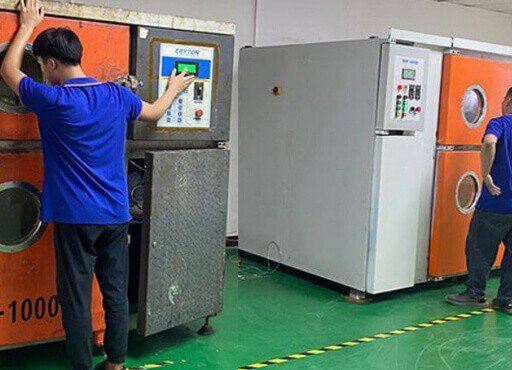
Expert en prototypage rapide et fabrication rapide
Spécialisé dans l'usinage CNC, l'impression 3D, la coulée d'uréthane, l'outillage rapide, le moulage par injection, la coulée de métal, la tôlerie et l'extrusion
Processus de formage plastique courant coulée sous vide
Il existe de nombreux processus de formage pour les pièces en plastique, y compris le moulage par injection, le soufflage, le moulage par extrusion, le moulage sous blister, le moulage sous vide, etc. Chaque processus de formage du plastique a ses avantages et ses inconvénients uniques. Aujourd'hui, nous allons nous concentrer sur la présentation de la procédure de travail, les avantages et les inconvénients du processus de coulée sous vide, ainsi que le matériau commun utilisé pour la coulée sous vide, etc.
Qu'est-ce que la coulée sous vide?
Coulée sous vide être appelé coulée d'uréthane ou coulée de polyuréthane également, est un processus de fabrication de répliques de pièces en plastique et est l'un des processus les plus économiques pour la formation de pièces en plastique en petits lots. Généralement, créera d'abord un maître par impression 3D ou usinage CNC, puis utilisera le maître pour fabriquer un moule en silicone ou en caoutchouc (actuellement, la plupart est un moule en silicone), injectera de la résine liquide dans le moule sous vide et laissera durcir la fabrication méthode. Les pièces en plastique dupliquées peuvent reproduire avec précision la structure, les détails et la texture du maître et fournir une finition de surface cohérente pour obtenir des résultats similaires à la production de moulage par injection. Il convient à la production d'essais en petits lots dans la phase de recherche et de développement de produits, avec une structure complexe, une épaisseur de paroi uniforme et des échantillons de production d'essai qui répondent à certaines exigences fonctionnelles.

Étapes de traitement de la coulée sous vide
Le processus de fabrication du processus de coulée sous vide est divisé en trois étapes : la fabrication du maître, la fabrication des moules en silicone et la coulée des pièces.
Étape 1 : créer un master
La qualité des pièces en double dépend de la qualité du master, et lorsque vous devez maintenir une haute précision, une haute finition ou même une clarté optique, sa meilleure utilisation Usinage CNC pour créer le maître. De plus, pour les pièces aux formes et structures complexes, nous envisagerons également d'utiliser l'impression 3D pour réaliser le master. Nous pouvons pulvériser une texture ou un effet mat sur la surface du maître pour simuler la texture finale du moule des pièces en plastique. Le moule en silicone reproduira avec précision les détails et la texture du maître, et la surface de la réplique finale maintiendra un degré élevé de cohérence avec le maître.

Étape 2 : Fabriquer le moule en silicone
Le moule de coulée est en silicone liquide, également connu sous le nom de moule RTV. Le caoutchouc de silicone est chimiquement stable, auto-détachant et flexible, minimisant le rétrécissement et reproduisant efficacement les détails des pièces du maître au moule. Les étapes de fabrication du moule en silicone sont les suivantes :
Collez autour du maître sur une zone plane pour un démoulage facile plus tard, qui sera également la surface de séparation du moule en silicone.
Accrochez le maître dans une boîte et placez un bâton de colle sur les pièces pour régler le trou d'ouverture et de ventilation.
Remplissez la boîte de silicone liquide et aspirez-la, puis faites-la durcir dans un four à 40°C pendant 8 à 16 heures, selon la taille du moule en silicone.
Une fois le caoutchouc de silicone durci, retirez la boîte et le bâton de colle, sortez le maître du moule en silicone, puis formez une cavité et le moule en silicone est créé.

Étape 3 : coulée sous vide
Les procédures d'exploitation standardisées de DD Prototype garantissent une reproduction précise des pièces et des performances mécaniques constantes. Nos techniciens contrôlent tous les paramètres de fonctionnement : mélange, dégazage, agitation, préchauffage, coulée et démoulage, fournissant des répliques quasi parfaites du maître. Le processus de coulée sous vide est le suivant :
Mettez d'abord le moule en silicone dans le four et préchauffez à 60-70℃.
Il est très important de sélectionner un agent de démoulage approprié et de l'utiliser correctement avant de fermer le moule pour éviter le collage et les défauts de surface.
Pour préparer la résine de polyuréthane, préchauffez-la à environ 40°C avant utilisation, mélangez la résine à deux composants dans le bon rapport, puis remuez complètement et dégazez sous vide pendant 50 à 60 secondes.
La résine est versée dans le moule à l'intérieur de la chambre à vide et le moule est à nouveau durci dans le four. Temps de durcissement moyen : 1-3 heures pour les petits morceaux, 3-6 heures pour les gros morceaux.
Retirez les pièces moulées du moule en silicone après durcissement. Répétez cette procédure.

Avantages du moulage complexe sous vide
Faible coût du moulage, le traitement de coulée sous vide n'a pas besoin d'investir dans des moules d'injection coûteux et chronophages.
Délai d'exécution rapide, jusqu'à 50 prototypes avec certaines fonctions peuvent être produits en 10 à 15 jours.
Une large gamme d'options de matériaux, les matériaux en polyuréthane pour l'injection sous vide peuvent être rigides, élastiques, transparents et de différentes couleurs.
Haute précision et détails fins. La coulée sous vide peut fournir des pièces de haute précision et de haute précision avec une qualité de niveau de production.
Excellente finition de surface, par rapport au prototype CNC ou à l'impression 3D, le moulage sous vide offre une meilleure qualité de surface.

Matériaux courants utilisés dans la coulée sous vide
Les matériaux utilisés dans la coulée sous vide comprennent les thermoplastiques, le caoutchouc et les résines, qui peuvent tous simuler des propriétés et des caractéristiques spécifiques :
Qualité de l'apparence
Texture/finition de surface
Transparence/Translucidité
Rigidité
Flexibilité
Force
Dureté
Résistance à la température
rayons UV
Couleur
Plus de FAQ sur la coulée sous vide
Quelle est la précision des pièces en plastique dupliquées créées par le traitement de coulée sous vide ?
-La tolérance de précision de réplication standard est de ± 0.15 mm/100 mm, et la précision la plus élevée peut atteindre ± 0.05 mm.
Quelle est la taille maximale de la pièce coulée ?
-L'équipement de coulée sous vide peut accueillir des spécifications de moule de 2.0 M * 1.2 M * 1.0 M.
Quelle est l'épaisseur minimale de paroi des pièces en plastique pouvant être reproduite ?
-L'épaisseur de paroi minimale de la pièce est de 0.5 mm et la meilleure est de 1.5 mm à 2.5 mm.
Quelle est la durée de vie du moule en silicone ?
-Chaque moule peut couler jusqu'à 20 pièces, et si la pièce nécessite une haute qualité (telle qu'une structure transparente ou complexe), un moule ne peut fabriquer que 12 ou même 10 pièces en plastique.
Quel est le délai de livraison général pour le moulage par injection sous vide ?
-Jusqu'à 50 prototypes coulés peuvent être réalisés en 10 à 15 jours, selon la taille et le volume de la pièce.
Traitement de surface et autres fonctions?
– Coloration de la résine liquide, matte etching, polissage transparent, peinture, galvanoplastie, inserts métalliques, surmoulage…
Le processus de coulée sous vide est une méthode efficace pour fabriquer des prototypes fonctionnels et de petits lots de pièces en plastique, et vous aide à équilibrer la production de pièces en plastique de haute qualité avec les délais les plus courts. Si vous souhaitez savoir comment le prototypage peut bénéficier à votre projet, veuillez contacter DD Prototype, nous voulons vous entendre parler de vos projets.