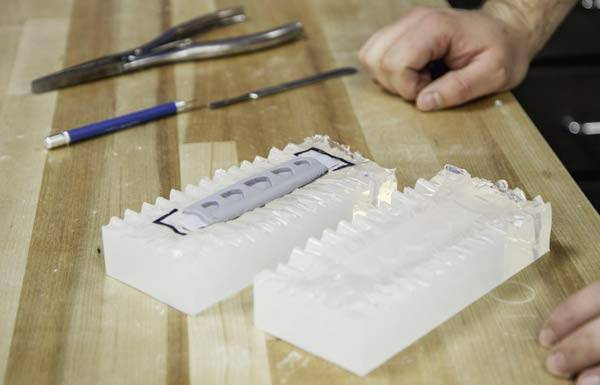
Эксперт по быстрому прототипированию и быстрому производству
Специализируется на обработке с ЧПУ, 3D-печати, литье уретана, быстрой оснастке, литье под давлением, литье металла, листовом металле и экструзии.
Все, что вы должны знать о вакуумном литье
вакуумное литье является одним из важных процессов изготовления прототипов. Он имеет преимущества низкой стоимости и стабильного качества продукции. Он очень подходит для быстрого инженерного тестирования (быстрого тестирования проектов), проверки концепции дизайна и физического отображения (отображения физической структуры продукта). Подождите. Прежде чем перейти от концепции или идеи к массовому производству, дизайнеры должны постоянно выявлять проблемы и улучшать планирование продукта; многие промышленные пластиковые детали, такие как автозапчасти, роботы, медицинские устройства и продукты 3C, обычно используют процесс литья под давлением. Производятся миллионы единиц, но стоимость открытия пресс-формы очень высока, а время разработки пресс-формы относительно велико. (и цикл проектирования и производства пресс-формы длительный). Что усложняет задачу для дизайнеров, так это то, что если в плане есть небольшой недостаток, это приведет к огромным потерям (стоимость модификации пресс-формы довольно высока). Вы должны знать, что комплект металлоформ обычно стоит 10,000 20, а то и десятки тысяч долларов, и затраты времени не могут быть компенсированы. Поэтому важным шагом является производство небольших партий пластиковых деталей для проверки конструкции, например, 500-XNUMX штук. В настоящее время вакуумное литье является предпочтительным методом обработки.

Что такое вакуумное литье?
вакуумное литье, также известное как силиконовая форма, использует изготовленную силиконовую форму для воспроизведения пластиковых деталей. Отлитый полиуретановый материал вспенивают, перемешивают, предварительно нагревают и заливают в условиях вакуума, а процесс формования вторичного отверждения проводят в термостате при температуре 60°С-80°С в течение 2-3 часов. Реплика из силиконовой композитной формы может достигать прочности и твердости ABS и других материалов, а также может быть окрашена в соответствии с требованиями. Процесс вакуумного литья позволяет изготавливать небольшие партии пластиковых деталей сложной конструкции, с одинаковой толщиной стенок и определенными функциями и внешним видом.

Производственный процесс вакуумного литья
Производственный процесс вакуумного литья делится на три этапа: изготовление прототипа основной формы, изготовление формы и заливка деталей.
Шаг 1: Прототип мастер-формы
Вы можете выбрать любой материал со стабильными характеристиками для изготовления прототипа основной пресс-формы. Обычно изготавливается из пластика или металла. Единственное требование состоит в том, что этот материал должен быть стабильным в течение определенного периода времени при высокой температуре 40°C.
Стоит отметить, что прототип играет решающую роль в качестве копируемых деталей. Если вы хотите обрабатывать высокоточные, блестящие или даже высокопрозрачные пластиковые детали, то прототип мастер-формы лучше всего обрабатывать с помощью станков с ЧПУ.
Это также идеальный выбор для изготовления прототипа мастер-модели с помощью процесса SLA, но по сравнению с прототипом мастер-модели, обработанным с помощью ЧПУ, стоимость конечной детали может сильно отличаться (точность будет немного хуже, а цена за единицу будет меньше). быть чуть ниже); это когда при выборе процесса вакуумного литья для изготовления деталей котировки разных производителей будут сильно отличаться, даже в несколько раз (одна из причин, почему котировки разных производителей разные).
Поверхность прототипа основной модели также может быть выполнена с текстурой спрея или с матовым эффектом. Силиконовая форма точно воспроизведет детали и текстуры, а поверхность окончательной копии сохранит высокую степень согласованности с прототипом.
Шаг 2: Сделайте силиконовую форму
Форма для заливки изготовлена из жидкого силикона, также известного как форма RTV. Силикон химически стабилен, самоотделяющийся и гибкий, сводит к минимуму усадку и эффективно воспроизводит детали деталей от прототипа до формы. Равномерно перемешайте силикагель и отвердитель. Внешний вид силикагеля формы представляет собой текущую жидкость, компонент А представляет собой силикагель, а компонент В представляет собой отвердитель. Пример: возьмите 100 грамм силикагеля и добавьте 2 грамма отвердителя (Примечание: силикагель и отвердитель необходимо перемешать равномерно. Если их перемешать неравномерно, одна часть формы затвердеет, а другая не отверждение, и силикон будет отвержден неравномерно, что повлияет на срок службы силиконовой формы и количество раз переворачивания формы, и даже приведет к тому, что форма будет утилизирована.
Нанесите ленту на плоские места вокруг прототипа, чтобы сформировать поверхность разъема после последующей резки формы. Затем прототип подвешивается в литейной коробке, а на детали наклеиваются клеевые стержни, чтобы образовались литники и вентиляционные отверстия для вентиляции во время процесса формования силикона. Налейте силикагель в коробку, а затем удалите пузырьки воздуха. Время не должно быть слишком большим. В нормальных условиях это не должно превышать десяти минут, чтобы предотвратить невозможность чистки кистью или заливки после того, как происходят реакции сшивания.
Поместите литейную коробку в печь для отверждения, температура 40 ℃, время 8-16 часов, это время зависит от объема формы.
После отверждения силиконовой резины снимите коробку и клей-карандаш, разрежьте по линии разъема и извлеките прототип. В это время силиконовый каучук образует полость точно такой же формы, как у прототипа; Таким образом, силиконовая форма может быть успешной.
Шаг 3: Вакуумное литье
Поставить форму в духовку для застывания и разогреть до 60-70℃.
Выберите подходящий разделительный состав и правильно используйте его перед закрытием формы, что очень важно во избежание прилипания и дефектов поверхности.
Подготовьте полиуретановую смолу в соответствии с вашими требованиями к дизайну, смешайте двухкомпонентную смолу в правильном соотношении, затем полностью перемешайте и дегазируйте под вакуумом в течение 50-60 секунд и предварительно нагрейте ее до температуры около 40°C перед использованием.
Залейте полиуретановую смолу в полость формы. После того, как полость заполнена, поместите форму в вакуумную среду, чтобы удалить воздух из полости, и заполните каждую позицию формы жидким силиконом, чтобы убедиться, что форма формованного изделия точно такая же, как у прототипа.
Продолжайте ставить форму в духовку, чтобы снова вылечить. Среднее время отверждения: 1-3 часа для мелких деталей, 3-6 часов для крупных.
После отверждения выньте отлитую деталь из силиконовой формы, и вы сможете получить точную копию оригинальной детали.
Повторите этот цикл.
Выбор материала для вакуумного литья
полиуретан смолы представляют собой полимеры с широким спектром свойств и областей применения. Производители вакуумных отливок используют полиуретановые смолы, в том числе Hei-Cast из Японии и Axson из Франции. Свойства материала аналогичны конструкционным пластмассам, таким как АБС, ПММА, ПК, ПП, ПА и т. д. Типы литейных смол могут варьироваться от прозрачных, полупрозрачных до цветных, мягких резиновых или твердых пластиков и даже ударопрочных, высокопрочных. -термостойкие (120°C) или огнестойкие (UL94-V0) материалы. процесс вакуумного литья может использоваться для вторичного литья под давлением, а также могут быть добавлены вставки;
Технические параметры вакуумного литья
Описание | Примечание о допуске |
точность | Из-за теплового расширения жидкости и естественных свойств гибкой формы ожидаемая степень усадки составляет +0.15%; стандартный допуск составляет ±0.15 мм/100 мм, а максимальная точность может достигать ±0.05 мм. |
максимальный размер | Оборудование для вакуумной заливки может вместить максимальный размер 2d,0 м * 1.2 м * 1.0 м. |
Минимальная толщина стенки детали | Для обеспечения адекватного заполнения формы необходима толщина стенки не менее 0.75 мм. Для достижения наилучших результатов мы рекомендуем толщину стенки не менее 1.5 мм. |
Типичное количество реплик | До 25 копий на форму (в зависимости от сложности формы и материала отливки); для пресс-формы можно изготовить только 12 или даже 10 копий, если деталь требует высокого качества (например, прозрачные или сложные структуры). |
Типичные сроки выполнения | В зависимости от размера и объема детали можно изготовить до 50 литых образцов в течение 10–15 дней. |
Варианты отделки для вакуумного формования
Матовый/матовый.Мастер-прототип имеет матовую пескоструйную обработку, реплика имеет гладкую атласную поверхность, а прозрачные и полупрозрачные детали с такой отделкой будут казаться матовыми. Матовое покрытие полезно для рук и областей с частым касанием, так как оно снижает видимость отпечатков пальцев.
Полуглянцевая. Отделка с некоторым блеском, но не очень отражающая. Полуглянцевое покрытие находится между глянцевым и матовым, с гладкой, легко очищаемой поверхностью.
Глянцевый. Создайте высокоотражающую поверхность, отполировав мастер-прототип перед изготовлением формы. Имеет самую высокую прозрачность для прозрачных частей. Specular можно использовать для косметических моделей, линз и многого другого.
Полиуретан можно смешивать с пигментами для получения различных цветов. Черный, натуральный, прозрачный и различные пользовательские цвета (цвета Raoul или Pantone, наиболее близкие к вашему выбору).



Преимущества вакуумного литья
Быстрый оборот. До 50 деталей могут быть доставлены за 7-15 дней или меньше, в зависимости от спецификации детали (размер, конструкция) и количества. По сравнению с литьем под давлением время производства вакуумного литья короче. Изготовление традиционных форм для литья под давлением занимает от 4 до 8 недель. В то время как для полной сборки силиконовой формы требуется всего 1-2 недели, а все сложные детали можно изготовить за короткое время.
Бюджетный. Силикон дешевле с точки зрения стоимости по сравнению с формами для литья под давлением. Литье под давлением основано на изготовлении из стали или алюминия. Стоимость силиконовой формы может составлять от сотен до тысяч, а стоимость одной литьевой формы – от тысяч до десятков тысяч.
Возможность изготовления крупных деталей. В зависимости от типа используемого оборудования вакуумное литье может создавать очень большие детали, такие как автомобильные корпуса, большие роботизированные корпуса, медицинские корпуса компьютерной томографии и т. д.
Поверхностная обработка лучше, чем литье под давлением. Процесс вакуумирования удаляет пузырьки воздуха и позволяет материалу полностью сцепиться с полостью, захватывая детали.
вакуумное литье может реализовать требуемое сложные детали или конструкции за один раз, в то время как обработку с ЧПУ в большинстве случаев необходимо разделить и производить в соответствии с размером и структурой.
Различные цвета на выбор. В смолу можно добавлять красящие пигменты для получения различных цветовых вариантов.
Повторяемость. Силиконовую форму можно использовать около 20 раз, прежде чем ее нужно будет заменить.
Применение вакуумного литья
Подходит для мелкосерийного производства. Вакуумное двойное формование идеально подходит для небольших партий, когда количество оказывается недостаточным для инвестиций в литьевые формы, а также для производства деталей первой партии (первый выпуск), которое может быть завершено за несколько недель до того, как будут готовы производственные формы.
Процесс вакуумного литья относительно дешев., делая любые необходимые изменения конструкции простыми и экономичными. Кроме того, для одной и той же формы можно использовать разные материалы, что позволяет тестировать конструкции с несколькими материалами.
Тестирование рынка. Высококачественная отделка делает детали, отлитые под вакуумом, идеальными для потребительских испытаний, оценки пользователями и создания концептуальных моделей. В соответствии с той же концепцией дизайна, если вы не знаете, какой цвет лучше всего подходит для продукта, вы можете сделать силиконовую форму, сделать 10-15 отливок и на каждой отливке нарисовать цвет и текстуру вашего дизайна, чтобы он мог использоваться в отделе проектирования Даже внутренние обсуждения на собраниях руководства позволяют быстро адаптировать изменения для дальнейшего тестирования или выхода на рынок.
В августе 2021 года производитель велосипедов в США хотел произвести 50 крышек задних фонарей с обычной ромбовидной текстурой, причем детали должны были быть прозрачными. С учетом бюджетной стоимости, процесс вакуумного литья было рекомендовано, а постобработка отполирована; профессионалом Промежуточная команда проверяет продукт, а заказчик превосходит ожидания после получения деталей прототипа; Вывод: сложные детали пресс-формы могут точно воспроизводить структуру, детали и текстуру прототипа и обеспечивать такую же чистоту поверхности, что и прототип, достигая аналогичного литья под давлением результата производства.