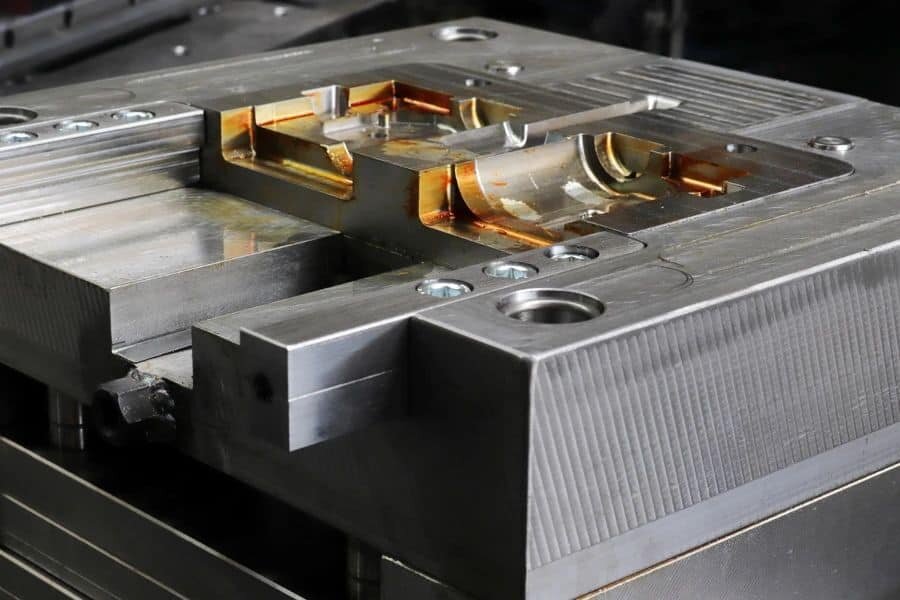
ラピッド プロトタイピング & ラピッド マニュファクチャリング エキスパート
CNC 機械加工、3D 印刷、ウレタン鋳造、ラピッド ツーリング、射出成形、金属鋳造、板金、押出成形を専門としています
射出成形とダイカストの違い
射出成形
射出成形は、非常に一般的な製造プロセスです。 主な理由は、金属、ガラスを含むさまざまな材料と互換性があるためですが、最も一般的なのはプラスチック、特に熱可塑性プラスチックであり、したがって、さまざまな製品を製造できます。 射出成形は、プラスチック射出成形と金属射出成形に分けることができます。

プラスチック射出成形 (PIM)
金型を射出成形機に取り付け、すべてのキャビティが充填されるまで高圧を使用して、液化溶融プラスチックを金型に射出します。 冷却後、部品を機械から取り外すことができます。 プロセスはプラスチック射出成形です。
射出成形の利点
複雑な幾何学的特徴を持つ部品を製造する能力
ラピッドプロトタイピング
繰り返し使用できます
材料の無駄がほとんどない
部品あたりの低コスト
厳しい公差を実現
さまざまなプラスチック材料と互換性があり、ソフト、タフ、または高強度パーツのカスタム選択
優れた表面仕上げ
射出成形の欠点
金型代が高い。
原材料費が高いかも
射出成形機と金型のサイズの制限により、小さな部品の作成に特に適しています。 大きな部品の場合、複数の部品が必要になり、組み立てに時間がかかり、コストがかかる場合があります。
複雑な部品の場合、リードタイムが長くなる場合があります
完成した金型、特に鋼の金型を修正することは非常に困難です。部品を製造する前に、いくつかの調整とテストが必要です。
一般的なプラスチック射出成形材料
プラスチック射出成形は、熱硬化性プラスチックおよび熱可塑性プラスチックと互換性があります。 より一般的な材料は次のとおりです。
ナイロン
ポリカーボネート
アクリル繊維
ポリスチレン
ポリオキシメチレン(POM)
ポリプロピレン(PP)
アクリロニトリルブタジエンスチレン(ABS)
熱可塑性ポリウレタン (TPU)
ポリエチレン(PE)
熱可塑性ゴム (TPR)
セルコン®(アセタール)
耐衝撃性ポリスチレン (HIPS)
低密度ポリエチレン(LDPE)
金属射出成形(MIM)
粉末金属とバインダー(ワックス、熱可塑性ポリマーまたはその他のバインダー)を混合し、得られた混合物を金属射出成形の「原料」として使用します。 混合物を高圧で金型に流し込み、冷却固化させて金属部品を成形します。 さらに、追加の洗浄と脱脂が必要で、熱処理後、結合剤を完全に除去すると、最終的な金属部品が得られます。

金属射出成形の利点
金属射出成形により、強度と耐摩耗性に優れた部品を製造できます
複雑で薄肉 (例: 0.1mm) の金属部品の製造
繰り返し使用
最終製品は追加の仕上げを必要としません
材料の無駄を最小限に
金属射出成形の欠点
大型部品 (例: 100 グラム以上) の製造コストが高くなる
プロの技術が必要な機械操作
脱脂または焼結の段階で、部品には一定の収縮率があります。
金型寿命が比較的短い(150K~300K回)
金属射出成形の一般的な材料は次のとおりです。 ステンレス鋼、チタン、ニッケル、タングステン、銅、その他のさまざまな組み合わせなど。
ダイカスト
ダイカストの製造プロセスは射出成形に似ています。選択される材料は溶融金属であり、プラスチックや粉末金属の混合物ではありません。
ダイカストのメリット
全自動ライン
低価格
部品の機械的特性の向上
デメリット
完成品には通常、気孔があります
パーツの質が比較的悪い
金型代が高い
ダイカストの一般的な材料: アルミニウム、亜鉛、銅、マグネシウム、鉛、その他の金属およびその他の合金。
ここでは、プラスチック射出成形がプラスチック部品を作る方法であることがわかります。 金属射出成形とダイカストは、金属部品を作るための技術です。 プラスチック部品の製造を計画している場合は、プラスチック射出成形を使用してください。 金属部品の製造を計画している場合は、金属射出成形とダイカストを比較するとより有益です。

金属射出成形 VS ダイカスト
どちらの工程も高品質な部品を生産できるのですが、両者には大きな違いがありますので、一つ一つ比較してみましょう。
薄肉部品
金属射出成形では、厳密なパラメータに従って薄肉部品を製造できますが、ダイカストでは、部品の壁の厚さと気孔率を制御できません。 したがって、ダイカストは薄肉部品の製造には適していません。
気孔
熱処理後、金属射出成形で製造された部品は、引張強度が高く、均一で緻密な構造を持っています。 ダイカストで作られた部品の内部構造には、通常気孔率と呼ばれる特定の空気の空洞があります。
金型寿命
高圧と高温の溶融金属に耐える必要がありますが、ダイカスト金型は 150 万ショット、金属射出成形金型は約 300k ~ XNUMXk の再利用が可能です。
製品収縮
通常、金属射出成形部品は熱処理後に 30% も収縮するため、収縮を正確に計算する必要があります。 ダイカスト部品は製品収縮の問題がありません。
費用
金属射出成形はダイカストよりも強度の高い部品を製造でき、材料の無駄を避けることができますが、金属射出成形はダイカストよりも 20% ~ 30% 高価です。 このコストの違いは、主に選択した材料の種類によって異なります。 さらに、ダイカストは人件費を削減する自動ラインを実現できます。
自動化と製品設計
金属射出成形では、複雑な構造の部品を製造できます。 これはダイカストにとってより困難です。
材料の無駄
材料の無駄がほとんどまたはまったくない金属射出成形。材料は、設定されたパラメータに従って金型に射出されます。 ダイキャスト製のパーツは余分なパーツを取り除く必要があり、ある程度の無駄があります。
金属部品を製造するためにどのプロセスを選択するか
ダイカストよりも金属射出成形の方が有利に見えるが、そうは判断できない。 それは現実を思いつくはずです。 金属部品を製造するためにどのプロセスを選択するかは、業界の目標によって異なります。 エンジンケーシング、大型コンテナなどの大型部品を製造したい場合は、ダイカストが理想的な選択肢かもしれません。 プロセスが複雑すぎず、原材料のコストが比較的低いためです。
複雑で小さな金属部品の製造を計画している場合、金属射出成形は時間とリソースを節約する理想的な製造プロセスです。 ダイカストでは非常に複雑な金属部品を作ることはできません。
まとめ
金属射出成形は新しい技術です。 小さく複雑な機能が必要な部品の大量生産には、より費用対効果が高くなります。
ダイカストは、より大きく単純な構造の部品を大量に製造する場合に、より収益性が高くなります。
それでも最適な製造プロセスを判断できない場合は、中国のトップ メーカーである DDPROTOTYPE にお気軽にお問い合わせください。設計図面を厳密に検討および最適化し、最も実現可能なソリューションを提案します。