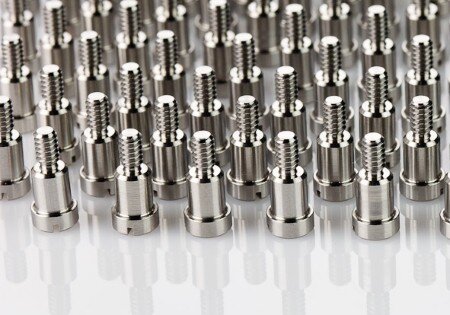
Expert en prototypage rapide et fabrication rapide
Spécialisé dans l'usinage CNC, l'impression 3D, la coulée d'uréthane, l'outillage rapide, le moulage par injection, la coulée de métal, la tôlerie et l'extrusion
Les services de finition pour les pièces usinées CNC
Dans le domaine de Usinage de précision CNC, les performances de travail et la durée de vie des pièces avec des exigences élevées en matière de résistance et de ténacité sont étroitement liées à leurs propriétés de surface. Et l'amélioration des propriétés de surface ne peut pas être obtenue uniquement en s'appuyant sur les matériaux, car elle est très peu économique, mais il est nécessaire de faire en sorte que ses performances soient conformes à la norme dans le traitement réel. À l'heure actuelle, nous devons utiliser diverses technologies de services de finition. Le traitement de surface est le processus de formation artificielle d'une couche de surface sur la surface d'un substrat qui est différente des propriétés mécaniques, physiques et chimiques du substrat grâce à des techniques de traitement spécifiques. De plus, pour l'usinage CNC de pièces métalliques de précision, afin de répondre aux objectifs de résistance à l'usure, de résistance à la corrosion, d'isolation, de décoration, d'amélioration de la durée de vie ou d'ajout d'autres fonctions spéciales, nous adoptons généralement des services de finition spécifiques pour répondre aux exigences. Pour le traitement de surface de pièces métalliques personnalisées, les techniques courantes que nous voyons sont l'anodisation, la galvanoplastie, le polissage électrolytique, la passivation, le brossage, le sablage, la peinture et le revêtement en poudre, etc.
Oxydation électrochimique des métaux ou alliages. L'aluminium et ses pièces en alliage forment un film d'oxyde (isolant) sur les pièces en aluminium (anode) sous l'action d'un courant appliqué dans l'électrolyte correspondant et les conditions de processus spécifiques. L'anodisation fait généralement référence à l'anodisation à l'acide sulfurique, sauf indication contraire. Afin de surmonter les défauts de dureté de surface et de résistance à l'usure des pièces en alliage d'aluminium, d'élargir le champ d'application et de prolonger la durée de vie, la technologie de traitement de surface est devenue un élément indispensable de l'utilisation des pièces en alliage d'aluminium, et la technologie d'anodisation est la plus largement utilisé et le plus économique. À l'heure actuelle, il existe deux principaux types d'anodisation : l'anodisation à l'acide sulfurique de type II et l'anodisation dure de type III (revêtement dur).

Anodisation de type II
Le procédé d'anodisation à l'acide sulfurique de type II est la méthode d'anodisation la plus courante. Les films du procédé d'anodisation à l'acide sulfurique varient de 0001″ à 001″ d'épaisseur. L'épaisseur globale du revêtement formé est de 67 % de pénétration dans le substrat et de 33 % de croissance par rapport à la dimension d'origine de la pièce. Il est particulièrement adapté aux applications où la dureté et la résistance à l'abrasion sont requises. Cependant, lorsque les pièces sont soumises à des contraintes considérables (comme les pièces d'avion), la présence éventuelle de résidus d'acide corrosif n'est pas souhaitable. La nature poreuse des films d'acide sulfurique avant le scellement est particulièrement mise à profit dans la production de finitions de surface colorées sur l'aluminium et ses alliages.
L'oxyde d'aluminium poreux absorbe bien les colorants et le scellage ultérieur aide à prévenir la perte de couleur en service. Bien que les films anodisés teints soient raisonnablement inaltérables, ils ont tendance à blanchir sous la lumière directe du soleil prolongée. Certaines des couleurs sont : noir, rouge, bleu, vert, gris urbain, brun coyote et or. Les pièces peuvent être traitées chimiquement ou mécaniquement avant l'anodisation pour obtenir une finition mate (non réfléchissante).

Avantages de l'anodisation à l'acide sulfurique :
Moins cher que les autres types d'anodisation en ce qui concerne les produits chimiques utilisés, le chauffage, la consommation d'énergie et le temps nécessaire pour obtenir l'épaisseur requise.
Plus d'alliages peuvent être finis.
Plus dur que l'anodisation chromique.
Une finition plus claire permet de teindre avec une plus grande variété de couleurs.
Le traitement des déchets est plus facile que l'anodisation au chrome, ce qui contribue également à réduire les coûts.
Applications d'anodisation d'acide sulfurique :
Composants optiques
Corps de vannes hydrauliques
Armes militaires
Boîtiers informatiques et électroniques
Matériel mécanique
Anodisation dure de type III
L'anodisation dure de type III (revêtement dur), bien qu'elle soit généralement effectuée dans un électrolyte à base d'acide sulfurique, est beaucoup plus épaisse et plus dense que l'anodisation sulfurique plus conventionnelle. Hardcoat est spécifié pour les composants en aluminium soumis à des applications d'usure extrême où une résistance supérieure à l'abrasion est nécessaire, ou des environnements corrosifs où un revêtement plus épais, plus dur et plus durable est nécessaire. Il peut également être utile lorsqu'une isolation électrique améliorée est requise. Étant donné que l'anodisation dure peut atteindre plusieurs millièmes dans certains cas, elle fait de ce type d'anodisation un candidat pour la récupération de composants usés ou mal usinés.

Caractéristiques de l'anodisation dure :
Meilleure résistance à l'usure
Non conductrice
Peut réparer les surfaces usées sur l'aluminium
Améliorer la surface des pièces pour les applications de glissement
Peut être teint en noir; autres couleurs moins décoratives
La finition est plus dure que l'acier à outils
Peut être rectifié ou rodé
Applications d'anodisation dure :
Valves
Pistons
Pièces coulissantes
Mécanismes de charnière
Cames
Engrenage
rotules
Plaques d'isolation
Boucliers anti-souffle
Services de finition : galvanoplastie
La galvanoplastie est le processus d'application d'une ou plusieurs couches d'un métal sur une pièce en faisant passer un courant électrique chargé positivement à travers une solution contenant des ions métalliques dissous (anode) et un courant électrique chargé négativement à travers votre pièce à plaquer (cathode). L'histoire remonte aux anciens Égyptiens qui recouvraient les métaux et les non-métaux d'or ou d'un procédé connu sous le nom de "dorure", la première finition de surface connue. Certains métaux s'appliquent plus uniformément que d'autres, mais l'utilisation de l'électricité signifie que le métal déposé s'écoule plus facilement vers les zones à courant élevé ou les bords d'une pièce. Cette tendance est particulièrement prononcée sur les formes complexes ou lorsque vous essayez de plaquer l'intérieur ou la partie ID d'une pièce.

Types de galvanoplastie :
Cadmium
Cuivre
Or
Chrome dur
Nickel
Argent
Étain
Étain-Plomb
Zinc
Zinc-Fer
Nickel noir
Chrome noir
Caractéristiques de la galvanoplastie :
Résistance à la corrosion
Résistance à l'usure
Aspect
Lubricité
Solderability
Applications pour la galvanoplastie :
Armement militaire
Instruments de diagnostic médical
Optiques
Outils et matrices
Composants d'aéronefs
Composants de la machine
Appareils électroniques et informatiques
Boîtiers, châssis et dissipateurs thermiques
Ensembles mécaniques
Services de finition : électropolissage
Le polissage électrolytique est le processus de lissage et/ou de brillantage anodique d'une surface métallique dans une solution acide ou alcaline concentrée. Configurez-le pour l'exécuter sur de l'acier inoxydable ou d'autres alliages riches en nickel. Bien que cela puisse être fait sur de nombreux métaux de base en tant qu'opération de préplaquage, cela se fait généralement sur l'acier inoxydable comme finition finale. Il fournit une surface chimiquement et physiquement propre et élimine toutes les aspérités de surface mécaniques qui peuvent être préjudiciables à la production de surfaces galvanisées uniformes et sans piqûres ou à la performance et à l'apparence futures d'un produit en acier inoxydable. Il aide à ébavurer les bords et les trous usinés ainsi qu'à éliminer tout fer incrusté du processus de fabrication. Le courant est le plus fort sur les bords extérieurs et les coins extérieurs des pièces, qui sont particulièrement lisses. Plus le processus est long, plus la quantité de métal enlevée est importante : les trous peuvent être agrandis, les filetages peuvent être arrondis et les arêtes vives peuvent être lissées.

Caractéristiques de l'électropolissage :
Apparence améliorée
Élimination des bavures
Microfinition rentable
Éviter les frottements, les fuites et l'usure
Passivation/Nettoyage
Applications de l'électropolissage :
Implants et dispositifs médicaux
Équipement de transformation et de manutention des aliments
Équipement pharmaceutique/de laboratoire
Engrenages et cannelures
Services de finition : passivation
La passivation est utilisée pour améliorer l'état de surface de l'acier inoxydable en dissolvant le fer qui est incrusté dans la surface par formage, usinage ou autres étapes de fabrication. Si on le laisse rester, le fer se corrode et donne souvent l'apparence de grandes ou petites taches de rouille sur l'acier inoxydable. Afin d'éviter cet état sur les pièces finies, celles-ci subissent un traitement de passivation. Ce traitement, qui consiste à immerger les pièces en acier inoxydable dans une solution d'acide nitrique sans sels oxydants pendant une durée déterminée, va dissoudre le fer incrusté et restaurer la surface d'origine résistante à la corrosion en formant une fine pellicule d'oxyde transparente. La passivation est utilisée comme opération de nettoyage pour les moulages, les estampages et les pièces de machines finies en immergeant les pièces.

Caractéristiques et avantages:
L'acier inoxydable n'a pas besoin d'être plaqué pour obtenir une protection maximale contre la corrosion
Fournit une surface propre supérieure
Aucune décoloration par la rouille de l'acier inoxydable en service
Préparation de surface pour d'autres finitions telles que l'apprêt ou la peinture
L'acier inoxydable passivé ne réagit pas avec d'autres matériaux en raison de la contamination par le fer
Applications :
En général, lorsque la contamination par le fer nuit aux performances d'une pièce
Stérilisation d'outils et d'équipements dans le domaine médical, y compris les implants
L'industrie alimentaire comme les mélangeurs, les réservoirs, les équipements de manutention, les blindages et les fixations
Dans les domaines de l'architecture ou de la marine où les finitions de surface doivent durer des décennies
Commandes du système de carburant aérospatial
Liste des processus/spécifications :
AMS 2700
AMS QQ P35
ASTM A 380
ASTM A 967
MILS 5002
Services de finition : Brossage
Le traitement de surface brossé est une méthode de traitement de surface qui forme des lignes sur la surface de la pièce en meulant le produit, ce qui a un effet décoratif. Parce que le traitement de surface brossé peut refléter la texture des matériaux métalliques, il a été apprécié par de plus en plus d'utilisateurs et de plus en plus largement utilisé. La méthode de traitement de la surface brossée doit choisir différentes méthodes de traitement en fonction des exigences de l'effet de brossage, de la taille et de la forme des différentes surfaces de la pièce. Il existe deux modes de brossage de surface : le brossage manuel et le brossage mécanique.

Services de finition : sablage
Le processus de nettoyage et de rugosité de la surface du substrat par l'impact du flux de sable à grande vitesse. L'air comprimé est utilisé comme puissance pour former un faisceau de jet à grande vitesse pour pulvériser le matériau de pulvérisation (sable de minerai de cuivre, sable de quartz, émeri, sable de fer, sable de Hainan, etc.) à la surface de la pièce à traiter à haute vitesse, de sorte que l'apparence ou la forme de la surface extérieure de la surface de la pièce change. En raison de l'impact et de l'effet de coupe de l'abrasif sur la surface de la pièce, la surface de la pièce peut obtenir un certain degré de propreté et une rugosité différente, de sorte que les propriétés mécaniques de la surface de la pièce sont améliorées, améliorant ainsi la résistance à la fatigue de la pièce, augmentant l'adhérence du revêtement, prolonge la durabilité du film de revêtement et facilite également le nivellement et la décoration de la peinture.

Services de finition : revêtement en poudre
Le coût de la poudre utilise le phénomène de décharge corona pour faire adsorber le revêtement en poudre sur la pièce. Le processus de revêtement en poudre est : le pistolet de pulvérisation de poudre est connecté à l'électrode négative, la pièce est mise à la terre (électrode positive), le revêtement en poudre est introduit dans le pistolet de pulvérisation par le système d'alimentation en poudre au moyen de gaz à air comprimé, et un une haute tension générée par un générateur électrostatique haute tension est ajoutée à l'avant du pistolet de pulvérisation. Une charge dense est générée à proximité. Lorsque la poudre est pulvérisée par la buse du pistolet, elle forme un circuit pour former des particules de peinture chargées, qui sont attirées vers la pièce avec la polarité opposée en raison de la force électrostatique. Plus l'accumulation est importante, lorsqu'elle atteint une certaine épaisseur, en raison de la répulsion électrostatique, l'adsorption ne se poursuivra pas, de sorte que toute la pièce pourra obtenir un revêtement en poudre d'une certaine épaisseur, puis la poudre sera fondue, nivelée, et solidifié par la chaleur, c'est-à-dire qu'il forme un revêtement dur à la surface des pièces.
