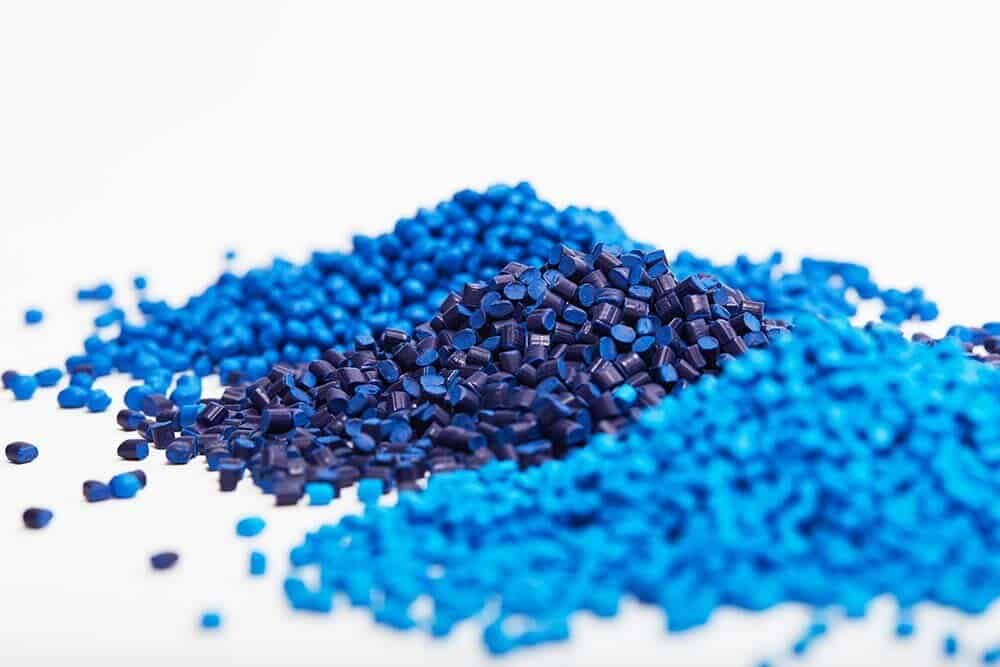
ラピッド プロトタイピング & ラピッド マニュファクチャリング エキスパート
CNC 機械加工、3D 印刷、ウレタン鋳造、ラピッド ツーリング、射出成形、金属鋳造、板金、押出成形を専門としています
適切な射出成形材料を選択するにはどうすればよいですか?
不完全な統計によると、材料ライブラリには現在 45 のポリマー シリーズ、85,000 種類ものプラスチックがあり、熱硬化性プラスチックと熱可塑性プラスチックの XNUMX つのカテゴリに大別できます。 射出成形は、大量の部品を製造する最も一般的な方法の XNUMX つであり、適切な材料を選択することは困難な作業のように思える場合があります。 これには、材料の詳細な理解が必要であり、部品を作成する目的、効率、およびコストに言及する必要があります。 確かに、特定の材料の方が適している場合もありますが、射出成形に関しては「万能」というものはありません。 適切な素材を選択することで、パーツの形状、フィット感、機能を向上させることができます。 最終的な分析では、選択された材料は常に部品の用途に直接関係しています。
1. 熱硬化性プラスチックと熱可塑性プラスチックの違い
熱硬化性樹脂と熱可塑性樹脂の主な違いは、熱に反応して結果が異なることです。
熱硬化性プラスチック. この材料は、加熱または高温にさらされると強度が増します。 たとえば、熱硬化性プラスチック製品は、高温にさらされたり、高温にさらされたりしても、全体的な強度と形状を保持します。 この特徴的な決定は、大型の恒久的な部品やアセンブリを製造する場合に役立ちます。 より多くの用途や極端な条件にも耐えます。 熱硬化性樹脂にも重大な欠点があります。 一度加熱すると内部構造が変化し、形を変えることができず、再利用できません。 熱硬化性プラスチックは融点が高いため、射出成形プロセスには適していません。 また、すべての熱硬化性樹脂の融点が同じというわけではありません。 各材料は熱に対して異なる反応を示すため、特定の種類の熱硬化性プラスチックでは特殊な機械が必要になる場合がありますが、これは一般的に一般的ではありません。

熱可塑性樹脂。熱可塑性樹脂は、加熱と冷却を繰り返しても化学構造を変えずに再利用できるリサイクル可能な材料です。 射出成形の場合、熱可塑性樹脂は融点が比較的低いという利点があり、プラスチック部品の大規模製造に適しています。

* 熱可塑性樹脂は、一般に熱硬化性樹脂よりも高価です。
2. 材料選択時の考慮事項
プラスチック パーツに適した材料を見つけるには、逆に考えると役立つ場合があります。 次の質問に答える準備をしておいてください。部品は何に使用されますか? 部品にはどのような圧力がかかりますか? 彼らは過酷な環境で働いていますか? 組み立ては複雑ですか? 次の要因に優先順位を付けると、適切な材料を選択するのに役立ちます。
設置位置: 部品の取り付け位置は考慮しなければならない要素です。
太陽の下、屋外、湿度の高い環境、またはモジュールの内側または外側に設置されていますか?
温度: 部品は冷たい冷蔵庫、または室温やボンネットの下などの高温環境で動作しますか?
ライフサイクル: 部品の平均使用年数は5年ですか、10年ですか、それ以上ですか。
保証: 特に自動車業界では、数年後に部品が破損する可能性があることを考慮する必要があります。 修理費用はどのくらいかかりますか?
コストの制約: 高密度ポリエチレンやポリプロピレンなどの商用グレードのプラスチックは、通常、高密度で熱が低く、比較的安価です。 もう XNUMX つは、PEEK、PEI などのエンジニアリング プラスチックで、高温耐性があり、非常に硬いですが、コストが比較的高くなります。
外観要件: パーツに質感が必要かどうか、表面仕上げをどれだけ高くする必要があるか、透明なパーツよりも色付きのパーツの方が適しているかどうかなど。
最初の質問を理解したら、ほとんどの資料を除外できますが、資料をさらに絞り込むために、次の一連の質問を検討する必要があります。
デザイン機能: 部品の機械的特性を考えると、柔軟性、圧縮性、接着性などの機能が必要ですか? 引っ張り強度は必要ですか? 部品の耐衝撃性または電気絶縁要件は何ですか? 材料には、複数材料のオーバーモールディングやインサート モールディングなどの接着インサートが必要ですか? パーツの重量も重要な考慮事項です。
環境要因: 部品はどのような動作環境にさらされますか? 化学物質にさらされますか、難燃性が必要ですか、UV 要件は何ですか?
コンプライアンス: 一部の特定の業界では、パーツにマテリアル アクセスのしきい値が必要です。 あなたの部品には食品認証が必要ですか、それはFDAに準拠する必要がありますか? それとも、医療グレード、ISO、電気的コンプライアンスなどが必要ですか?
熱硬化性樹脂と熱可塑性樹脂の違い
熱硬化性ポリマー | 熱可塑性ポリマー |
加熱成形はXNUMX回のみ | 数回の加熱成形が可能 |
形成中に硬化し、加熱しても軟化しない | 加熱すると柔らかくなる(液化する場合もある) |
溶けません。 それらは高温に耐えることができます。 | 熱を加えると白くなり、冷やすと硬くなります。 |
安定するまで最大5分 | 10秒で安定する |
高い耐熱性と耐薬品性。 | 優れた機械的特性と容易な加工。 |
不溶 | 有機溶剤に不溶。 |
例: シリコーン、一部のタイプのポリエステルおよびフェノール材料。 | 例:ポリエチレン、ポリプロピレン、ポリスチレン、ポリ塩化ビニル。 |
3. 一般的に使用される熱可塑性材料の利点と用途
プロ 射出成形 工場は通常、数十種類のエンジニアリンググレードのプラスチックを在庫しており、顧客から要求されたより特殊な材料もサポートする必要があります。 中国の射出成形サプライヤーである DDPROTOTYPE が在庫している材料の在庫に基づいて、一般的に使用される熱可塑性樹脂の利点と用途がまとめられています。
①ABS(アクリロニトリルブタジエンスチレン)。
Advantages:ABSは、収縮が少なく、寸法が安定しており、耐酸性および耐アルカリ性に優れた、強靭で衝撃に強いプラスチックであり、さまざまな分野で広く使用されています。 この材料の価格は比較的安いです。
アプリケーション分野: 電子製品、リモコン、コンピューター、電話、化粧品、ハンドヘルド デバイス、筐体などを含みますが、これらに限定されません。
注意事項: ABS 製の射出成形部品にはウェルド ラインが見られ、厚みのある部分にくぼみやボイドがある場合があります。 幸いなことに、ABSはPCと混合でき、改善された材料は欠陥を大幅に解決できます。

②ABS/PC
Advantages:ABS/PCハイブリッド素材で、ポリカーボネートの強度と耐熱性と、ABSの柔軟性と寸法安定性を併せ持ち、機械的特性に優れた素材です。 ABSよりも耐熱性に優れた素材です。 低温では、この材料は PC よりも高い耐衝撃性を備えています。
アプリケーション: これらのハイブリッド材料は、自動車、電子機器、電気通信業界などで一般的です。
注意事項: ABS/PC材料は、肉厚成形の問題など、単一材料で成形する場合の欠点を最大化します。 優れた機械的特性を選択し、コストを削減したい場合は、このハイブリッド材料を選択できます。

③PC(ポリカーボネート)
Advantages: PC は透明なプラスチックで、光学的に透明なグレードで、強度が高く、耐衝撃性が非常に高く、収縮が少なく、寸法安定性に優れています。 さらに、PC は耐熱性が高く、機械加工された部品の表面仕上げは非常に高いです。
アプリケーション: レンズ、ライト、携帯電話の筐体、電子部品、医療機器、防弾ガラスなどを含みますが、これらに限定されません。
注意事項: PC はより厚い部品を作成し、ボイド、気泡、またはくぼみがある場合があります。 また、PC 部品の耐薬品性は比較的劣ります。 ABS/PC 混合材料は PC の優れた代替品であり、いくつかの欠陥を解決できますが、製造された部品は不透明です。

④PAまたはPPA(脂肪族ポリアミド)
Advantages: PAは優れた性能を持つエンジニアリングプラスチックです。 優れた機械的性質、優れた耐食性、耐油性、耐熱性などを備えており、強化や難燃化により耐熱性を大幅に向上させることができます。 特性、安定性および難燃性。 ナイロンには多くの種類があります (4、6/6、6、6/10、6/12、12 など)。 各素材には独自の利点があります。 ナイロンは強度と高温強度が高く、耐薬品性に優れています。 たとえば、ナイロン 6/6 は強度と硬度が高く、耐摩耗性に優れています。 ナイロン 6 は非常に硬く、低温では強靭です。 ナイロン 6/12 は耐衝撃性に優れています。
アプリケーション: 薄肉の部品、シャフト、ギアとベアリング、ネジ、ポンプ、ガイドなどを含みますが、これらに限定されません。
注意事項: ナイロンは変形しやすいのは周知の事実。 湿度の高い冷蔵庫内などの特定の環境では、通常、ナイロン部品は避けられます。 ナイロンは吸水性のある素材のため、パーツのサイズや構造の変化、破損の原因となります。

⑤POM(ポリオキシメチレン)
Advantages: 靭性、剛性、硬度、強度を備え、他のプラスチックに比べて非常に硬いです。 同時に、潤滑性と耐有機溶剤性に優れ、弾力性にも優れています。 したがって、このプラスチックはベアリング面やギアの製造に非常に適しています。
アプリケーション: ギア、ポンプ、インペラー、ブレード、コンベア チェーン、ファン、スイッチ コンポーネント、ボタン、ノブなどを含みますが、これらに限定されません。
注意事項: POM は収縮するため、部品を製造する際には肉厚を均一に設計する必要があります。 潤滑性があるため、塗装やコーティングが難しく、美的効果を得ることも困難です。

⑥PMMA(ポリメチルメタクリレート)
Advantages: アクリルとも呼ばれ、優れた光学特性、表面仕上げ、耐スクラッチ性、低収縮性を備えた透明なプラスチックでもあります。
応用: レンズ、ライトパイプ、レンズ、ランプシェード、光ファイバー、ロゴなどを含みますが、これらに限定されません。
注意事項: PMMA は比較的もろく、力を加えると割れやすく、耐薬品性に劣ります。

⑦PP(ポリプロピレン)
Advantages: PP は、良好な成形性、良好な表面剛性、耐スクラッチ性を備えています。 耐衝撃性、耐摩耗性、非常に靭性が高く、伸びがよく、耐酸性アルカリ性に優れた低コストのプラスチックです。
アプリケーション: ヒンジ、ファン、ボトルキャップ、医療用ピペットなどを含みますが、これらに限定されません。
注意事項: PPは低温で脆くなります。 より厚い部品を製造すると、エア ポケットが発生する可能性があり、収縮や反りの可能性もあります。

⑧PBT(ポリブチレンテレフタレート)
Advantages: PBTは、優れた靭性と耐疲労性、耐熱性、優れた耐候性、優れた電気特性、および低吸水性を備えた優れた性能を備えたエンジニアリング材料です。 強化および難燃性改質により、耐熱性、寸法安定性、および難燃性が大幅に向上します。 自動車に非常に適しており、電子部品に優れた電気特性を提供します。 中強度から高強度で、強靭で、燃料、油、脂肪、および多くの溶剤に対する耐性が高く、臭気を吸収しません。
応用: すべり軸受、歯車、グラインダー、掃除機に限らず、 ボタンなど
注意事項: PBT樹脂は反りやすく、薄肉部品への加工が困難です。

⑨PPSU(ポリフェニルサルホン)
Advantages: PPSUは高い靭性と耐熱性が特徴で、耐熱性と寸法安定性に優れた材料です。 また、耐放射線性と一定の耐酸および耐アルカリ性も備えています。
アプリケーション: 医療機器部品、滅菌トレイ、温水付属品、ソケットおよびコネクタなどに限定されません。
注意事項: より厚い部品の場合、PPSU はボイドや気泡を引き起こす可能性があります。 有機溶剤と炭化水素は、PPSU 材料に特定の腐食を引き起こします。 PPSU樹脂には、一般的に着色剤を添加することはできません。

⑩PEEK(ポリエーテルエーテルケトン)
Advantages: PEEK は、耐熱性、優れた耐薬品性、難燃性、優れた強度、寸法安定性のある材料であり、医療、航空宇宙、自動車産業で一般的に使用されています。
応用: ベアリングに限らず、ピストン部品やポンプ、絶縁電線など。
注意: PEEK は高性能材料であるため、コストが非常に高くなります。

⓫PEI(ポリエーテルイミド)
Advantages: PEEK と同様に、PEI は耐熱性と難燃性、優れた強度と寸法安定性、優れた耐薬品性を備えた材料です。 医療、航空宇宙、自動車産業で一般的に使用されています。
アプリケーション: 医療および化学機器に限定されません。 エアコン、パイプラインなど
注意: PEIも回転率の高い素材ですが、PEEKよりも安価です。

上記の11の材料は、射出成形で一般的に使用されています。 DDPROTOTYPE メモリには、PPS、TPE、TPU、LCP、HDPE、LDPE、PSU などの他のプラスチック オプションも含まれており、これらの樹脂はガラス繊維と炭素繊維を追加することで性能を向上させることもできます。
4. 医療用射出成形の代表的な材料
プラスチックは、医療用途では金属よりも優れていると長い間考えられてきました。 人体に接触すると、金属が人体の生理食塩水と化学反応を起こす可能性があるためです。 射出成形プロセスにおいて、医療業界は最高レベルの要件を持ち、大きな需要があります。 医療用射出成形部品の品質は、人の健康に関係し、人の命を脅かすことさえあります。 医療用射出成形メーカーと協力する場合、メーカーが医療用射出成形で最も一般的に使用される熱可塑性樹脂の特性を完全に理解することが非常に重要です。 以下に、医療用射出成形部品の一般的な材料と用途を紹介します。 通常、これらの医療材料は予備の在庫材料として使用されることはありませんが、製造前に厳密なテストを経て生産に使用する必要があります。

ポリエチレン(DPE)
世界で最も広く使用されているプラスチックであるポリエチレンは、非吸収性、非生分解性、耐色性を備えた費用対効果の高い医療グレードの素材であり、繊細な医療機器やコンポーネントに最適です。 ポリエチレンは危険なバクテリアを保持しにくく、強力な洗浄剤にも耐えることができます。 容器、ボトル、パイプなどに広く使用されていますが、紫外線に弱く、可燃性です。 引張強度は 4,000 psi です。
ポリプロピレン – 医療機器の射出成形に一般的に使用される熱可塑性樹脂。
ポリプロピレンは、優れた機械的特性と耐薬品性を備えた熱可塑性材料です。 ポリプロピレンは、4,800 psi の非常に高い引張強度を備え、比較的強く耐久性があり、自動車のバンパーから医療用具に至るまでの用途に使用されています。 ポリプロピレンは、使い捨て注射器、コネクター、ナックル プロテーゼ、非吸収性縫合糸、容器、バイアル、透明バッグなどの製造に一般的に使用されています。

ポリスチレン
ポリスチレンは、最も広く使用されているプラスチックの XNUMX つです。 これはガラス質で透明な硬質プラスチックで、比較的安価ですが、酸素と水蒸気に対するバリアが弱く、融点が比較的低いです。 ポリスチレンは、試験管、ペトリ皿、トレイ、使い捨てプラスチック食器などの製造に一般的に使用されています。

アクリル
PMMA は可視光をほぼ完全に透過し、光ビームをその表面内で反射させ続けるという珍しい特性を持っているため、光ファイバーの製造によく使用されます。 人工歯、歯科インプラント、義歯材料、歯科用充填剤、眼内レンズ、透析用膜を製造する医療機器でよく使用されます。

ポリ塩化ビニル
ポリ塩化ビニル (PVC) は、世界で最も一般的に使用されている熱可塑性ポリマーの XNUMX つです。 病院の無菌検査室の床材、配管、羽目板などの建設業界で最も一般的に使用されています。 場合によってはゴムの代用としても使用され、血液透析または血液灌流装置、血液チューブ、血液バッグ、補綴材料の製造にも一般的に使用されています。

ポリカーボネート – 医療機器の射出成形に一般的に使用される熱可塑性樹脂
ポリカーボネートは、可視光を自然に透過し、紫外線に強い熱可塑性ポリマーのグループです。 それらは眼鏡レンズで一般的に使用されており、ガラスの優れた代替品と見なされています。 ポリカーボネートは非常に丈夫な素材で、もろくなく、医療機器で一般的に使用されています。 ポリカーボネート製の部品は、120°C の蒸気、ガンマ線、またはエチレンオキシド (Eto) 法を使用して滅菌できます。
5. 信頼できる射出成形メーカーを探す
射出成形プロジェクトを製造業者に委託する場合、製造業者が一貫して期待に応え、プロジェクトに付加価値を与えることを期待します。 したがって、射出成形メーカーを探す方法を知る必要があります。
適切な射出成形認証。
射出成形業界には、特に医療などの特殊な業界向けの厳格なガイドラインがあります。


設計および製作資格:
メーカーの機器が IQ/OQ/PQ プロセス検証の品質基準を満たしていることは非常に重要です。 また、SolidWorks CAD などの設計ソフトウェアを使用することは、彼らのプロトタイピング能力を決定する重要なパフォーマンスです。
品質管理と評価の認証
メーカーにとって、ISO 9001:2015 は、適切な品質管理システムを意味する重要な認証です。
材料の安全性と調達の認証
特に医療分野では、トレーサビリティが非常に重要です。 メーカーの生産記録が、関連する法的および倫理的制約に完全に準拠していることを確認してください。
メーカーの品質管理レベル
射出成形には非常に高い安定性が求められるため、製造プロセス全体を通じてサプライヤーが品質管理と安全対策を実施していることを確認してください。 さまざまな熱可塑性部品を製造するための実践的なソリューションについては、工場をチェックしてください。 彼らが実践の具体例を説明しているのを聞くのは賢明です。
社内製造設備とプロのメカニック
社内の高度な製造設備と機械工は、高品質を実現し、生産の期待に応えるための重要な基盤です。 5軸CNC工作機械、三次元測定器等が必要条件です。 もちろん、経験豊富なメカニックが開発段階全体をフォローする必要があります。
射出成形材料の選定でお困りのことがございましたら、お気軽にお問い合わせください DDプロトタイプ すぐに、20 年以上の経験に基づいて無料でアドバイスします。