonform herstellen, 10-15 Abgüsse machen und die Farbe und Textur Ihres Designs auf jeden Abguss malen, damit es möglich ist in der Konstruktionsabteilung eingesetzt werden Auch interne Diskussionen bei Managementmeetings ermöglichen eine schnelle Adaption von Änderungen für weitere Tests oder Markteinführungen.
Im August 2021 wollte ein Fahrradhersteller in den USA 50 Rücklichtabdeckungen mit einer regelmäßigen rautenförmigen Textur produzieren, und die Teile mussten transparent sein. Angesichts der Budgetkosten a Vakuum-Gießverfahren wurde empfohlen, und die Nachbearbeitung wurde poliert; von einem Fachmann Das Zwischenteam überprüft das Produkt und der Kunde übertrifft die Erwartungen nach Erhalt der Prototypenteile; Fazit: Die komplexen Formteile können die Struktur, Details und Textur des Prototyps genau nachbilden und die gleiche Oberflächenbeschaffenheit wie der Prototyp bieten, wodurch ein ähnliches Spritzguss-Produktionsergebnis erzielt wird.