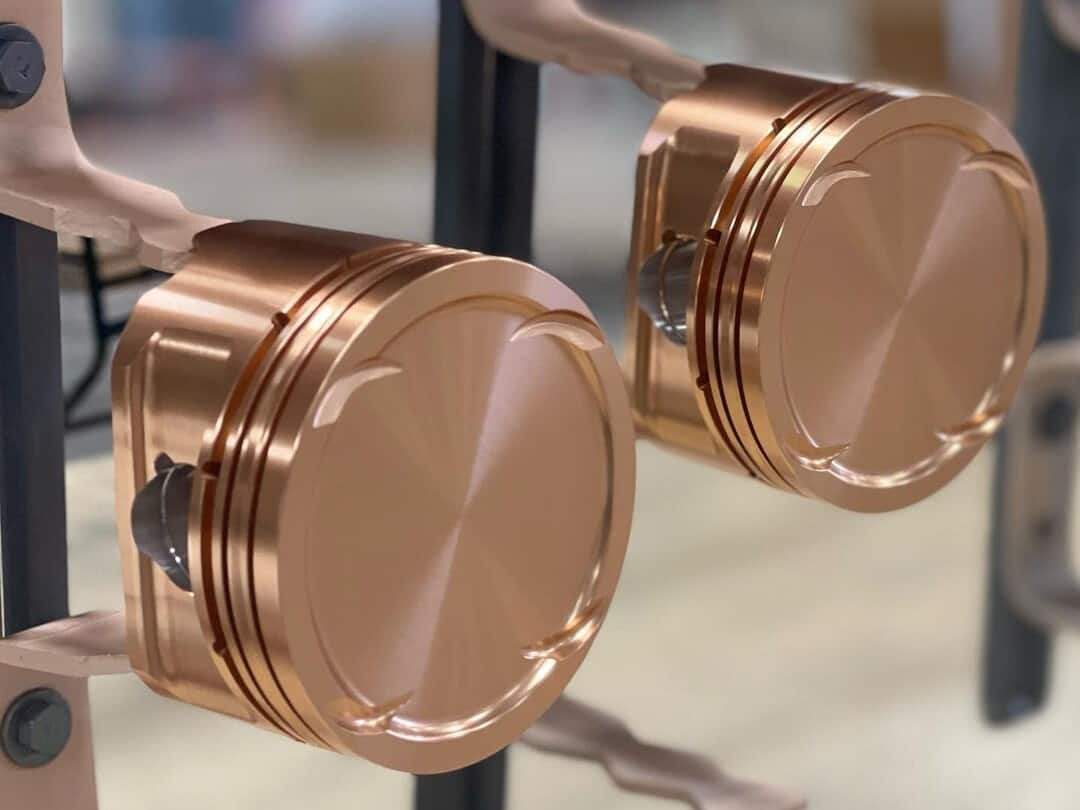
알루미늄 부품의 아노다이징 비용에 영향을 미치는 요인
알루미늄 합금은 저밀도, 고강도, 우수한 연성, 우수한 전기 전도성, 강한 내식성 및 용이한 성형과 같은 우수한 물리적 및 화학적 특성으로 인해 철강 다음으로 큰 유형의 금속 재료가 되었습니다. 특히 알루미늄 프로토타입을 제작하기 위해 CNC 가공 기술을 사용하는 것이 널리 주목받고 있습니다. 맞춤형 알루미늄 부품은 아노다이징, 마이크로아크 산화, 전기도금, 도장(분체도장 또는 도장) 등의 다양한 표면처리가 있으며 가장 널리 사용되는 공정은 아노다이징입니다. 오늘은 아노다이징에 대한 지식과 비용에 영향을 미치는 요인에 대해 논의해 보겠습니다. 아노다이징 알루미늄 부품을 절단하고 마킹합니다.
아노다이징이란 무엇이며 그 효과
아노다이징 공정은 금속 또는 합금 부품을 양극으로 사용하고 전기 분해 방법을 사용하여 표면에 산화 피막을 형성하는 것입니다. 금속 산화물 피막은 표면 착색과 같은 표면 상태 및 특성을 변경하고, 내식성을 개선하고, 내마모성 및 경도를 향상시키고, 금속 표면을 보호합니다. 알루미늄 및 알루미늄 합금의 아노다이징, 알루미늄 및 알루미늄 합금을 해당 전해질(예: 황산, 크롬산, 옥살산 등)에 양극으로 놓고 특정 조건 및 적용된 작용에서 전기분해가 수행됩니다. 현재의. 양극의 알루미늄 또는 알루미늄 합금의 산화 된 표면에 산화 알루미늄의 얇은 층이 형성되고 그 두께는 50-30 미크론이며 경질 양극 산화 피막은 약 25-150 미크론에 도달 할 수 있습니다. 알루미늄 및 알루미늄 합금은 아노다이징 처리 후 경도 및 내마모성이 향상되었으며 얇은 산화 피막에 많은 수의 미세 기공이있어 다양한 윤활제를 흡수 할 수 있으며 엔진 실린더 또는 기타 내마모성 부품 제조에 적합합니다. ; 흡착력이 강한 얇은 산화막의 미세 기공은 다양한 색상으로 아름답고 화려한 색상을 낼 수 있습니다. 비철금속 또는 그 합금(알루미늄, 마그네슘 및 그 합금 등)은 양극산화 처리할 수 있습니다. 이 방법은 기계 부품, 항공기 및 자동차 부품, 정밀 기기 및 무선 장비, 일용품 및 건축 장식에 널리 사용됩니다.
부식 저항. 아노다이징으로 얻은 필름층은 대기 중에서 충분한 안정성을 가지므로 산화피막을 알루미늄 부품의 부식방지 보호층으로 사용할 수 있다. 크롬산 용액에서 양극 산화 처리하여 얻은 알루미늄의 산화 피막은 내식성이 우수하고 산화 피막의 미세 기공이 미세합니다. 황산 용액에서 얻은 산화 피막은 전자보다 미세 기공이 더 크지 만 피막 층이 더 두껍고 강한 흡착력을 가지며 적절한 충진 및 밀봉 처리 후 내식성도 매우 좋습니다. 크롬산 아노다이징 방법은 리벳 부품 및 용접 부품의 아노다이징 처리에 특히 적합합니다.

장식. 아노다이징은 다양한 유기 염료와 무기 염료를 흡수하여 알루미늄 부품에 다양한 밝은 색상을 부여합니다. 일부 특수 공정 조건에서 보호 및 장식용 산화 피막을 얻을 수 있으며 도자기 외관과 유사합니다.
내마모성. 경질 아노다이징 알루미늄 및 알루미늄 합금을 통해 표면에 두껍고 단단한 산화막을 얻을 수 있습니다. 황산 또는 옥살산 용액에서 양극 산화 처리하여 알루미늄 부품에 단단하고 두꺼운 산화 피막을 얻을 수도 있습니다. 예를 들어, 자동차 및 트랙터의 엔진 실린더 및 피스톤은 아노다이징 처리 후 내마모성을 크게 향상시킬 수 있습니다.
단열재. 아노다이징으로 얻은 알루미늄 및 알루미늄 합금의 산화 피막은 저항이 크므로 알루미늄 부품의 전기 절연성 향상에 일정한 효과가 있습니다. 양극 산화는 커패시터의 유전체 층을 준비하는 데 사용할 수 있으며 산화 알루미늄은 표면에 대한 절연 층을 준비합니다.
도장 및 전기도금용 프라이머. 양극 산화 피막의 다공성과 우수한 흡착력으로 인해 스프레이 페인트 및 기타 유기 필름의 바닥층으로 사용할 수 있으므로 페인트 필름과 유기 필름이 부품과 단단히 결합되어 내식성이 향상됩니다. . 알루미늄 및 알루미늄 합금 부품을 전기도금하기 전에 전기도금 전에 프라이머 층을 도포해야 합니다. 기판 표면에 바닥층을 적용하는 방법에는 여러 가지가 있습니다. 전기아연도금, 아연침지, 무전해니켈도금 외에 아노다이징 처리도 중요한 방법 중 하나이다.



양극산화피막의 제조공정
알루미늄 합금 아노다이징의 일반적인 프로세스에는 크롬산 아노다이징 프로세스, 황산 아노다이징 프로세스, 옥살산 아노다이징 프로세스 및 인산 아노다이징 프로세스가 포함됩니다. 다른 전해질을 사용하는 경우, 얻어진 산화막은 외관과 특성에 큰 차이가 있습니다. 실제 제조에서는 사용 목적에 따라 적절한 아노다이징 공정을 선택하는 것이 필요합니다.
황산 아노다이징 공정. 현재 세계에서 가장 널리 사용되는 아노다이징 공정은 황산 아노다이징입니다. 황산 아노다이징 공정은 간단하고 작업 시간이 짧고 생산 작업을 마스터하기 쉽고 필름 투명도가 높으며 내식성 및 내마모성이 좋습니다. 다른 산성 아노다이징과 비교하여 다양한 측면에서 분명한 장점이 있습니다. 황산 아노다이징의 공정 흐름은 연마 → 탈지 → XNUMX회 세정 → 화학 연마 또는 전해 연마 → XNUMX회 세정 → 아노다이징 → XNUMX회 세정 → 염색입니다. 알루미늄 부품이 더 높은 전압과 강한 황산을 아노다이징에 사용하는 경우 이를 "경질" 아노다이징이라고 하며 심하게 마모된 부품을 만드는 데 이상적인 옵션입니다.

크롬산 아노다이징. 크롬산 아노다이징 공정은 1923년 Bengough와 Staurt에 의해 처음 개발되었습니다(줄여서 BS 방법). 크롬산 아노다이징으로 얻은 산화 피막은 비교적 얇고 일반적으로 두께가 2-5μm에 불과하여 부품의 원래 정밀도와 표면 거칠기를 유지할 수 있으며 "경량"형 아노다이징이라고합니다. 산화 피막은 부드럽고 내마모성은 황산 산화 피막만큼 좋지 않지만 탄성이 좋습니다. 또한, 필름층은 불투명하고 공극률이 낮아 염색이 어렵고 밀봉 없이 바로 사용할 수 있다. 알루미늄 합금에 대한 크롬산 용액의 낮은 용해도는 핀홀 및 틈새에 잔류하는 용액을 구성 요소의 부식에 거의 영향을 미치지 않게 합니다. 주물, 리벳 부품 및 기계 가공의 표면 처리에 사용됩니다.

옥살산 아노다이징. 옥살산 아노다이징 공정은 1938년부터 일본과 독일에서 널리 사용되었습니다. 알루미늄 및 알루미늄 합금에 대한 옥살산의 용해도가 작고 산화 피막의 다공성이 낮아 내식성, 내마모성 및 전기 절연성 필름의 황산 필름보다 낫다. 그러나 옥살산 양극 산화의 비용은 일반적으로 황산 양극 산화의 3-5 배이며 비용이 많이 듭니다. 옥살산 산화 피막의 색상은 공정 조건의 변화에 따라 쉽게 변하여 제품의 색상 불일치가 발생하므로이 공정은 적용 범위가 제한적이며 일반적으로 전기 절연층을 만드는 것과 같은 특별한 요구 사항에서만 사용됩니다. .
인산 아노다이징. 인산 아노다이징은 알루미늄 도금의 전처리 공정으로 처음 사용되었습니다. 산화막은 황산보다 인산 전해질에 더 많이 용해되기 때문에 인산막은 얇고(두께 약 3㎛) 기공 크기가 크다. 인산 필름은 내수성이 강하기 때문에 주로 인쇄 된 금속판의 표면 처리 및 알루미늄 공작물 접합의 전처리에 사용됩니다.
아노다이징은 알루미늄 및 알루미늄 합금에 더 나은 내식성, 내마모성, 장식 특성 및 전기 절연성을 부여하며 현재 알루미늄 및 알루미늄 합금에 가장 널리 사용되는 표면 처리 기술입니다. 과학 기술의 발전으로 환경 보호의 개념을 따르거나 양극 산화 피막의 한 측면의 성능을 향상 시키거나 생산 비용을 줄이기 위해 양극 산화 피막은 점차 전통적인 산성 양극 산화 피막에서 발전했습니다. 혼합 산 양극 산화 피막.
알루미늄 아노다이징 비용에 영향을 미치는 요인
산화막의 두께. 산화층의 두께는 알루미늄 부품을 아노다이징하는 비용의 주요 요인입니다. 표준 두께의 산화막이 가장 저렴합니다. 대부분의 사람들은 산화피막이 두꺼울수록 아노다이징 비용이 높아진다고 생각합니다. 실제로 산화막이 얇을수록 가격이 높아집니다. 예를 들어, +/- .001"은 +/- .0001"보다 저렴합니다. 두꺼운 산화막이 얇은 산화막보다 제어하기 쉽기 때문입니다.
아노다이징 공정의 유형. 위에서 우리는 4가지 유형의 아노다이징 공정을 소개했으며, 각 유형은 아노다이징된 알루미늄의 비용에 상당한 영향을 미칩니다. 네 가지 유형 중 크롬산 아노다이징 공정이 가장 저렴합니다. 크롬산과 같이 사용하는 재료가 저렴하고 에너지 소모가 적기 때문이다. 황산으로 아노다이징하면 경질 아노다이징 알루미늄 생산 가격이 높아집니다.
부품의 크기입니다. 부품의 크기는 양극 산화 처리 비용의 중요한 요소입니다. 알루미늄 부품. 크기가 클수록 부품의 표면적이 커집니다. 이는 필요한 재료와 설비가 증가해야 함을 의미합니다. 또한 부품의 크기가 커지면 노동력과 시간이 증가할 뿐만 아니라 비용도 증가하게 됩니다.



아노다이징은 전해 공정이며 알루미늄 부품의 성능을 향상시키기 위한 이상적인 옵션입니다. 사실 알루미늄 부품의 아노다이징은 간단한 공정으로 저장탱크, 화학약품, 안정적인 고전압 전기 등 필요한 장비만 있으면 집에서 알루미늄을 아노다이징할 수 있다. 그러나 고품질과 미적 외관을 추구하려면 전문 양극 산화 알루미늄 공급 업체를 고려하는 것이 가장 좋습니다.