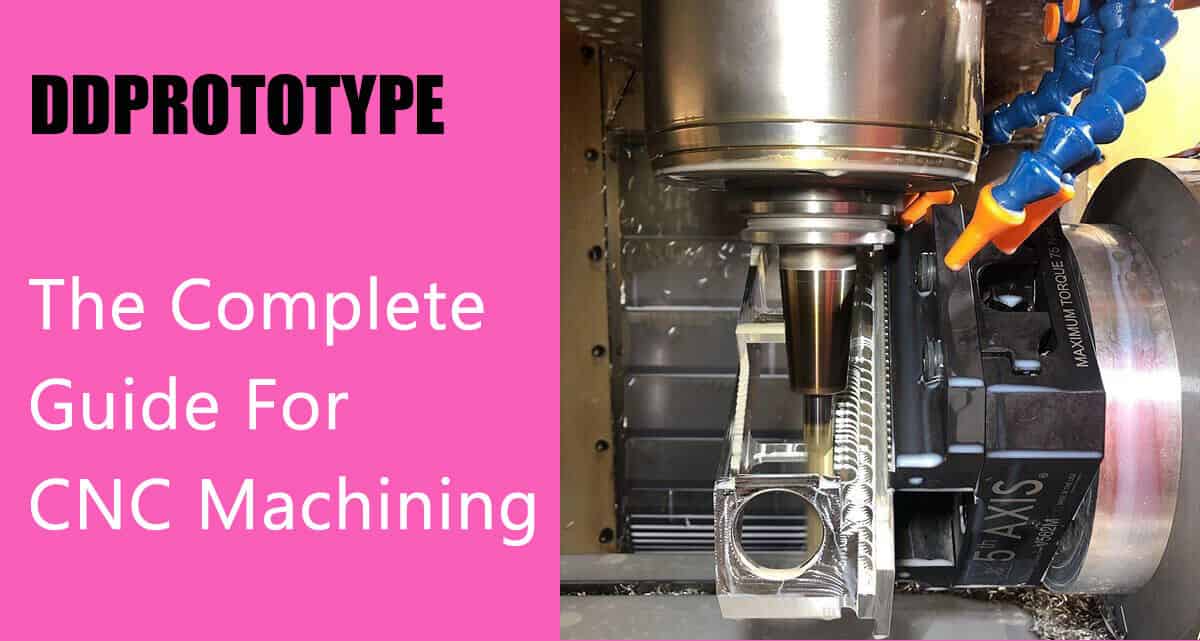
ラピッド プロトタイピング & ラピッド マニュファクチャリング エキスパート
CNC 機械加工、3D 印刷、ウレタン鋳造、ラピッド ツーリング、射出成形、金属鋳造、板金、押出成形を専門としています
CNC加工の完全ガイド
このペーパーでは、 CNC加工 世界中の設計者がアイデアを理想的なプラスチックまたは金属部品に変換するのに役立つ、長所と短所、設計ルールと技術、材料の選択、コスト削減、仕上げサービスなどを詳細に説明します。 オンラインとして CNC機械加工サービス ショップ、カスタムパーツの注文は、シンプル、迅速、簡単である必要があると考えています。 DDPROTOTYPEのコンセプトは、世界の 製造業 業界、 プロトタイプ加工 金属およびプラスチックの少量製造。 20年のCNC機械加工の経験、3000平方メートルのワークショップ、数十台の3軸および5軸CNCマシン、および日本のEDM / WEDMマシンやヘキサゴンCMMなど、ドイツ、米国、および日本の付属機器があります。 デザイナーの全エネルギーが製品デザインに集中していることを確認してください。 DDPROTOTYPEは、アレバ、オリンパス、ABBなどの世界のトップ350企業の多くを含む、世界50か国以上で500以上の顧客にサービスを提供しています。DDPROTOTYPEをオンラインCNCマシンショップとしてサプライチェーンの一部にしましょう。 。
ご不明な点がございましたら、お問い合わせください info@ddprototype.com。
CNC加工プロセスとは何ですか?
CNC機械加工では、材料を差し引いて除去することにより、原材料を最終的な形に加工します。 金属またはプラスチックのブランクを異なるテーパー、直径、および形状の部品にするために、穴、チャネル、またはボイドをドリルで開けます。 これは、特定の形状の部品を製造するために材料が追加および階層化される他のタイプの処理(例:積層造形)とは対照的です。 これは、金型を使用してさまざまな材料状態の材料を射出し、成形部品を成形する射出成形とも対照的です。 CNC機械加工は、金属、プラスチック、木材、ガラス、発泡体、その他の複合材料など、さまざまな材料に広く使用されています。 この汎用性により、CNC機械加工は業界全体で人気のある選択肢となり、設計者やエンジニアは部品を効率的かつ正確に製造できます。

CNC加工操作はXNUMXつの段階に従います
部品設計
CNC機械加工で製造された部品は、通常、初期設計としてCADソフトウェアから始まります。 設計段階では、エンジニアは、パフォーマンスを最適化するためのパラメータ、最終部品の動作条件、許容範囲の変動の許容レベルなど、必要な最終製品のすべての側面を慎重に検討します。
デザイン変換
初期設計段階の後、CADモデルはコンピューター支援製造(CAM)ソフトウェアを使用して機能的なCNCプログラムに変換する必要があります。 CAMソフトウェアは、元のCADモデルファイルから幾何学的要件を抽出し、それらをCNC互換のプログラミング言語(GコードやMコードなど)に変換して、機械の機械的動作を決定します。
CNC工作機械の準備
次に、CNC機械のオペレーターは、CNCプログラムで要求される仕様に従って機械と材料をセットアップする必要があります。 オペレーターは、正しい切断または穴あけ工具が正しく取り付けられ、適切なドリルまたはエンドミルと一致していることを確認します。 オペレーターはまた、通常は固定具に、またはCNC工作機械に直接取り付けられたワークピースをセットアップする必要があります。
プログラムされた操作の実行
最後に、CNC機械のオペレーターが必要な機械的プロセスを実行します。 運転中、CNCプログラムは工作機械の動きを正確に制御します。
CNC加工の利点:タイムリーで信頼性が高く、正確で強力
CNCフライス盤 回転は非常に正確で再現性のあるプロセスです。 仕様に応じて、+ / – 0.001“ – 0.005”の公差を実現できます。 機械は週24時間、必要に応じて週7日確実に稼働するようにプログラムできるため、CNCフライス盤はオンデマンドで部品を製造するための最良の方法の10000つです。 標準ツールを使用するCNC機械加工は、古い部品の交換や顧客への特別なアップグレードの提供など、カスタムの使い捨て部品を作成する場合に特に役立ちます。 単品生産規模をXNUMX台以上に拡大することも考えられます。 機器の数、サイズ、複雑さによっては、コンポーネントの所要時間はXNUMX日程度に短縮される場合があります。 輸送と配達により、XNUMX週間で締め切りに間に合わせることができます。
CNC機械加工技術のもう50つの大きな利点は、達成可能な機械的特性です。 射出成形や積層造形のようにブランク材料を熱間変形させるのではなく、ブランク材料を切断することで、選択した金属またはプラスチックのすべての望ましい機械的特性を維持できます。 CNCフライス盤と旋盤加工では、XNUMXを超える工業用金属、合金、プラスチックを処理できます。 この選択には、アルミニウム、真ちゅう、青銅、チタン、ステンレス鋼、ピーク、ABS、および亜鉛が含まれます。 CNC機械加工の唯一の材料要件は、部品が固定および切断に十分な硬度を備えていることです。 最も費用対効果の高いCNC機械加工部品を入手するには、生産能力を拡大して各部品のコストを分散させることをお勧めします。 CNC加工の回数が数十から数百に達すると、単価は徐々に下がります。 CNC部品の構造化された大量生産と輸送は、廃棄物や在庫のコストを削減するのに役立ちます。

短所:幾何学的複雑性のコスト
CNC機械加工の高性能を使用する場合のトレードオフの5つは、幾何学的な複雑さが犠牲になることです。 シンプルでかさばる部品は、CNCフライス盤と旋削に最適な設計です。 この工具の使用の程度は工作機械のシャフトの数に関係しますが、工具の影響により常にいくつかの設計上の制限があります。 つまり、使用する軸が多いほど、関数は複雑になります。 もうXNUMXつのトレードオフは、CNC処理の起動コストが高くなる可能性があることです。 CNCフライス盤と旋盤で工具をセットアップ、ロード、プログラムするための訓練を受けた専門家が必要です。 幸い、このコストは固定されているので、複数のパーツに同じ設定を使用することで、より経済的になります。 部品の再配置を最小限に抑えることで、コストを節約することもできます。 多面体形状では、部品を手動で再配置する必要がないため、XNUMX軸以上のシャフトでの加工の方が経済的である場合があります。
CNCフライス盤
CNCフライス盤では、部品を機械に取り付け、回転切削工具を使用して材料を除去します。 以下は、基本的なCNCフライス盤プロセスの概要です。最初に、CADモデルは、CNCマシンで解釈できる一連のコマンド(gコード)に変換されます。 これは通常、提供された技術図面を使用して機械のオペレーターによって行われます。次に、材料(ブランクまたはワークピースと呼ばれる)を特定のサイズにカットし、万力を使用して構築されたプラットフォームに配置するか、機械に直接取り付けます。 。 正確な位置決めと位置合わせは、特別な測定ツールが通常使用される正確な部品を製造するための鍵です。

次に、特殊な切削工具を使用して非常に高速(キロRPM)で回転し、ブランクから材料を取り除きます。 通常、設計されたパーツを作成するには数回のパスが必要です。 まず、材料を低精度ですばやく除去して、ブランクのおおよその形状を提供します。 次に、XNUMXつまたは複数の仕上げパスを使用して最終部品を作成します.XNUMXつの設定で切削工具では実現できない機能がモデルにある場合(たとえば、裏面にスロットがある場合)、部品を反転して上記の手順を繰り返します。
機械加工後、部品のバリ取りが必要です。 バリ取りは、機械加工中の材料の変形によって鋭いエッジに残った小さな欠陥(たとえば、ドリルビットが貫通穴から遠くにあることによる欠陥)を取り除くための手動プロセスです。 次に、技術図面で公差が指定されている場合は、主要な寸法がチェックされます。 その後、部品を使用または後処理することができます。ほとんどのCNCフライス盤システムには、X、y、Z軸の5つの線形自由度があります。 XNUMX自由度のより高度なシステムでは、ベッドやビット(A軸とB軸)を回転させることもできます。 XNUMX軸CNCシステムは、幾何学的複雑性の高い部品を製造でき、さまざまな工作機械の設定が不要になります。

CNC旋盤
CNC旋削では、部品を回転チャックに取り付け、固定切削工具を使用して材料を除去します。 このようにして、中心軸に沿って対称なパーツを作成できます。 旋削部品は通常、フライス盤部品よりも速く(そして安価に)製造されます。
これは、CNC旋削で従うべきステップの要約です:
まず、CADモデルからGコードを生成し、次に適切な直径のシリンダーをCNC工作機械にロードします。
パーツは高速で回転し始め、固定切削工具はそのプロファイルを追跡し、デザインのジオメトリが作成されるまで徐々に材料を除去します。 中心軸に沿った穴は、センタードリルと内部切削工具を使用して作成することもできます。
パーツを裏返したり移動したりする必要がある場合は、このプロセスを繰り返します。 それ以外の場合は、部品を在庫から切り取って使用したり、さらに後処理したりすることができます。

典型的なCNCターニングパーツは、円筒形のブランクから材料を取り除くことによって作られます。
一般に、CNC旋盤システム(旋盤とも呼ばれます)は、円筒形のプロファイルを持つ部品を製造するために使用されます。 非円筒部品は、CNCフライス盤を備えた最新の多軸CNCターニングセンターを使用して製造できます。 これらのシステムは、CNC旋削の高い生産性とCNCフライス盤機能を組み合わせており、カムシャフトやラジアルコンプレッサーインペラーなど、回転対称のさまざまな形状を生成できます。 CNC旋削加工では、主軸上でワークが高速回転しても切削工具は静止したままです。 CNC旋削は、厳しい公差のある円筒部品を迅速に製造できます。 たとえば、ddprototype CNC旋盤は、±152インチの厳密な許容誤差を維持しながら、直径240インチ、長さ0.001インチまでの部品を製造できます。
フライス盤と旋盤システムの境界はあいまいであるため、このペーパーの残りの部分では、より一般的な製造プロセスであるCNCフライス盤に焦点を当てます。

CNC工作機械の種類
最も一般的なタイプのCNCマシンは、切削工具を使用してワークピースから余分な材料を取り除くものです。 CNCマシンはウォータージェット切断および放電加工(EDM)で動作しますが、このガイドでは3軸および多軸CNCマシンに焦点を当てます。
3軸CNC工作機械
3軸CNCフライス盤は、最も一般的な形状を作成するために使用できるため、非常に一般的です。 それらはプログラミングと操作が比較的簡単であるため、起動処理コストは比較的低くなります。 工具へのアクセスは、CNCフライス盤の設計上の制約となる場合があります。 使用できる軸は3つしかないため、一部の領域にアクセスできない場合があります。 ワークを一度だけ回転させる必要がある場合、これは大きな問題ではありませんが、何度も回転させる必要がある場合、人件費と処理コストが急速に増加します。 XNUMX軸マシンにより、切削工具はまっすぐなXNUMX次元ベクトル(上下、左右、前後)に沿って移動できます。

多軸CNC工作機械
多軸CNC工作機械は3軸工作機械に似ていますが、機械的運動の自由度が高くなっています。 たとえば、多軸工作機械は、回転および斜めの切削操作を使用できます。 多軸CNC工作機械には主にXNUMXつのタイプがあります。
インデックス5軸CNCフライス盤
フライス盤が運転中にXNUMXつの直線軸に沿ってしか切断できない場合でも、オペレーターはXNUMXつの操作の間の次の切断のためにベッドとカッターヘッドを回転させることができるため、成形能力が向上します。
連続5軸CNCフライス盤
この機械タイプは、動作中にXNUMXつの直線軸とXNUMXつの回転軸に沿った連続動作を可能にします。 これにより、オペレーターはターゲットアーティファクトから非常に複雑なテーブルを作成できます。

フライス盤ターニングセンター
フライス盤はCNC旋盤とCNCフライス盤の機能を兼ね備えています。 ワークピースは、高速で回転させることも、フライス盤上に正確に配置してフライス盤操作を行うこともできます。
さまざまな機械構成の中で、最も簡単なセットアップは3軸CNCフライス盤です。これは通常、公差の大きい単純な部品を作成するための最も安価な方法です。 ねじやカップリングなどの円筒形のワークピースが必要な場合、旋盤のCNC旋削も非常にコスト競争力のあるプロセスです。 一般的に、同様の部品の場合、旋盤のコストは15軸工作機械のコストよりもXNUMX%低くなります。
5軸CNC加工を使用する場合、5つのオプションがあります。インデックス5軸CNCフライス盤と連続5軸CNCフライス盤です。 5軸CNCフライス盤では、ワークが自動的に回転するため、カッターがフライス盤機能を使いやすくなります。 部品を固定具から取り外すことなく、フライス盤ステップ間で3つの追加の運動方向が達成されます。 連続5軸CNCフライス盤の違いは、ワークを切断するときに機械がすべての方向に同時に移動できることです。 どちらのプロセスも、ワークピースを手動で再配置することに関連するコストの増加と潜在的な人的エラーを排除します。 これらの利点があるため、複雑な部品には5軸加工が最適なソリューションです。 「基本的な」5軸CNCフライス盤と比較して、20軸加工のコストが高くなり、インデックス5軸CNCフライス盤は3つのうち安価です。 連続XNUMX軸CNCフライス盤のコストは、通常、インデックスXNUMX軸工作機械のコストよりもXNUMX%以上高く、標準のXNUMX軸フライス盤のコストの約XNUMX倍です。

CNC機械加工部品の設計–CADモデルの設計
CADのコンセプトは加工点です。 製品の最終用途に直接関係する設計要件に加えて、エンジニアは実際の切削作業に使用されるCNC工作機械の機能と制限にも注意を払う必要があります。 エンジニアは、元のCADモデルファイルをオープンソースステップやIGES形式などのCNC互換形式、またはIPTやsatなどのより制限された形式に変換する必要があります。 また、エンジニアがデジタルCAD命令とともに送信される技術図面を作成することもベストプラクティスです。 これらの図面は、設計公差と形状を確認するために使用されます。 機械工が部品の顕著な特徴を特定するのを手伝ってください。 問題が発生した場合の実際の検証ソースとして機能します。
CNC機械加工プロセスのXNUMXつのルール
ルール1:すべての道路は半径につながる
ほとんどのドリルは円筒形の設計であるため、これは、内部でカットを行うと、丸みを帯びたコーナーとも呼ばれる湾曲したコーナー/エッジも生成されることを意味します。 内部フィレットを使用して部品を設計する場合は、「大きいほど良い」という原則に従ってください。 結果として得られる角度は、使用するツールの直径の半分になります。
1.25mmではなく1mmなどの非標準の半径を使用して、特定の工具クリアランスでコーナーをカットできるようにします。 可能であれば、プロセス全体で同じツールを使用できるように、異なる壁と床の半径も設計に使用する必要があります。
内側の角の正確な測定は、加工されるキャビティの深さに関係します。 内側のコーナーとエッジを挿入する場合、半径はキャビティの深さのXNUMX分のXNUMXより大きくする必要があります。
ルール2:直角アンダーカット
CNC機械加工部品に直角を作成するには、コーナーの半径を小さくして同様の結果を得るよりも、設計にアンダーカットを追加することをお勧めします。 カスタムツールの追加コストを回避するには、標準サイズ、つまり幅3mmから40mmのアンダーカットスロットをミリメートル単位で設計します。 使用する工具の形状により、アンダーカットは可能な限り浅くする必要があります。 アンダーカットツールが到達できる最大の深さは、ツールヘッドの幅のXNUMX倍になります。
ルール3:フィレットは虫歯を引き起こす可能性があります
キャビティ/キャビティの深さは通常、内部フィレットの作成に使用されるツールの直径に関連しています。 目安として、溝の深さは工具径の3〜4倍までにしてください。 深さが工具径の6倍を超える場合は、より大きな工具が必要になります。 これにより、コーナー半径が犠牲になります。 キャビティを加工するときは、キャビティ幅も考慮する必要があります。 深さは幅の4倍に保つのが最善です。これは良いガイドです。
ルール4:背の高い特徴、悪い振動
キャビティとピットの深さと同様に、背の高いフィーチャの最大高さは、最大でフィーチャ幅の4倍です。 フィーチャーが高いほど振動しやすくなり、部品の加工精度が低下します。
ルール5:薄い壁を避ける
一般的に、部品の設計には厚い壁を使用することをお勧めします。 高い壁と同様に、薄壁のフィーチャーを作成すると振動が増加します。 プラスチックを処理するときは、熱も考慮する必要があります。 カッターヘッドの摩擦により、壁が薄いほど柔らかくなり、反りやすくなります。 目安として、プラスチック壁の最小厚さは1.0〜1.5mmにする必要があります。 金属部品の最小肉厚は、0.5mmから0.8mmの間です。 壁が支えられている場合は、振動や震えを避けるために、壁を厚くするか高くする必要があります。
ルール6:ドリルするときは標準に従ってください
CNCフライス盤で選択できる穴には、止まり穴と貫通穴の25.5種類があります。 選択したタイプに関係なく、推奨される深さと直径は同じです。 穴の直径は、1 mm(10 mmを超える直径)以上の標準ビットサイズに関連している必要があります。 穴の公称深さは、穴の最大直径によって異なります。 通常、穴の深さは、穴の公称直径のXNUMX倍に等しく作成されます。
ルール7:スレッド標準への準拠
スレッドを作成するときは、標準サイズを維持することも重要です。 スレッドが大きいほど、処理が簡単になります。 最大長は、穴の呼び径の3倍に維持する必要があります。 パーツに既製のねじサイズを保持することにより、追加コストを回避できます。
CNC材料選択ガイドライン
CNC機械加工作業には、適切な材料の選択が不可欠です。 選択は、最終製品の使用目的に大きく依存します。 サブトラクティブ製造プロセスとして、CNC機械加工では、金属やプラスチックなどの原材料を使用して部品を製造します。 このブロックはマテリアルブランクと呼ばれます。 どの材料を使用する場合でも、製造プロセスの前に正しいブランクサイズを選択することが非常に重要です。 一般に、原材料の不整合を解決するために、各サイズが最終部品サイズより少なくとも0.125インチ(〜0.3 cm)大きいブランクを選択することをお勧めします。 同時に、材料の無駄を最小限に抑えるために、大きすぎるブランクを使用しないことが重要です。 CNC機械加工部品を注文する前に覚えておくべきもう一つの重要なことは、材料の選択が生産時間とコストに影響を与えるということです。 これは、一部の材料が他の材料よりも機械加工性に優れているため、処理が容易であるためです。 より速い処理速度は、最終的にはより低い生産コストにつながります。

金属は主に、高強度、硬度、耐熱性を必要とする用途に使用されます。 プラスチックは、耐薬品性や電気絶縁性から、通常、さまざまな物性を備えた軽量素材です。 対象となる材料特性は、機械的強度(引張降伏強度として表される)、機械加工性(機械加工性は、CNCの価格設定に影響します)、材料コスト、硬度(主に金属の場合)、および耐熱性(主にプラスチックの場合)です。
次のようなさまざまな材料特性を調べて、設計に最も適した材料を決定する必要があります。
抗張力
硬度
操作が簡単です
耐薬品性
耐食性
熱性能
金属部品
一般に、CNCフライス盤は金属をより簡単に切断し、より高い効率を達成できるため、延性の高い金属は処理が容易です。 たとえば、真ちゅうは延性が優れているため、処理が最も簡単な金属の304つです。 アルミニウム合金はCNC加工にも非常に適しているため、製造時間を短縮できます。 一方、鋼はアルミニウムよりも機械加工性がはるかに低い固体金属であるため、生産性が低く、コストが高くなります。 ただし、鋼のグレードが異なれば、炭素含有量に応じて作業性のレベルも異なることを覚えておくことが重要です。 炭素含有量が非常に低い鋼と非常に高い鋼は、通常、機械加工が困難です。 例えば、低炭素含有量のステンレス鋼303は、粘着性になり、硬化が速すぎるため、機械加工が困難です。 硫黄やリンなどの添加剤は、ステンレス鋼XNUMXなどのステンレス鋼の加工を容易にします。機械加工の観点から、炭素鋼は通常、アルミニウムのXNUMX倍の時間がかかりますが、ステンレス鋼はXNUMX倍の時間がかかります。

プラスチックの部品
熱可塑性プラスチックは機械加工できますが、ポリマーの材料特性はCNC機械加工に課題をもたらす可能性があります。 まず、熱伝導率が低いため、多くの熱可塑性プラスチックは、CNCフライスカッターまたはドリルビットと接触すると溶融または反ります。 金属の強度と剛性を必要としない部品の場合、熱可塑性プラスチックはより安価なオプションを提供します。 熱可塑性プラスチックの範囲では、デルリン(POM)、高密度ポリエチレン(HDPE)、およびABSが優れた機械加工性を備えています。 ピーク、ULTEM、ナイロン、および多くの複合材料は、その強度と耐久性で人気がありますが、処理がより困難です。

アルミニウム合金
アルミニウム合金は、優れた強度/重量比、高い熱伝導率と伝導率、および自然耐食性を備えています。 加工が簡単でバッチコストが低いため、カスタムの金属部品やプロトタイプを作成するための最も経済的なオプションであることがよくあります。アルミニウム合金は通常、鋼よりも強度と硬度が低くなりますが、陽極酸化してその上に硬質保護層を形成することができます。水面。
アルミニウム合金6061は、他のアルミニウム合金よりも優れた切削強度を備えています。
アルミニウム6082の組成と材料特性は6061のものと類似しています。これはヨーロッパの基準を満たしているため、ヨーロッパでより一般的に使用されています。
アルミニウム7075は、鋼の優れた疲労特性を持ち、熱処理して高い強度と硬度を実現できるため、航空宇宙用途で最も一般的に使用される合金です。そのため、軽量化が不可欠です。
アルミニウム5083は、他のほとんどのアルミニウムよりも強度が高く、耐海水性に優れています。 CNCアルミ加工 したがって、建築および海洋用途で一般的に使用されます。 溶接にも最適です。
材料特性:
アルミニウム合金の典型的な密度:2.65-2.80 g / cm3
陽極酸化することができます
非磁性
ステンレス鋼
ステンレス鋼合金は、高強度、高延性、優れた耐摩耗性、耐食性を備えており、溶接、機械加工、研磨が容易です。 それらの組成に応じて、それらは(基本的に)非磁性または磁性である可能性があります。
ステンレス鋼304は、優れた機械的特性と優れた機械加工性を備えた最も一般的なステンレス鋼合金です。 それはほとんどの環境条件と腐食性媒体に耐性があります。
ステンレス鋼316は、304と同様の機械的特性を持つ別の一般的なステンレス鋼合金です。特に塩溶液(海水など)では耐食性と耐薬品性が高くなりますが、通常、過酷な環境での使用に適しています。
ステンレス鋼2205デュプレックスステンレス鋼は、最高強度のステンレス鋼合金(他の一般的なステンレス鋼合金のXNUMX倍)であり、優れた耐食性を備えています。 過酷な環境で使用され、石油およびガス産業で多くの用途があります。
ステンレス鋼303は靭性に優れていますが、304よりも耐食性が低くなっています。機械加工性に優れているため、航空宇宙用途のナットやボルトなどの大量用途によく使用されます。
17-4ステンレス鋼(SAE 630グレード)の機械的特性は304に匹敵します。それは(工具鋼と比較して)非常に高度に析出硬化することができ、優れた耐薬品性を備えているため、非常に高性能な用途に適しています。タービンブレードの製造など。

材料特性:
典型的な密度:7.7-8.0 g / cm3
非磁性ステンレス鋼合金:304、316、303
電磁ステンレス鋼合金:2205デュプレックス、17-4
低炭素鋼{軟鋼}
低炭素鋼は、低炭素鋼とも呼ばれ、優れた機械的特性、優れた機械加工性、および優れた溶接性を備えています。 低コストであるため、機械部品、固定具、固定具の製造など、一般的な目的に使用できます。 低炭素鋼は腐食や化学的攻撃を受けやすいです。
低炭素鋼1018は、優れた被削性と溶接性に加えて、優れた靭性、強度、硬度を備えた一般的な合金です。 最も一般的に使用されている低炭素鋼合金です。
低炭素鋼1045は、優れた溶接性、優れた被削性、高強度、耐衝撃性を備えた中炭素鋼です。
低炭素鋼A36は、溶接性に優れた一般的な構造用鋼です。 さまざまな産業および建築用途に適しています。

材料特性:
典型的な密度:7.8-7.9 g / cm3
磁気
合金鋼
合金鋼には、炭素に加えて他の合金元素が含まれているため、硬度、靭性、耐疲労性、耐摩耗性が向上します。 低炭素鋼と同様に、合金鋼も化学的腐食や腐食の影響を受けやすくなっています。
合金鋼4140は、優れた全体的な機械的特性に加えて、優れた強度と靭性を備えています。 この合金は多くの産業用途に適していますが、溶接にはお勧めできません。
合金鋼4340は、優れた靭性、耐摩耗性、疲労強度を維持しながら、高い強度と硬度を実現するために熱処理することができます。 この合金は溶接可能です。

材料特性:
典型的な密度:7.8-7.9 g / cm3
磁気
工具鋼
工具鋼は、硬度、剛性、耐摩耗性、耐熱性に優れた金属合金の一種です。 これらは、金型、金型、金型などの製造ツール(名前の由来)を作成するために使用されます。 良好な機械的特性を得るには、熱処理する必要があります。
工具鋼D2は耐摩耗性合金の一種で、硬度を425°Cに維持できます。通常、切削工具や金型の製造に使用されます。
工具鋼A2は、空気硬化性の一般工具鋼の一種で、高温での靭性と寸法安定性に優れています。 通常、射出成形金型の製造に使用されます。
工具鋼O1は、65HRCの高硬度の油硬化合金です。 一般的に切削工具や切削工具に使用されます。

材料特性:
典型的な密度:7.8 g / cm3
典型的な硬度:45-65 HRC
真鍮
真ちゅうは、機械加工性と導電性に優れた金属合金であり、低摩擦を必要とする用途に最適です。 また、美的目的で金色の外観を持つ部品を製造するために建築でよく使用されます。
真ちゅうc36000は、引張強度が高く、自然耐食性に優れた材料の一種です。 処理が最も簡単な材料のXNUMXつであるため、大量のアプリケーションでよく使用されます。

材料特性:
典型的な密度:8.4-8.7 g / cm3
非磁性
ABS
ABSは、優れた機械的特性、優れた衝撃強度、高い耐熱性、および優れた機械加工性を備えた最も一般的な熱可塑性材料のXNUMXつです。
ABSの密度が低いため、軽量アプリケーションに非常に適しています。 CNCで機械加工されたABS部品は、通常、射出成形による大量生産の前にプロトタイプとして使用されます。
材料特性:
典型的な密度:1.00-1.05 g / cm3

ナイロン
ポリアミド(PA)としても知られるナイロンは、熱可塑性プラスチックの一種であり、その優れた機械的特性、優れた衝撃強度、高い耐薬品性、耐摩耗性により、エンジニアリングアプリケーションで広く使用されています。 吸湿しやすいですが。
ナイロン6とナイロン66は、CNC機械加工で最も一般的に使用されるグレードです。
材料特性:
典型的な密度:1.14 g / cm3

ポリカーボネート繊維
ポリカーボネートは、靭性が高く、機械加工性が高く、衝撃強度に優れた熱可塑性樹脂です(ABSよりも優れています)。 着色することもできますが、通常は光学的に透明であるため、流体機器や自動車用ガラスなどの幅広い用途に最適です。
材料特性:
典型的な密度:1.20-1.22 g / cm3

POM(デリン)
デルリンという商品名のPOMは、プラスチックの中で最も加工性の高いエンジニアリング熱可塑性プラスチックとして知られています。
POM(Delrin)は通常、プラスチック部品を高精度、高剛性、低摩擦、高温での優れた寸法安定性、および非常に低い吸水率でCNC加工する場合に最適です。
材料特性:
典型的な密度:1.40-1.42 g / cm3

PTFE(テフロン)
一般にテフロンとして知られているPTFEは、優れた耐薬品性と耐熱性を備え、既知の固体の中で最も低い摩擦係数を備えたエンジニアリング熱可塑性プラスチックです。
PTFE(ポリテトラフルオロエチレン)は、200℃を超える温度に耐えることができる数少ないプラスチックのXNUMXつであり、優れた電気絶縁体です。 ただし、純粋な機械的特性があり、通常、アセンブリのライニングまたはインサートとして使用されます。
材料特性:
典型的な密度:2.2 g / cm3

高密度ポリエチレン
高密度ポリエチレン(HDPE)は、熱可塑性プラスチックの一種で、強度と重量の比率が高く、耐衝撃性が高く、耐候性に優れています。
HDPEは軽量の熱可塑性プラスチックで、屋外での使用やパイプライン輸送に適しています。 ABSと同様に、射出成形の前にプロトタイプを作成するためによく使用されます。
材料特性:
典型的な密度:0.93-0.97 g / cm3

asfasdf
Peekは、優れた機械的特性、広い温度範囲での熱安定性、およびほとんどの化学物質に対する優れた耐性を備えた高性能エンジニアリング熱可塑性プラスチックです。
ピークは、重量と重量の比率が高いため、金属部品の代わりによく使用されます。 また、ピークを生物医学的用途に適したものにする医療レベルも提供します。
材料特性:
典型的な密度:1.32 g / cm3

ルールの概要
アルミニウム6061は、最も一般的なCNC機械加工材料であり、コストが最も低くなっています。
POM(Delrin)は、その優れた加工性により、最も経済的なCNCプラスチックです。
高強度、硬度、および/または耐熱性を必要とする用途には、金属合金を選択してください。
軽量アプリケーションまたは射出前のプロトタイプには、特別な材料要件を持つプラスチックを選択してください。
各種材料の適用範囲
アルミニウム
主要な性能:アルミニウムは、その強度対重量比および耐食性で高く評価されています。 また、熱伝導率と伝導率も良好です。
アルミニウム6061-t6:6061は、最も一般的に使用されているアルミニウムの種類の6つであり、広く使用されています。 T276マークは、材料にXNUMXMPaの極限引張強さを与えます。 一般的なアプリケーション:一般
アルミニウム7075:極限引張強さは572 MPaで、鋼に匹敵します。 高ストレスのアプリケーションに役立ち、その使用は高コストによって制限されます。 一般的なアプリケーション:航空宇宙、自動車、船
アルミニウム2024-T3:2024-T3 2000シリーズ合金は、強度重量比が高く、引張強度は400〜430 MPa、降伏強度は少なくとも270〜280MPaです。 T3認証、溶体化熱処理、冷間加工を実施しています。 一般的なアプリケーション:産業、航空宇宙、医療、電子製品。
アルミニウム5052:117 MPaで、この種のアルミニウム合金の疲労強度は、ほとんどのアルミニウム合金よりも高くなっています。 また、優れた海水および塩水噴霧耐性を備えています。 一般的なアプリケーション:船、航空宇宙、電子機器。
アルミニウムmic-6:7000シリーズのアルミニウム合金と同様に、mic-6は金型や基板に一般的に使用される鋳造プレート材料です。 一般的なアプリケーション:航空宇宙、電子機器、ギア。

真ちゅう、青銅、銅
主な機能:純銅は、熱伝導率と電気伝導率が高く、柔らかく展性のある金属です。 真鍮と青銅は銅の合金です。 真鍮は銅と亜鉛の混合物であり、青銅は主に銅とスズです。 一般的に、真ちゅうはその機械加工性と高い強度保持力で高く評価されています。 青銅は摩擦性能が低く、耐食性が高い。 真ちゅう、青銅、銅は通常、審美的な目的で選択されます。
C360真ちゅう:C360は、すべての真ちゅう合金の中で最も低コストで、機械加工性の高い材料です。 業界:業界、ビジネス。
真ちゅう260:最も展性のある真ちゅう合金260は、他の同様の製品よりも多く使用されています。 産業:産業、商業。
C932M07 ベアリング ブロンズ: 軽量用途向けのこの合金は、加工が容易で耐腐食性があります。 業種:一般。
ETP銅C110:この合金は、銀(100%IACS)を除くすべての金属の中で最も高い電気伝導率(105%IACS)を持っています。 産業:電力、建設、医療。
銅101:多くの真ちゅうや青銅の母材である銅101は、高い延性(伸び5%〜50%)と衝撃強度を備えています。 産業:電子機器、自動車。
鋼
主な機能:CNC機械加工材料の最も広い範囲を提供すると言うことができます、鋼はステンレス鋼、合金、工具および低炭素鋼のオプションを持っています。 一般的に、鋼は優れた機械的特性を持ち、加工が容易です。
鋼1018:この低炭素汎用鋼は延性があり、成形および溶接に適しています。 業界:一般、ギア、ネジ、ナット。
ASTM A36:低炭素鋼の例であるA36は、400〜550 MPaの極限引張強さや20%の破断点伸びなど、優れた機械的特性を備えた低コストの合金です。 業界:ギア、建設。
合金鋼4130:この多機能鋼合金は、組成(強度限界(670 MPa)、靭性(降伏強度435 MPa)、および被削性)の観点から最適化されています。 産業:航空宇宙、石油およびガス、自動車。
ステンレス鋼304:最も一般的なステンレス鋼の種類であり、鋼の基本的な品質を代表するこの合金は、他のほとんどの鋼よりも耐食性が高く、導電率が低くなっています。 溶接が必要な用途には適していません。 産業:食品、ネジ、自動車。
ステンレス鋼17-4:この析出硬化ステンレス鋼は、その高い強度と機械的特性で知られており、熱処理によってさらに開発することができます。 華氏600度でも優れた機械的特性を持ち、高い耐食性を備えています。 この材料は、過酷な環境でうまく機能します。 産業:原子力、海洋、食品、医療。
チタン
主な特徴:チタンはアルミニウムよりも重いですが(ただし、鋼よりも軽い)、チタンはその優れた重量対強度比でも知られています。 それらの硬度のために、多くのチタンの品種は加工が難しいと考えられています。
チタングレード2:グレード2は、高強度(限界344 MPa)と優れた耐食性を備えたこの金属の一般的な形態です。 通常、熱交換器の製造に使用されます。 産業:航空宇宙、自動車、化学。
チタン6Al-4V:別の一般的に使用されるチタンの種類であるこの合金は、低密度(4.429 – 4.512 g / cm3)と優れた耐食性が必要な場合に最適です。 産業:医療、航空宇宙、海洋、天然ガス。

亜鉛合金
主な機能:亜鉛は、ほとんどの品種が脆すぎて処理できないため、CNC機械加工では一般的に使用されていません。 いくつかの特定の形式では、材料は処理しやすく、扱いやすくなります。
亜鉛合金板500:優れた導電性と高い耐食性を備えた機械加工可能な亜鉛を含む連続鋳造合金。 業界:建築。
プラスチック素材
主な機能:軽量で頑丈な一部の工業用プラスチックは、金属部品の低コストの代替品と見なすことができます。 プラスチックはあらゆる産業で広く使用されています。
Abs:電気絶縁を備えたこの一般的な高強度熱可塑性プラスチックは、低コストで軽量の金型やプロトタイプに最適です。 業界:一般、医療、自動車、電子機器。
アセタール:デルリンは最も加工しやすいプラスチックです。 優れた剛性(曲げ強度82.7 MPa)、低摩擦、優れた耐湿性を備えています。 業界:一般、ギア、電子機器、医療、建設。
ナイロン6/6:一般的なポリアミド、ナイロン6/6(または略して66)は、高い機械的強度(66 MPa)、熱的および化学的作用下での剛性と安定性を備えています。 産業:自動車、電子機器、ギア、パイプ。
ピーク:この高度な熱可塑性プラスチックは、機械的要件が高いあらゆる場面で使用できます。 業界:医療、航空宇宙、自動車、電子機器。
ポリカーボネート:一般にPCとして知られているこの透明なプラスチックは、優れた光学特性を備えています。 頑丈で軽量、頑丈で耐衝撃性に優れています(600 – 850 J / M)。 業界:一般、電子機器、航空、自動車、パイプライン。
仕上げサービス
機械加工後の仕上げサービスにより、製造される部品の外観、表面粗さ、硬度、および耐薬品性が変化する可能性があります。 以下は、CNC機械加工の最も一般的な表面処理の概要です。
機械加工
機械加工された部品は、追加の作業が必要ないため、最も厳しい公差があります。 ただし、切削工具パスに沿ったマーキングは表示されます。 機械加工部品の標準的な表面粗さは3.2μm(125μin)ですが、さらに操作することで0.4μm(16μin)に減らすことができます。
最も厳しい寸法公差。
追加費用なし(標準的な表面処理)。

ビーズブラスト
ビードブラストは、機械加工された部品に均一なマットまたはサテン仕上げを追加し、すべてのツールマークを排除します。
得られた表面粗さは保証できないため、ビードブラストは主に審美的な目的で使用されます。 寸法変化を避けるために、主要な表面または穴などのフィーチャーをマスクすることができます。
心地よいマットまたはサテン仕上げ。
低コストの表面処理。
異なる粗さを提供します。

陽極酸化(透明または着色)
陽極酸化処理により、アルミニウム部品の表面に薄くて硬い非導電性セラミックコーティングが追加され、耐食性と耐摩耗性が向上します。
重要な領域をマスクして、厳密な許容誤差を維持できます。 陽極酸化された部分は、滑らかで美しい表面を作り出すために染色することができます。
耐久性のある美しい外観。
内腔に適用することができます。
パントンの色合いに着色することができます。

ハードコーティングアルマイト
ハードコーティングの陽極酸化により、優れた耐食性と耐摩耗性を提供する厚くて高密度のセラミックコーティングが生成されます。
ハードコーティングアルマイトは、機能的な用途に適しています。 通常、50μmの一般的なコーティング厚さは適用されません。 重要な領域をマスクして、厳密な許容誤差を維持できます。
ハイエンドエンジニアリングアプリケーション向けの高耐摩耗性コーティング。
内腔に適用することができます。
良好な寸法管理。

粉体塗装
粉体塗装は、部品の表面に強力で耐摩耗性および耐腐食性の保護ポリマーコーティングの層を追加します。
あらゆる素材のパーツに適用でき、さまざまな色から選択できます。
機能的な用途向けの堅牢で耐摩耗性および腐食性のコーティング。
陽極酸化よりも耐衝撃性に優れています。
すべての金属材料と互換性があります。

シルクスクリーン印刷
スクリーン印刷は、美的目的でCNC機械加工部品の表面にテキストやロゴを印刷するための安価な方法です。
陽極酸化などの他の仕上げに加えて使用することができます。 パーツの外面には、印刷されたコンテンツのみを適用できます。
カスタムテキストまたはロゴを低コストで印刷します。
さまざまな色があります。

CNCプロジェクトの予算を削減するためのヒント
CNC機械加工部品のコストは、次の要因によって異なります。
処理時間とモデルの複雑さ:部品の形状が複雑になるほど、処理時間が長くなり、コストが高くなります。
立ち上げ費用:CADファイルの準備とプロセス計画に関連しますが、費用は基本的に固定されています。 規模の経済を通じて単価を下げる機会があります。
材料費と表面処理:バルク材料のコストと材料の処理の容易さは、総コストに大きく影響します。
まとめましょう
3軸CNCフライス盤は、比較的単純な形状の部品を低コストで製造でき、優れた精度を備えています。
CNC旋盤の単価は最低ですが、回転対称の部品にのみ適しています。
インデックス付きの5軸CNCフライス盤で作られた部品は、主軸のXNUMXつと素早く位置合わせできず、高精度であるという特徴があります。
連続5軸CNCフライス盤で製造された部品は、非常に複雑な「有機」形状と滑らかな輪郭を持っていますが、コストが高くなります。
フライス盤CNCセンターは、CNC旋盤とCNCフライス盤の利点を5つのシステムに組み合わせて、他のXNUMX軸CNCシステムよりも低コストで複雑な部品を製造します。

CNC機械加工部品は、あらゆる分野で広く使用されています。 ddprototypeでは、次のような幅広い分野にサービスを提供しています。
医療
自動車
自転車
ロボット
航空宇宙
船
農業機械
電子製品
あらゆる分野のカメラおよびその他の精密製造部品