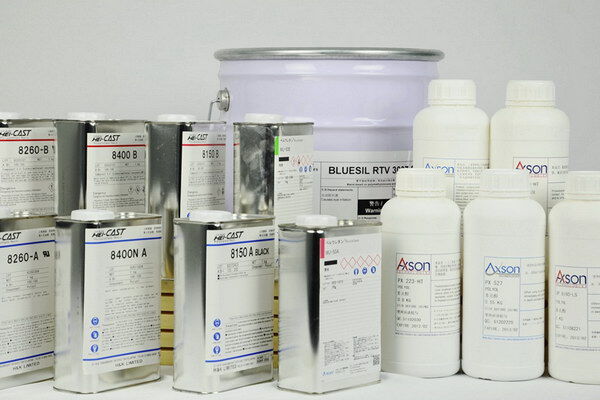
ラピッド プロトタイピング & ラピッド マニュファクチャリング エキスパート
CNC 機械加工、3D 印刷、ウレタン鋳造、ラピッド ツーリング、射出成形、金属鋳造、板金、押出成形を専門としています
真空鋳造と射出成形のどちらがプラスチック部品プロジェクトに適していますか?
プラスチック部品の成形プロセスは XNUMX 種類以上ありますが、さまざまな新規プロジェクトの開発や部品の大量生産で一般的なプロセスは、真空鋳造と射出成形です。 両工程の共通点は、金型に原材料を注入して部品を製造することです。 どちらのプロセスにも独自の長所と短所がありますが、最適なプロセスを選択する方法は、部品のニーズやその他のさまざまな要因によって異なります。
真空鋳造とは何ですか?
真空鋳造 ポリウレタンキャスティングと呼ばれることもあります。 ポリウレタン樹脂は、脱ガス、撹拌、予熱、真空条件下での注入、およびその後、2℃~3℃の恒温槽内で 60 ~ 80 時間硬化されます。 真空鋳造は、製品開発の初期段階における構造的および機能的なプロトタイプ、設計と機能の検証、新製品のテスト、初期の市場調査、少量生産に適しています。 真空鋳造は、金型製作のコストを大幅に節約し、製品開発サイクルを短縮し、家電、医療、自動車製造、航空宇宙などのさまざまな分野でも広く使用されています。

真空鋳造のワークフロー:
1: CNC 機械加工または 3D 印刷を使用して 1:1 のマスター パーツを製造し、マスター パーツを密閉ボックスに固定し、液体シリコン材料を注ぎ、焼成して硬化します。 シリコンが固まったら半分に切ってマスターパーツを取り出します。 残りのキャビティはシリコン型で、次のステップはパーツのコピーです。
2: シリコン型を予熱します。 シリコンモールドを60~70℃に予熱します。 金型温度が低すぎると硬化が不完全になり、物性が低下します。 金型温度は、コピー パーツの寸法精度に直接関係します。
3: ポリウレタン樹脂はあらかじめ脱気されています。 A液とB液の2液をそれぞれ真空ボックス内で30分以上真空脱泡処理した。
4: 注射。 A液とB液の入った容器をそれぞれ作業室に置きます。 作業室の排気後、B液を時々かき混ぜて5~10分脱泡し、A液をB液に注ぎ、30~40分かき混ぜ、手早くシリコーンゴム型に流し込む。 そして、混合開始から1分~1分30秒以内に大気圧復帰操作を行う。
5:硬化。 5~30℃のインキュベーターで60~60分硬化後、脱型可能です。 必要に応じて70~2℃のインキュベーター内で3~70時間二次養生を行ってください。

真空鋳造のメリット
金型の低コスト、生産サイクルの大幅な短縮は、小ロット向けの費用対効果の高い生産プロセスの XNUMX つです。
より複雑な構造と均一な肉厚の部品だけでなく、大量の部品を少量でコピーできます。
安定した寸法精度。



真空鋳造のデメリット
肉厚が等しくなく、構造が非常に複雑な部品は、収縮により通常の公差から逸脱する場合があります。
シリコンモールドの耐用年数は短く、通常は 15 ~ 25 コピーしか作成できませんが、これは部品の複雑さにも依存します。
部品を大量に製造するのはコスト効率が悪い
射出成形とは何ですか?
射出成形 熱可塑性樹脂または熱硬化性樹脂で作られた部品を製造するプロセスです。 射出成形とは、射出成形機のバレル内でプラスチックが流動状態のときに加熱して溶かすことです。 プランジャーまたはスクリューの圧力下で、溶融プラスチックは圧縮されて前方に移動し、バレルの前端にあるノズルから非常に高速で低温の閉じた金型に射出されます。 一定時間冷却して硬化させた後、金型を開いて部品を得ます。 射出成形は、複雑な形状のプラスチック部品の大量生産に適しています。 重要な大量処理方法の一つであり、さまざまな産業や分野でも広く使用されています。

射出成形の利点
生産速度が速く、効率が高く、コストが低く、操作を自動化できます。
素材や色の選択肢が多く、形状はシンプルなものから複雑なものまで、サイズは小さいものから複雑なものまでさまざまです。
正確な寸法、優れた表面効果、複雑な形状と構造を持つ部品を大量に製造できます。
射出成形の欠点
金型の初期投資コストが高い。
金型の構築時間は長く、通常は最大 4 ~ 8 週間です。
金型のメンテナンス費用が高くなります。
真空鋳造と射出成形の比較
金型費。 射出成形金型 (スチールまたはアルミニウムの金型) のセットを構築するコストは、真空射出成形金型 (シリコン) の数百倍または数千倍になります。 金型に使用される材料、金型の構造と製造方法、および金型の耐用年数は、金型のコストに影響します 真空鋳造で使用されるシリコーン金型は、構築が非常に簡単で、少量生産にのみ適しています. しかし、射出成形に使用される鋼製金型には、さまざまな精密加工が必要です。 さらに、金型構造も非常に複雑で、金型の耐用年数は比較的長いです。 通常、1000K 以上の部品を生産できます。 射出成形に使用されるアルミニウム金型の場合、金型のコストは硬質金型よりもはるかに低くなりますが、耐用年数はスチール金型よりもはるかに短くなります。 通常、10K-20K の部品を生産できます。 また、金型製作時間は鋼金型よりも短くなります。 アルミ金型は、一般的にラピッド ツーリングとして知られています。
量。プロジェクトが開発の初期段階にあり、設計と機能の検証に少数のプラスチック部品しか必要としない場合、真空射出成形は間違いなく最も費用対効果の高いオプションです。 プロジェクトが大量生産を実装した後、必要な部品の数が 200 ~ 20K の間である場合は、高速のアルミ金型を選択することをお勧めします。 ただし、20 万個を超える部品が必要な場合は、スチール製の金型を選択する方が費用対効果が高くなります。
材料。真空射出成形部品の材料は、最終製品の材料をシミュレートすることしかできませんが、完全に置き換えることはできません。 非常に必要な特性を持つ一部の部品については、射出成形製造で製造に同じプロセスと材料を使用できます。
納期。スチール金型とアルミ金型の製造には通常、より複雑で精密な機械加工が必要であり、準備には通常数週間かかるため、射出成形の納期は金型製作時間と射出成形時間に分けられ、リードタイムは最大で2ヶ月。 一方、真空注型に使用されるシリコン型は非常に短い時間で作成でき、通常はシリコン型と部品の製造が完了するまでに XNUMX 週間しかかかりません。
個々の部品コスト。一般的に言えば、真空鋳造の部品コストは、射出成形よりもはるかに高くなります。これは、製造できる部品の数がかなり少なく、手作業が多いためです。 ただし、真空鋳造の全体的なコストは、工具と材料のコストが低いため、一般に射出成形よりもはるかに低くなります。
プラスチック部品に最適な製造プロセスを選択してください
どちらの製造方法にも長所と短所があります。 設計に最適な製造技術を直接判断する方法はありません。 最終的には、設計している部品またはプロトタイプに依存します。 より良いソリューションを選択するには、次の点を考慮する必要があります。
研究開発・試作・量産のどの段階ですか?
部品に必要な数量は?
具体的な設計パラメータは何ですか?
どの製造技術を使用するかを最終決定できなくても問題ありません。 と連絡するだけ DDプロトタイプ (中国にあるプロトタイプメーカー)より多くの技術サポートを得るために。 その他様々な成形加工により、ご要望に応じた樹脂部品の製作が可能です。