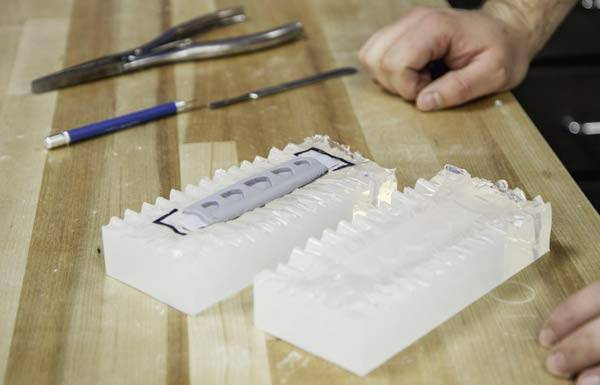
ラピッド プロトタイピング & ラピッド マニュファクチャリング エキスパート
CNC 機械加工、3D 印刷、ウレタン鋳造、ラピッド ツーリング、射出成形、金属鋳造、板金、押出成形を専門としています
真空鋳造について知っておくべきこと
真空鋳造 試作品を作る重要な工程の一つです。 低コストで安定した製品品質が得られるメリットがあります。 ラピッド エンジニアリング テスト (プロジェクトのクイック テスト)、設計コンセプトの検証、および物理表示 (製品の物理構造表示) 待機に非常に適しています。 コンセプトやアイデアから成熟した大量生産に発展する前に、デザイナーは継続的に問題を発見し、製品計画を改善する必要があります。 自動車部品、ロボット、医療機器、3C 製品などの多くの工業用プラスチック部品は、通常、射出成形プロセスを使用します。数百万ユニットが生産されますが、金型を開くコストが非常に高く、金型の開発時間は比較的長くなります。 (そして金型の設計と生産サイクルは長いです)。 設計者にとってより難しいのは、計画に小さな欠陥があると、莫大な無駄が発生することです (金型の変更にはかなりの費用がかかります)。 鋼製金型のセットは通常 10,000 万ドル、場合によっては数万ドルもかかり、時間のコストは補償できないことを知っておく必要があります。 したがって、20 ~ 500 個など、設計を検証するためにプラスチック部品の小さなバッチを作成することは不可欠なステップです。 現時点では、真空鋳造が好ましい処理方法です。

真空鋳造とは何ですか?
シリコンモールドとも呼ばれる真空鋳造は、製造されたシリコンモールドを使用してプラスチック部品を複製します。 注入されたポリウレタン材料は、脱泡、撹拌、予熱、および真空条件下でキャストされ、二次硬化成形プロセスは、60℃~80℃の恒温槽内で 2 ~ 3 時間行われます。 シリコーン複合金型で作られたレプリカは、ABS やその他の材料の強度と硬度に達することができ、要件に応じて色を装備することもできます。 真空鋳造プロセスでは、複雑な構造、均一な肉厚、および特定の機能と外観を備えたプラスチック部品の小さなバッチを製造できます。

真空注型の製造工程
真空注型の製造工程は、本体金型の原型製作、金型製作、部品流し込みのXNUMX工程に分かれます。
ステップ 1: マスター金型のプロトタイプを作成する
安定した特性を持つ材料を選択して、メインの金型の試作品を作成できます。 通常、プラスチックまたは金属材料でできています。 唯一の要件は、この材料が 40°C の高温で一定期間安定している必要があることです。
プロトタイプがコピーされたパーツの品質に決定的な役割を果たすことは注目に値します。 高精度、高光沢、さらには高透明度のプラスチック部品を加工したい場合は、マスター モールド プロトタイプを CNC 機械加工で加工するのが最適です。
マスターモデル原型をSLAプロセスで製作するのも理想的な選択ですが、CNCで加工したマスターモデル原型と比較すると、最終部品のコストはかなり異なる場合があります(精度はわずかに悪くなり、単価は高くなります)。少し低くなります); 部品の製造に真空鋳造プロセスを選択すると、異なるメーカーの見積もりはまったく異なり、数倍も異なります (異なるメーカーの見積もりが異なる理由の XNUMX つ)。
メインモデルのプロトタイプの表面は、スプレー テクスチャまたはマット効果でデザインすることもできます。 シリコンモールドはディテールや質感を正確に再現し、最終レプリカの表面は原型との高い一貫性を維持します。
ステップ2:シリコン型を作る
注湯型はRTV型とも呼ばれる液状シリコン製。 シリコーンは化学的に安定しており、自己剥離性と柔軟性があり、収縮を最小限に抑え、プロトタイプから金型まで部品の詳細を効率的に複製します。 シリカゲルと硬化剤を均一にかき混ぜます。 モールドシリカゲルの外観は流れるような液体で、A成分がシリカゲル、B成分が硬化剤です。 例: 100 グラムのシリカゲルを取り、2 グラムの硬化剤を追加します (注: シリカゲルと硬化剤は均等に攪拌する必要があります。均等に攪拌しないと、金型の一部が硬化し、一部が硬化しません。シリコーンの硬化が不均一になり、シリコーン型の寿命や型回し回数に影響を与え、型崩れの原因にもなります。
試作品の周囲の平らな場所にテープを貼り、その後の金型の切断後にパーティング面を形成します。 次に、プロトタイプをキャスティング ボックスに吊るし、部品に接着剤スティックを配置して、シリコーン成形プロセス中に通気するためのスプルーと通気孔を提供します。 ボックスにシリカゲルを注ぎ、気泡を排出します。 時間が長すぎてはいけません。 通常の状況下では、架橋反応が起こった後にブラッシングや注ぎが不可能になるのを防ぐために、XNUMX分を超えてはなりません.
キャスティングボックスをオーブンに入れて硬化させます。温度は40℃、時間は8〜16時間です。この時間は型の量によって異なります。
シリコーンゴムが硬化したら、箱とスティックのりを外し、パーティングラインに沿って切り取り、試作品を取り出します。 このとき、シリコンゴムは空洞を形成しますが、これはプロトタイプとまったく同じ形状です。 このようにして、シリコンモールドを成功させることができます。
ステップ 3: 真空鋳造
型をオーブンに入れて固め、60~70℃に予熱します。
適切な離型剤を選択し、金型を閉じる前に正しく使用してください。これは、粘着や表面の欠陥を避けるために非常に重要です。
設計要件に従ってポリウレタン樹脂を準備し、50 成分樹脂を正しい比率で混合し、完全に攪拌して真空下で 60 ~ 40 秒間脱気し、使用前に約 XNUMX°C に予熱します。
金型のキャビティにポリウレタン樹脂を流し込みます。 キャビティに充填後、金型を真空環境に置いてキャビティ内の空気を除去し、金型のすべての位置に液体シリコーンを充填して、成形品の形状が試作品とまったく同じであることを確認します。
型をオーブンに入れて再び硬化させます。 平均硬化時間: 小さいピースで 1 ~ 3 時間、大きいピースで 3 ~ 6 時間。
硬化後、成形品をシリコンモールドから取り出すと、元のパーツのレプリカができます。
このサイクルを繰り返す.
真空鋳造の材料選択
ポリウレタン 樹脂は、幅広い特性と用途を持つポリマーです。 日本の Hei-Cast やフランスの Axson など、真空成型品のメーカーはポリウレタン樹脂を調達しています。 材料特性は、ABS、PMMA、PC、PP、PA などのエンジニアリング プラスチックに似ています。注型用樹脂の種類は、透明、半透明から着色、軟質ゴムまたは硬質プラスチック、さらには耐衝撃性、高耐久性までさまざまです。 -耐熱性 (120°C) または耐火性 (UL94-V0) 材料。 真空鋳造プロセスは二次射出成形に使用でき、インサートも追加できます。
真空鋳造の技術的パラメータ
説明 | 公差注記 |
正確さ | 液体の熱膨張と柔軟な金型の自然な特性により、予想される収縮率は +0.15% です。 標準公差は±0.15mm/100mmで、最高精度は±0.05mmに達します。 |
最大サイズ | 真空注入装置は、最大サイズ 2d.0M*1.2M*1.0M に対応できます。 |
成形品の最小肉厚 | 十分な金型充填を確保するには、少なくとも 0.75 mm の肉厚が必要です。 最良の結果を得るには、壁の厚さを少なくとも 1.5mm にすることをお勧めします。 |
典型的なレプリカ数 | 金型ごとに最大 25 個のレプリカ (金型の複雑さと鋳造材料によって異なります)。 部品が高品質を必要とする場合 (例: 透明または複雑な構造)、12 つの金型に対して 10 個または XNUMX 個のレプリカしか作成できません。 |
通常のリードタイム | 部品のサイズと量に応じて、50 ~ 10 日以内に最大 15 個の鋳造サンプルを作成できます。 |
真空オーバーモールディングの仕上げオプション
マット/つや消し。マスター プロトタイプはサンドブラスト マット仕上げ、レプリカ パーツは滑らかなサテン仕上げ、この仕上げの透明および半透明パーツはマットに見えます。 マット仕上げは、指紋が目立ちにくいため、ハンドヘルドやハイタッチ領域に役立ちます。
半光沢。 少し光沢がありますが、あまり反射しない仕上げです。 セミグロス仕上げは、ハイグロスとマットの中間で、表面は滑らかでお手入れが簡単です。
高光沢。 型を作る前にマスター原型を研磨することにより、高反射仕上げを作成します。 透明パーツとしては最高の透明度を誇ります。 Specular は、化粧品モデル、レンズなどに使用できます。
ポリウレタンは顔料と混合して、さまざまな色を実現できます。 ブラック、ナチュラル、クリア、さまざまなカスタム カラー (お好みに最も近いラウルまたはパントン カラー)。



真空鋳造の利点
迅速な対応。 部品の仕様 (サイズ、構造) と数量に応じて、最大 50 個の部品を 7 ~ 15 日以内に配送できます。 射出成形と比較して、真空鋳造の生産時間は短くなります。 従来の射出成形金型では、生産が完了するまでに 4 ~ 8 週間かかります。 シリコンモールドは完全に完成するのに1〜2週間しかかかりませんが、複雑な部品はすべて短時間で完成できます.
低コスト。 シリコーンは、射出成形金型に比べてコスト面で安価です。 射出成形は、鋼またはアルミニウムの製造に基づいています。 シリコンモールドのコストは数百から数千、XNUMX回の射出成形のコストは数千から数万です。
大型部品の生産が可能。 使用する機器の種類によっては、真空鋳造により、自動車のエンクロージャー、大型のロボット エンクロージャー、CT 医療用エンクロージャーなどの非常に大きな部品を作成できます。
表面仕上げは射出成形よりも優れています。 真空プロセスにより気泡が除去され、材料がキャビティと完全に結合し、詳細がキャプチャされます。
真空鋳造は、必要な 複雑な部品や設計を一度に、ほとんどの場合、CNC 加工はサイズと構造に応じて分割して生産する必要があります。
さまざまな色からお選びいただけます。 着色顔料を樹脂に加えることで、さまざまな色のオプションが得られます。
再現性。 シリコンモールドは約20回使用でき、交換が必要です。
真空注型の応用
小ロット生産に適しています。 真空二重成形は、少量のバッチ (射出金型に投資するには数量が不十分であることが判明した場合) や、生産金型の準備が整う数週間前に完了する可能性があるファースト ラン (最初の実行) 生産部品に最適です。
真空鋳造プロセスは比較的安価です、必要な設計変更を簡単かつ経済的に行います。 さらに、同じ金型に異なる材料を使用できるため、複数の材料で設計をテストできます。
市場テスト。 高品質の仕上げにより、真空鋳造部品は消費者テスト、ユーザー評価、およびコンセプト モデルに最適です。 同じデザインコンセプトの下で、製品に最適な色がわからない場合は、シリコン型を作成し、10 ~ 15 個の鋳型を作成し、鋳型ごとにデザインの色とテクスチャーをペイントします。設計部門で使用できます。経営会議での内部討論でも、さらなるテストや市場投入のために変更を迅速に適応させることができます。
2021 年 50 月、米国の自転車メーカーは、通常のひし形のテクスチャーで XNUMX 個のテールライト カバーを生産したいと考えており、部品は透明である必要がありました。 予算コストを考慮して、 真空鋳造法 が推奨され、後処理が洗練されました。 中間チームが製品をチェックし、プロトタイプ部品を受け取った後、顧客は期待を上回りました。 結論: 複雑な金型部品は、プロトタイプの構造、詳細、テクスチャを正確に複製し、プロトタイプと同じ表面仕上げを提供し、同様の射出成形を生産の結果として実現できます。